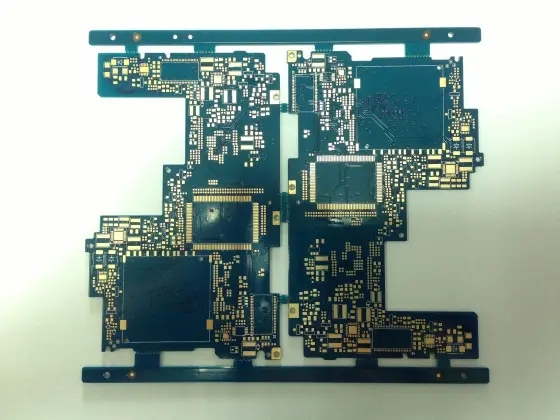
PCB factory: composition and classifICation of solder paste and requirements for selecting solder paste
In the whole process of SMT, solder paste plays an important role in the quality and production efficiency of SMT. Therefore, SMT staff must understand some of their performance and learn to use them correctly.
1、 Main components of solder paste
Solder paste is a homogeneous mixture composed of alloy solder powder, flux, activator and viscosity control agent, which has certain viscosity and good thixotropy, good printing performance and reflow soldering performance, and is stable in storage.
Alloy solder is the main component of solder paste, accounting for 85%~90% of the weight of solder paste. The commonly used lead solders are: Sn, SnPbAg, SnPbBi, etc. The typical alloy composition is Sn63Pb37; Common lead-free solders include SnZn, SnCu, SnBi, SnAg, SnAgCu, SnAgBi, SnZnBi, etc. The shape of alloy solder powder can be divided into spherical and elliptical. Its shape and particle size affect the surface oxidation and fluidity, so it has a great impact on the performance of solder paste.
2、 Classification of Solder Paste
There are many kinds of solder pastes, which can be divided into leaded solder pastes and lead-free solder pastes according to whether they contain lead; According to the melting point, it can be divided into low temperature solder paste, medium temperature solder paste and high temperature solder paste. The melting point of low temperature solder paste is generally less than 150 ℃, and the melting point of high temperature solder paste is generally greater than 250 ℃. Of course, some people are used to calling Sn63Pb37 solder paste medium temperature solder paste. The one below this melting temperature is calLED low temperature solder paste, and the one above this melting temperature is called high temperature solder paste; According to the activity of the added flux, it can be divided into non active, medium active, active and extremely active solder pastes. Medium active solder pastes are commonly used. According to the cleaning method, it can be divided into organic solvent cleaning, water cleaning, cleaning free, etc.
Basic requirements for selection of solder paste
As many defects in SMT production are caused by improper selection and use of solder paste, it is very important to standardize the use of solder paste.
SMT has the following requirements when selecting solder paste:
(1) It has a long storage life and can be stored at 0~10 ℃ for 3~6 months. During storage, there will be no chEMIcal change, no separation of solder powder and flux, and its viscosity and adhesion will remain unchanged.
(2) It has a long working life. It is usually required to be kept at room temperature for 12-24 hours after printing or drip coating, and its performance remains unchanged.
(3) After printing or coating, and during reflow soldering preheating, the solder paste shall keep its original shape and size without blocking.
(4) It has good welding strength to ensure that components will not fall off due to vibration and other factors.
(5) Good wettability. The active agent and wetting agent components in the flux should be selected correctly to meet the requirements of wetting performance.
(6) No solder splash. This mainly depends on the water absorption of solder paste, the type, boiling point and amount of solvent in solder paste, and the type and content of impurities in solder powder.
PCB manufacturers, PCB designers and PCBA manufacturers will explain the main components and classifications of solder paste and the basic requirements for selecting solder paste.
然后
联系
电话热线
13410863085Q Q
微信
- 邮箱