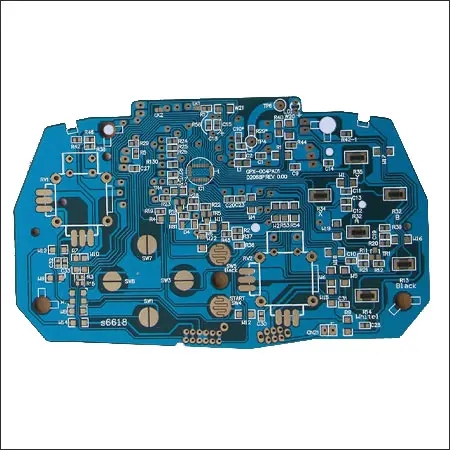
ApplICation of Flux in Wave Soldering in PCBA Processing
Wave soldering flux is the main electronic auxiliary material used for electronic assembly PCBA processing. Its quality directly determines the reliability of subsequent products. Here is a brief introduction to the role of flux in wave soldering.
① Remove the rust film on the surface of the metal to be welded. The rust film on the surface of the metal to be welded is usually insoluble in any solution, but the rust can be removed by chEMIcal reaction with some materials to generate compounds that can be dissolved in liquid blasting aids, so as to purify the surface of the metal to be welded. This chemical reaction can be another compound that makes the flux and the rust film form a solution in the flux or flux solvent, or it can be a chemical reaction that reduces the metal rust film to a pure metal surface. The flux belonging to the first chemical reaction is mainly represented by rosin type flux, and some reducing gases are examples of the second chemical reaction. For example, oxygen can reduce oxides on metal surfaces at high temperatures, generate water and restore pure metal surfaces.
② Prevent secondary oxidation of the weld metal during heating. During wave soldering, the re oxidation of the metal surface will intensify with the increase of temperature, so the flux must provide protection for the cleaned metal surface, that is, the flux should form a film on the entire metal surface to wrap the metal and isolate it from the air, so as to prevent the secondary oxidation of the weld metal during the heating process of welding.
③ Reduce the surface tension of liquid solder. The flux in the welding process can affect the energy balance of the surface in the way of promoting the overflow of solder, reduce the surface tension of liquid solder, and reduce the contact angle.
④ Heat transfer. Generally, there are many gaps in the welded joint head. During the welding process, the air in these gaps acts as a separator, resulting in poor heat transfer. If these gaps are filLED with flux, the heat transfer can be accelerated and the speed of transmission can reach thermal balance.
⑤ Promote the overflow of liquid solder. After the preheat viscous flux contacts with the wave solder, the activity increases dramatically, and the viscosity drops sharply, forming a second overflow on the surface of the metal to be welded, and spreading rapidly on the surface of the metal to be welded. The overflow force formed in the secondary overflow process of the flux is attached to the liquid solder, thus dragging the overflow process of the liquid metal.
Drag effect of secondary flow of solder resist on liquid solder
The flux coating system automatically and efficiently applies the flux to the soldered surface of PCB. The flux is used to break the oxide layer, remove the loose oxide layer from the metal surface, and make the solder directly contact the base metal.
PCB manufacturers, PCB designers and PCBA manufacturers explain the use of flux in wave soldering in PCBA processing.
然后
联系
电话热线
13410863085Q Q
微信
- 邮箱