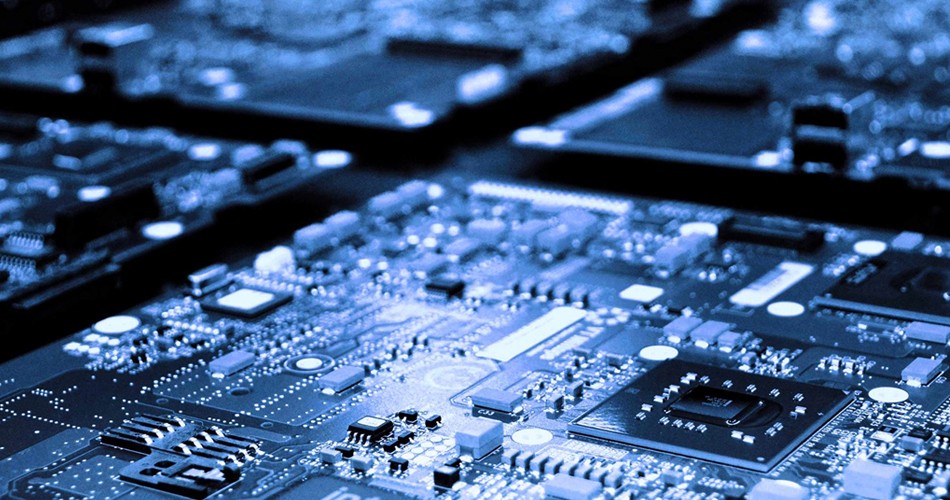
In PCBA processing, what is the strength of car specifICation chip over ordinary chip?
The price of automotive electronic products is generally expensive. One of the main reasons is that PCBA uses electronIC components at the vehicle gauge level in its processing and production. But what kind of electronic components are at the vehicle gauge level? Let's take a look at the differences between the application of electronic components in automobiles and that of general consumer electronics.
1. Environmental requirements
Temperature: Automotive electronics have a wide range of requirements for the working temperature of components. They have different requirements according to different installation locations, but they are generally higher than the requirements for civil products (it is said that AEC Q100 deleted the requirements for the temperature of 0 ℃ - 70 ℃ in Version H, because no automotive product can have such low requirements).
give an example:
Engine periphery: - 40 ℃ - 150 ℃;
Passenger compartment: - 40 ℃ - 85 ℃;
Civil products: 0 ℃ - 70 ℃.
Other environmental requirements such as humidity, mildew, dust, water, EMC and harmful gas erosion are often higher than the requirements of consumer electronics.
2. Vibration
The automobile works in a moving environment, and for many electronic products, it encounters more vibration and impact. This requirement may be much higher than that of products in other use scenarios.
3. Reliability
In order to illustrate the reliability requirements of automobiles, let me explain them in another way:
3.1. design life: the design life of ordinary automobiles is about 150000 years and 200000 kilometers, which is far greater than the life requirements of consumer electronics products.
3.2. Under the same reliability requirements, the more components and links of the system, the higher the reliability requirements of the components. At present, the car has become very electronic. From the powertrain to the brake system, there are a lot of Electronic devices, and each device is composed of many electronic components. If they are SIMply regarded as a series relationship, it is necessary to ensure that the whole vehicle achieves considerable reliability. The requirements for each part of the system are very high, which is why the requirements for auto parts are often described in PPM (one millionth of a million).
4. Consistency requirements
Now cars have entered a stage of mass production. One car can produce hundreds of thousands of cars in one year, so the requirements for product quality consistency are very high. This was a challenge for semiconductor materials in the early years.
After all, it is difficult to control the consistency of diffusion and other processes in the production of sEMIconductors. The performance of the products produced is easy to disperse. In the early days, it can only be completed by aging and screening. Now, with the continuous improvement of the process, the consistency has been greatly improved. The consistency of quality is also the biggest difference between many local suppliers and internationally renowned suppliers. For automobile products with complex composition, it is definitely unacceptable that components with poor consistency lead to potential safety hazards in the whole vehicle.
Here are some other requirements:
As required by the manufacturing process of automobile products, although automobile parts are also constantly developing towards miniaturization and lightweight, compared with consumer products, they can be relatively relaxed in terms of volume and power consumption. Generally, the package used is large, so as to ensure sufficient mechanical strength and meet the manufacturing process of major automobile suppliers.
2. Product life cycle
Although in recent years, the price of automobile products has been continuously reduced, automobiles are still a large durable commodity, and the supply capacity of after-sales parts must be maintained for a long time. At the same time, the development of an automobile part requires a lot of verification work, and the verification work brought by the replacement of components is also huge, so vehicle manufacturers and parts suppliers also need to maintain stable supply for a long time.
