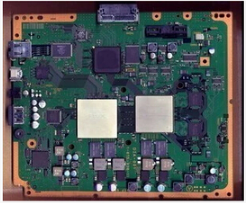
Before producing PCB boards, first understand the possible problems of the circuit boards made, and plan the functions to be realized in advance, so as to ensure the quality of the products more carefully, avoid unnecessary mistakes, and increase the cost when scrapping. It is not cost-effective, so pay great attention to it. In addition, it is necessary to ensure the high effICiency and low error rate of circuit board proofing, which also shows that circuit board proofing needs details
PCB proofing
When there is no isolation transformer, it is strictly prohibited to use grounded test equipment to detect
Even if the general equipment is equipped with a power transformer, it is necessary to understand that the chassis of the machine to be tested is still live, otherwise it is very easy to have a power short circuit. Once the integrated circuit is affected, it will have further impact, and the consequences are unimaginable. The loss is not only economic.
2. Before testing PCB boards, you should first understand the working principles of integrated circuits and related circuits
Before checking an integrated circuit, it is necessary to be familiar with the functions of the integrated circuit, its own parameters and the working principle of the circuit composed of peripheral components, and then to carry out thoughtful repair, so that the process of analysis and inspection will be optimized. This is a good idea. I hope you can learn more.
3. Pay attention to the insulation performance of electric soldering iron before testing PCB board
It is strictly prohibited to use an electrified soldering iron for welding. Before use, make sure that the soldering iron is not electrified. According to basic knowLEDge, ground the shell of the soldering iron. Try to use a low-voltage electric soldering iron (below 8V).
4. Carefully check whether PCB documents are correct
Even senior PCB engineers may inevitably make mistakes. Before proofing, they should strictly review the documents based on previous experience to avoid unexpected mistakes in the subsequent proofing process, which will reduce production efficiency and increase the cost of proofing.
5. Be strict about the layout and wiring of components
The layout and aliasing of components will have a certain impact on the quality of products. Pay attention to the layout order of components, assemble components according to skilled operation, and pay attention to the problem of heat dissipation during layout. Do not place hot PCB components in a centralized manner, and handle the distance between them reasonably.
6. Adjust PCB wiring
Some adjustments need to be made to some of the individual components, and the words on the board should be handled well for future production and debugging. In case of problems, it is also convenient for later maintenance.
7. Use software to conduct SIMulation test before circuit board proofing
Because of the progress of technology, we can now conduct simulation test on the software first. During the operation, we can find problems in advance and conduct pretreatment, which can greatly reduce the workload of later detection, debugging and maintenance.
8. Ensure PCB board quality
During welding, the welding time and power shall be controlled to avoid low-level errors and improve efficiency. Short circuit detection shall be carried out after PCB welding.
9. Consider the number of circuit board samples
Calculate and determine the quantity of proofing according to the specific situation to reduce unnecessary cost loss to a certain extent. After communicating with the customer in advance, we can determine the circuit board to be produced to prevent the wrong consumption of the customer.
然后
联系
电话热线
13410863085Q Q
微信
- 邮箱