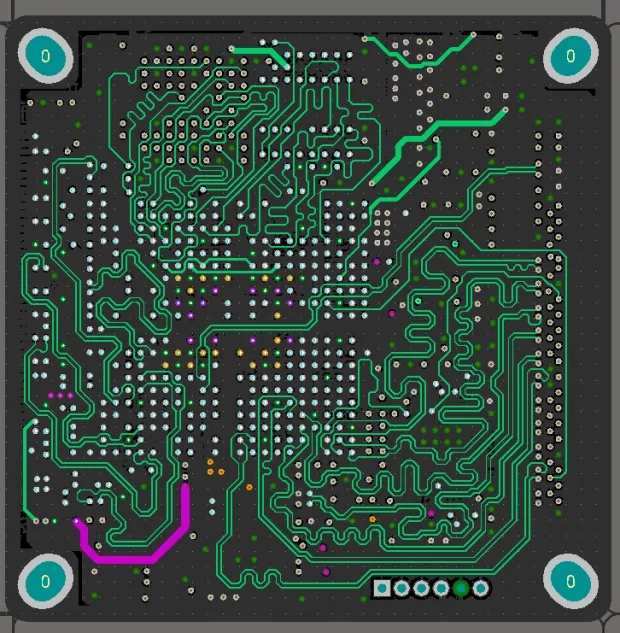
SMD parts changed to through hole solder paste
The boss lost a question today: suppose the same board, change the same part from the original pure SMD part to the traditional plug-in part manufacturing process or SMD solder leg+through-hole positioning column, and use the "through-hole solder paste (PIH, Paste In Hole)". What difference and impact will this have on the production line and design?
At that time, three lines appeared on my head, but I had to start thinking about this question whether I liked it or not. Later, I learned that it was originally a method to prevent the connector from being broken by rude customers.
PIH (Paste in Hole) is sometimes calLED PIP (Pin In Paste).
The first thought is that the traditional plug-in parts in the PIH process must follow the SMT high-temperature reflow process, so the part design must conform to the following specifICations, otherwise it may not pay off:
PIH parts should preferably be packaged with tape&Reel, so that SMT machine can be used to mount/print parts, at least hard tray should be used.
The material of PIH parts must be able to withstand the high temperature of SMT reflow. Generally, PIH parts are required to pass through the furnace on the second side. If they pass through the furnace only once, it is better to withstand at least 260? C lasts for more than 10seconds.
The solder legs of PIH parts shall not have kink or tight fit design, otherwise it will be difficult to place the parts on the board with the machine. If manual operation is reluctantly used to place such parts, it may be necessary to over voltage the circuit board to insert the parts, causing the circuit board vibration, and finally causing the offset or falling of the printed parts on the circuit board.
PIH parts must be designed with a plane at the top of the part so that SMT nozzle can absorb, or a piece of high temperature air leakage proof tape can be pasted on it.
A gap of more than 0.2mm/stand off shall be reserved at the junction of PIH part solder pin and circuit board to prevent siphon phenomenon, resulting in tin overflow, and the problem of uncertain tin bead affecting product function.
It is recommended that the height of the solder leg of PIH parts should be 0.3~1.0mm higher than the thickness of the circuit board. Too long is not conducive to the operation of taking and placing parts, and too short is likely to cause the risk of insufficient tin and easy to fall off, because most of the parts that will use the PIH process are external connectors.
As for the impact of changing pure SMD parts to PIH or SMD+PIH parts on the manufacturing process and products, I will try to summarize several key points below:
Labor hour: There should be no significant difference between the printing time of these two parts.
Cost: The cost of PIH parts may be higher than that of pure SMD because of some perforated PIN pins.
Clearance between SMT parts: According to experience, the clearance between PIH parts should be more than 1.5mm, while that of pure SMD parts should be only 1.0mm, and some can even be reduced to 0.5mm. This is because the weld leg of PIH is easy to deform, so the through-hole will also be designed a little larger. Generally, it is recommended that the ratio of weld leg diameter to through-hole diameter be 0.5~0.8, and the deviation of its punched parts will be relatively large, so a relatively large gap is required.
Rework and repair: Generally speaking, PIH parts are more difficult to rework and repair than pure SMD parts, because the soldering tin in the through-hole needs to be removed when replacing parts, which is a relatively difficult process in terms of current technology. Of course, you can also consider destroying the entire part, but the difficulty of rework of HIP parts is relatively high.
Space utilization rate of the circuit board: because there is a PIN pin sticking out on the back of the PIH part, the space on the circuit board is relatively less.
Tin filling problem: IPC-610 stipulates that the through hole tin eating rate of solder legs of through hole parts must exceed 75%, but sometimes it is difficult to achieve this amount of tin with normal solder paste printing due to the previous restrictions, so sometimes additional solder must be added.
In fact, when SMD parts are changed to plug-in PIH process, their soldering strength will be stronger than that of pure SMD, and they can withstand more or more times of external force plugging. According to past experience, the tolerance can be about 1.5 times, depending on the number of PINs and the thickness of PIN pins.
然后
联系
电话热线
13410863085Q Q
微信
- 邮箱