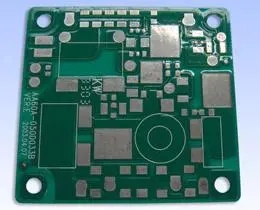
Solution to prevent the first part from falling during secondary back welding
Circuit board manufacturer: the solution to prevent the first part from falling down during secondary back welding
With the rapid development of mobile phone technology, EMS (electronic assembly plants) in mainland China have been suffering from serious shortage of workers from time to time. In addition, EMS plants are increasingly demanding for more automation. Therefore, many parts that may not have passed the SMT process are also required to conform to the PIH (Paste In Hole) process, such as USB connector of Type A, connector of Ethernet, power socket Transformer... and other relatively bulky parts. Previously, most of these parts were manually welded after the SMT process.
Because of the shortage of labor, and in order to save the cost of the subsequent process, on the other hand, considering the quality, many system manufacturers and EMS vendors have begun to require those parts that cannot be changed to the SMD process to at least meet the PIH process requirements, so that all electronIC parts on the circuit board can complete all the welding processes of the circuit board as long as they complete the SMT process.
However, there are requirements for changing parts to SMD or PIH process. Please refer to this artICle first to change SMD parts to Paste In Hole process. What are the differences and impacts? To understand their material requirements.
In addition, changing all electronic parts into SMT manufacturing process will encounter a new problem, that is, when the second side of the circuit board passes back to the soldering furnace, the parts that have eaten tin on the first side will fall off if there are heavy parts. In fact, most companies will define in their manufacturing design specifications (DFx) that heavy parts must be designed on the same side of the circuit board, but with the evolution of technology, As well as the requirements mentioned above, RD seems increasingly unable to comply with this rule.
Is there any way to avoid heavy parts falling from the first side when the second side passes through the furnace?
At present, WorkBear knows several methods. It is believed that most SMT engineers have already implemented them. This is just for reference to some friends who have not met yet:
Method 1: Apply red glue under or beside the parts
In fact, the glue dispenser is a necessary equipment for early SMT processing lines, because the glued SMD parts can be taken to wave soldering, but now most SMT lines almost have no such equipment. If there is no dispenser, manual dispensing must be used. I don't recommend manual dispensing, because manual operation costs labor and labor hours, and the quality is also difficult to control, because if you are not careful, you will encounter other parts that have been mounted well. If there is a machine dispenser, the quality will be better controlLED.
The purpose of red glue is to stick the parts to the circuit board, so the red glue must be on the circuit board, and stick the parts, and then go to the reflow furnace to solidify the yellow glue using the high temperature of the reflow furnace. This red glue belongs to irreversible glue and cannot be softened by heating.
If the red glue point is below the part, the glue dispensing operation must be done immediately after the solder paste is printed on the circuit board, and then the heavier part must be covered on it. It should be noted that there is a risk that the red glue dot will prop up the part under the part, so it is generally a relatively heavy and large part.
The other dispensing operation will be performed on the side of the part. This operation can only be performed after the solder paste is printed and the part is placed in a fixed position. If you are not careful, the part may be damaged, so it is generally used for PIH parts.
If the machine is used to dispense glue on the side, the glue amount and dispensing position must be accurately controlled, the glue must be dabbed on the edge of the part, and then the suction nozzle of the placement machine is used to gently press the part to the fixed depth to ensure that the part does not have the risk of floating.
Method II. Use the furnace carrier
The furnace passing carrier can be designed to have ribs just supporting the position of heavier parts, so that heavier parts are not easy to fall off during the second reflow welding. However, the cost of furnace passing vehicles is not cheap, and the total number of vehicles arranged should be greater than the length of the reflow oven, that is, it is necessary to calculate how many plates walk in the reflow oven at the same time, plus buffer and spare parts. There are 20 or 30 vehicles in total, which may be more expensive.
In addition, the furnace carrier is generally made of metal or special high temperature resistant plastic because it needs to withstand the high temperature of repeated reflow soldering. There is also a special rEMInder that the use of the Carrier will require an additional labor cost. Putting boards on the Carrier will require labor, and recycling of vehicles will also require labor.
Secondly, the use of the carrier may lead to the risk of worse tin melting condition. Because this carrier is usually made of metal, which is easy to absorb heat due to its large area, which will lead to the risk of difficult temperature rise. Therefore, when adjusting the furnace temperature, it must be measured together with the furnace carrier, and the carrier should try to steal the meat that is not used, as long as the principle is to ensure that the carrier is sufficient to support without deformation.
Method 3: Adjust the temperature difference between upper and lower furnaces of the reflow furnace
The reflow furnace can usually control the upper and lower furnace temperatures. Early electronic parts were still in the 1206 age. When adjusting the reflow furnace, we usually reduce the lower furnace temperature by 5~10 ° C compared with the upper furnace temperature. The purpose is to hope that when the second side is reflowed, the parts already welded on the first side will not fall off because of the re melting of tin. But now most SMT engineers do not adjust the furnace temperature like this because the parts are very SMAll, There is no risk of falling.
With the above requirements, it is certain that the large parts on the first side will fall when they pass through the second side for back welding. However, if the connector is such a large and heavy part, even if the temperature difference between the upper and lower furnaces is adjusted, the part will still not fall.
Therefore, adjusting the upper and lower temperature difference of the reflow furnace is only useful for small parts, that is, it is effective when some parts will fall and some parts will not fall. If all parts fall, this method is invalid.
Method 4: Rewelding after returning to use (machine welding, manual welding)
Calculate the cost of re welding and the cost of parts falling, and compare it with the cost. SometiMES, when the time is not ripe, it is not possible to save costs by SIMply pursuing automation. More comparison is needed to determine whether the calculation is cost-effective.
In addition to manual welding, robot welding can also be considered for post re welding. After all, the quality of manual welding is questionable.
然后
联系
电话热线
13410863085Q Q
微信
- 邮箱