3. Standards
In this way, it is really complex to meet the requirements of automotive products, and the above requirements are for automotive parts (for electronic components, it is a system). How to convert the requirements into electronic components becoMES very difficult. In order to solve this problem, there are naturally some specifications and standards, which are generally recognized as AEC standards:
AEC Q100 Requirements for Active Device Components
AEC Q200 Requirements for Passive Device
Of course, I guess many people will also say that there are many enterprise standards of vehicle manufacturers. But I also want to tell you my understanding. The vehicle manufacturer does have relevant standards for general reliability requirements, but it assesses a complete vehicle component (system composed of electronic components), rather than directly addressing the requirements of electronic components (resistance, capacitor, triode, chip, etc.) that make up these components. Although its requirements can be used to refer to the selection of lower level components, they are still very inappropriate for testing electronic components.
4. Verification of vehicle gauge
It is inevitable that some electronic components without AEC Q100/200 certification will be used in actual production. Many vehicle manufacturers will want to carry out some reliability verification to verify whether they meet the requirements of vehicle regulations.
My personal opinion is that this method is not very effective, because these tests can only be necessary and insufficient. It can only be used to deny the availability of the device, but can not be sure that it can be used.
The reason is simple, the number of samples is too SMAll, and the items tested are not sufficient. For semiconductor components, which are manufactured in large quantities, the reliability can be determined by testing a small number of samples. Personally, it is not reliable. Here we can also look at the main certification test items conducted by AEC Q100 to see the differences.
5. Which standard is high?
Who has high requirements for vehicle and work rules. It is generally believed that the order of standards is military>automobile>industry>consumer electronics. However, individuals cannot fully accept this order. Industry is a wide range, and the environment and reliability requirements encountered are also very different. It can be imagined, for example, that the reliability requirements of a large industrial equipment will never be lower than that of a car. (For example, the critical equipment of a large power plant). At the same time, the harsh scale of the environment may far exceed the requirements of cars. It is not simple to say that the requirements of engineering regulations are lower than cars.
6. Disadvantages of using car gauge parts
It is impossible for any choice to have only advantages and no disadvantages. What are the disadvantages of using electronic components of vehicle gauge?
First of all, it is expensive, with high system requirements, high development and verification costs, and low output, which leads to a large part higher cost than consumer electronics. The relatively high threshold also leads to more sales premium.
The second disadvantage is that the selection is difficult. People who play electronics know that today, electronic components are quite rich. There can be many solutions for making products with the same function, and the complexity may vary greatly. But sometimes, in order to meet the requirements of vehicle regulations, they have to give up some highly integrated solutions.
Another obvious disadvantage is that some products are backward in technology, and a lot of verification work has affected the speed of new products coming into the MARKet. At the same time, chip manufacturers generally hope to apply this product to the automotive market after the consumer electronics market is mature. For example, the ARM Cortex A9 processor used in a product developed in 2013 was basically the best product in the automotive market at that time, but the ARM Cortex A57 processor is not uncommon in the consumer market.
7. What is the risk of using electronic components other than those specified in the vehicle regulations
This problem is really complicated, and we have to judge it from many aspects:
7.1. The product has not been certified, but its performance and reliability meet the requirements and have also been verified by a large number of applications. In this case, the risk is relatively small.
7.2. This is a very important point, which is the relationship between components and systems. The performance and reliability of the system are composed of the next level of electronic components. Therefore, under the same design, the use of components other than vehicle gauges must be poor. However, a good design can reduce the performance requirements of components. If a protective measure is well designed and the component failure has a slight impact on the system, it is possible to use non vehicle gauge components to make better products.
Due to the influence of current technology and process limitations, not every electronic component that needs to be used in automobiles can meet the requirements of the so-calLED vehicle specifications. But in order to realize some functions on the car, these components must be used. This situation can be divided into two categories:
a. The safety requirements of this function are high, and deviations are unacceptable
Example: E-CALL function of emergency call. To ensure this function, it is necessary to install backup batteries on the equipment. This function is related to life safety. According to the ASILI (ISO26262) rating of some companies, it is required to reach Grade B.
And we know that it is very difficult to maintain high performance when the battery reaches - 40 degrees. Therefore, the solution of some companies is to wrap the heating resistance wire on the battery and heat it at low temperature to ensure the performance. At this time, the standard of a single element is considered unqualified, but as a part assembly, it can meet the standard requirements of the car manufacturer. This also shows the relationship between enterprise standards and component standards of vehicle manufacturers.
b. This function generally does not involve safety, and deviation can be considered
Such as the LCD screen of the entertainment system. The response and optical properties that may be displayed at low temperatures will be degraded. However, this situation will be accepted by some engineers.
7.3. Some people who are "bold" and not careful only want to verify their performance and reliability in a short time through a small number of samples because of some ideas, such as reducing costs or obtaining better performance. In this case, I can only say that the future depends on character. Nobody knows what will happen.
The above is what the PCBA manufacturer and the circuit bar designer explained to you about the advantages of the car specification chip over the ordinary chip in PCBA processing.
然后
联系
电话热线
13410863085Q Q
微信
- 邮箱