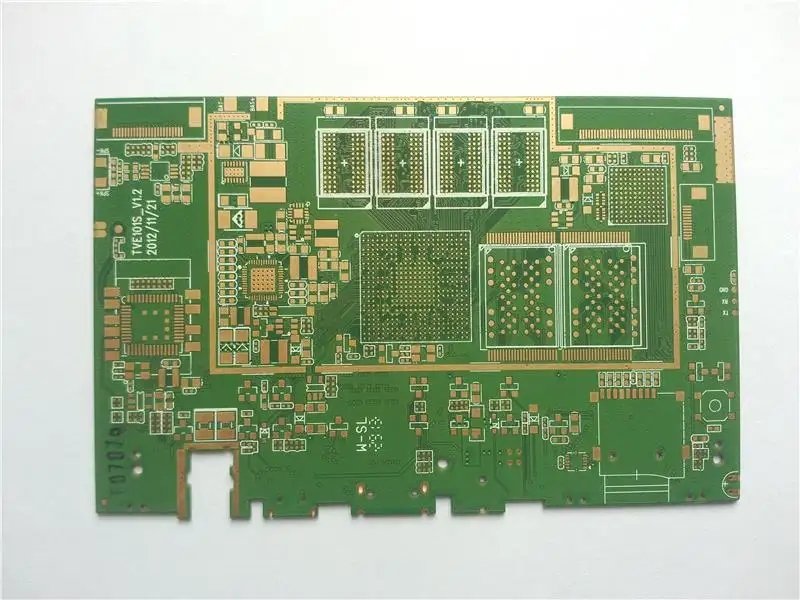
design Considerations for Movable Pieces of Flip type Connector
The circuit board manufacturer and the circuit board designer explain the design considerations of the movable piece of the flip connector
The porous movable sheet design greatly strengthens the mechanICal structure strength of the movable sheet. Early movable pieces were designed as a whole piece. When the number of pins was SMAll, there would be no big problem. However, if the connector was more than 30 pins, it would be easy to warp and deform because the length of the movable piece grew. If the plastic material was chosen carelessly, such as some hygroscopic plastics, it would be brittle after being reflowed in a high temperature furnace, and it would be easy to break in use.
The movable sheet with porous design can effectively enhance the strength of its mechanical structure and reduce the chance of deformation. However, the mold needs more precise design and more precise plastic injection machine, otherwise it is easy to have problems of insufficient injection or too much flash.
▼ For the old flip connector, its movable piece is a plane design of the whole piece. If the number of PIN of the connector is more, it is easier to have deformation problems.
Flip type connector, the old flip type connector, its movable piece is a whole piece of graphIC design. If the number of PIN of the connector is more, it is easier to have deformation problems.
▼ The movable piece of the new connector adopts the porous design, which can not only reduce the plastic materials, but also increase the mechanical strength of the movable piece.
Flip type connector, the movable piece of the new connector adopts the porous design, which can not only reduce the plastic material, but also increase the mechanical strength of the movable piece. It is really a human ingenuity to lock by using the interference between the lower rotating edge of the movable piece and the soft plate, which turns the original mechanism that people think has problems into a design that can solve the problems. Previously, the lower rotating edge of the movable piece of this flip connector would be designed as a radius to avoid the problem of unsmooth rotation caused by the interference between the movable piece and the soft plate (FPC). However, in general, When we assemble the product, we usually only lift the movable piece, insert the FPC, and then cover the movable piece. Most of us only do this once. Therefore, if we only need to use a little effort to cover the movable piece, the user should not pay much attention to it. In addition, the soft plate involved here is a stiffener made of Polyester material, which can withstand a certain amount of compression without damage, It will not cause any side effect.
It is better to make a small round corner at the lower rotating edge of the movable plate, so that it can not only interfere with the soft plate, but also not hurt the soft plate due to the acute angle generated by the right angle.
▼ The new connector design uses the interference between the lower rotating edge of its movable plate and the soft plate to clamp the soft plate and prevent the movable plate from lifting.
The new connector design uses the interference between the lower rotating edge of the movable plate and the soft plate to clamp the soft plate and prevent the movable plate from being lifted. Flip type connector, a new connector design, uses the rotation of its movable piece
The interference between the lower edge and the soft plate is used to clamp the soft plate and prevent the movable plate from lifting.
The locking bump at both ends of the movable piece becoMES smaller or even cancelLED
Some connector manufacturers believe that this new connector design has already used the interference between the lower edge of the rotary movable plate and the soft plate to lock the movable plate, so they reduce or eliminate the small bumps at both ends of the original movable plate.
To be honest, it is necessary to reduce the locking bumps at both ends of the movable piece. Otherwise, too large bumps still need great strength to open the movable piece, and there is still a chance to damage the connector body and the movable piece that are fragile due to high temperature; However, it is not recommended to cancel the whole piece, because without these two small bumps, the movable piece can swing up and down freely. When the SMT machine is picking up and placing the connector, it is very likely that the movable piece will be lifted because the picking up and placing speed is too fast, causing the connector to move away from the SMT nozzle or fall down as a whole. Although slowing down the picking up and placing speed of the SMT can solve this problem, it will affect the efficiency of the SMT somewhat.
Canceling the locking bumps at both ends of the whole movable sheet may also cause other problems. The movable sheet will have a better chance to open itself during the feeding process, which will cause the SMT suction nozzle unable to suck materials. This usually occurs when the SMT feeding gun (feeder) vibrates too much, or the tape on the tape reel has static electricity to suck up the movable sheet. In addition, it may also be damaged due to the opening of the movable piece during the process of taking and transporting the PCA (PCB Assembly).
▼ The two ends of the earlier lift type movable piece are designed with bumps to hold the movable piece in the connector housing, but sometimes after the high temperature of reflow welding, the connector will be deformed, causing the movable piece to be too tightly clamped, which requires more effort to open the movable piece. Some connectors are broken because of plastic embrittlement or can't stand too much force.
In the early days, the two ends of the flip type movable piece were designed with bumps to hold the movable piece in the connector housing. However, sometimes after the high temperature of reflow soldering, the connector would be deformed, causing the movable piece to be too tightly clamped, requiring more effort to open the movable piece. Some connectors were broken due to plastic embrittlement or too much force.
▼ Some connectors are designed to use small triangles on the movable piece to clamp the movable piece on the body.
Some connectors are designed to use small triangles on the movable piece to clamp the movable piece on the body.
Postscript:
The connectors sent by many manufacturers have been inspected under the microscope. It is found that if the connector itself has too many burrs, the quality of the connector itself is usually unstable, which is not absolute, but it is not uncommon. Most of the connectors are extremely thin. If the injection process and mold are not carefully maintained, it is easy to have problems, It also means that the manufacturer of connectors does not attach great importance to their quality, which is relatively easy to cause problems. I personally will inspect and test such connectors with special care.
▼ There are many burrs on this connector in some places, which will not affect the function, but I found that several connectors have broken movable pieces, which should be caused by the damage when the movable pieces are squeezed into the body.
There are many burrs on this connector in some places, which will not affect the function, but I found that several connectors have the problem of broken movable pieces, which should be the damage caused by squeezing the movable pieces into the body.
▼ The burr of this connector is long near the contact end point, which may cause poor contact between the contact terminal and the soft plate when installing the soft plate.
然后
联系
电话热线
13410863085Q Q
微信
- 邮箱