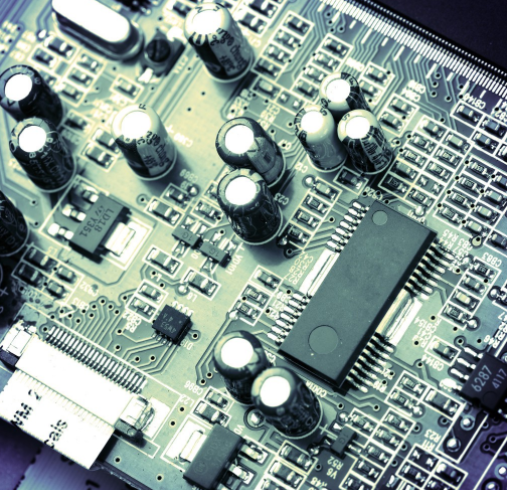
What are the basIC principles of the design for manufacturability of PCBA
PCBA design for manufacturability
1. Optimize surface assembly and crimping parts
surface mounted components and crimping components have good manufacturability. With the development of component packaging technology, most components can be purchased according to the package category suitable for reflow, including plug-in components that can be reflowed through holes. If the design can realize full surface assembly, the assembly efficiency and quality will be greatly improved. Crimping components are mainly multi pin connectors. This package also has good manufacturability and connection reliability, and is also the preferred category.
2. Take the PCBA component as the surface of the object, and consider the package size and pin spacing as a whole
The biggest impact on the overall board manufacturability is the package size and pin spacing. On the prEMIse of selecting surface mount components, for PCB with specific size and assembly density, a group of packages with SIMilar processing efficiency or packages suitable for solder paste printing on a mold with a certain thickness must be selected For example, the selected packages are suitable for solder paste printing with 0.1mm thick steel wire MESh
3. Shorten process path
The shorter the process route, the higher the production efficiency and the more reliable the quality. The preferred routing design is:
Single side reflow welding;
Double side reflow welding;
Double side reflow+wave soldering;
Double side reflow+selective wave soldering;
Double side reflow welding+manual welding.
circuit board
4. Optimize component layout
Component layout design mainly refers to the layout and spacing design of components. The Layout of components must meet the requirements of welding process. Scientific and reasonable layout can reduce the use of bad solder joints and tooling, and can optimize the design of steel mesh.
5. Consider the design of pad, solder mask and mold window as a whole
The design of pad, solder mask and mold window determines the actual distribution of solder paste and the formation process of solder joint. Coordinating the design of bonding pad, solder mask and steel mesh has a great impact on improving the welding pass rate.
6. Focus on new packages
The so-calLED new package software does not completely refer to the package software newly launched in the MARKet, but refers to the package software that the company has no experience in using. For the introduction of new packaging, SMAll batch process validation shall be carried out. Other people can use it, but that doesn't mean you can use it. The prerequisite for use must be to have done experiments, understand the process characteristics and problem spectrum, and master the countermeasures.
7. Focus on BGA, chip capacitors and crystal oscillators
BGA, chip capacitor and crystal oscillator are typical stress sensitive components, and should be placed in PCB welding, assembly, workshop turnover, transportation. In the layout process, they are easy to bend and deform when used
8. Study cases to improve design rules
Design for manufacturability rules are derived from production practices. Based on the continuous occurrence of poor assembly or failure cases, continuous optimization and improvement of design rules are of great significance for improving design for manufacturability.
然后
联系
电话热线
13410863085Q Q
微信
- 邮箱