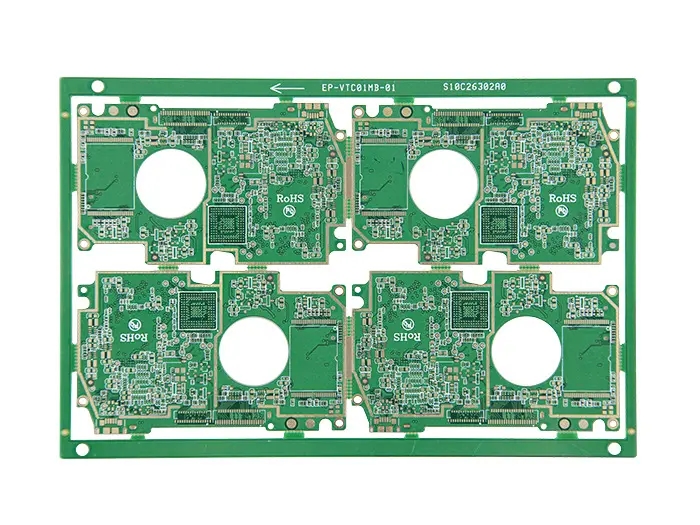
Tell you why PCB uses resin plug hole, what's the reason?
In recent years, the process flow of resin plug hole has been more and more widely used in PCB industry, especially in some products with high layers and large board thICkness. People hope to use resin plug holes to solve a series of problems that can not be solved by using green oil plug holes or pressing and filling resin. However, because of the characteristics of the resin used in this process, many difficulties need to be overcome in the production to achieve good quality of resin plug hole products.
1. Origin of resin plug hole:
1.1 Development of electronIC chips
With the continuous updating of electronic product technology, the structure and installation mode of electronic chips are also constantly improving and changing. Its development is basically from parts with plug-in pins to highly dense integrated circuit modules with spherical matrix solder joints. The development history of components can be seen from the following figure:
1.2 The meeting of two people makes the resin plug hole technology come true
In the PCB industry, many process methods have been widely used in the industry, and people have little concern about the origin of some process methods. In fact, as early as the time when the electronic chip with spherical matrix array just CAMe into the MARKet, people have been giving advice for this SMAll chip mounted component, hoping to reduce the size of its finished product from the structure.
In the 1990s, a Japanese company developed a resin that plugs the hole directly and then plated copper on the surface, mainly to solve the problem of air blowing in the air that is easy to occur in the green oil plug hole. Intel applied this process to Intel's electronic products, and the so-calLED POFV (also called Via on pad in some factories) process was born.
2. Application of resin plug hole:
At present, the process of resin plug hole is mainly used in the following products:
2.1 Resin plug hole of POFV technology.
2.1.1 Technical principle
A. Plug the through hole with resin, and then copper plate the hole surface.
2.1.2 Advantages of POFV technology
l. Reduce the space between holes, reduce the area of the plate,
l. Solve the problem of wire and wiring, and improve the wiring density.
2.2 Inner HDI resin plug hole
2.2.1 Technical principle
Plug the embedded hole of the inner HDI with resin, and then press it. This process balances the contradiction between the thickness control of the pressed medium layer and the design of HDI buried hole filling.
l. If the HDI embedded hole in the inner layer is not filled with resin, the plate will be directly scrapped due to the problem of plate bursting during overheating impact;
l. If the resin plug hole is not used, multiple sheets of PP are required to be pressed to meet the needs of glue filling. However, the thickness of the medium layer between layers will be thicker due to the increase of PP sheets.
2.2.3 Application of inner HDI resin plug hole
l. The inner HDI resin plug hole is widely used in HDI products to meet the design requirements of HDI products' thin dielectric layer requirements;
l. For the blind buried hole products with embedded hole design in the inner layer HDI, because the medium design in the middle is too thin, it is often necessary to add the process of inner layer HDI resin plug hole.
For some blind hole products, because the thickness of the blind hole layer is greater than 0.5mm, the blind hole cannot be filled by pressing and filling glue. The blind hole also needs to be filled by resin plug to avoid the problem of copper free blind hole in the subsequent process.
2.3 Through hole resin plug hole
In some 3G products, because the thickness of the board is more than 3.2mm, in order to improve the reliability of the product, or to improve the reliability of the green oil plug hole, under the permission of the cost, people also use resin to plug the through hole. This is a major product category that has been popularized in recent years.
3. Process manufacturing method of resin plug hole:
The three types of resin plug holes described above have different processes, as follows:
3.1.1 POFV type products (different equipment in different factories follow different processes)
1. Cutting à drilling → PTH/electroplating → plug hole → baking → grinding → PTH/electroplating → outer line → anti welding → surface treatment à forming à electrical measurement à FQC à delivery
2. Cutting à drilling à copper sinking à plate electricity (thickened copper) à resin plug hole à polishing à drilling through hole à copper sinking à plate electricity à outer layer graphics à graphic electroplating à etching à resistance welding à surface treatment à molding à electrical measurement à FQC à shipment
3.1.2 Inner layer HDI resin plug type products (two processes: grinding and non grinding)
Grinding process:
1. Cutting and burying hole inner layer figure à AOI à pressing à drilling → PTH/electroplating → plugging → baking → grinding → inner layer line → browning → pressing → drilling (laser drilling/mechanical drilling) → PTH/electroplating → outer layer line à welding prevention à surface treatment à forming à electrical measurement à FQC à shipping
2. Cutting à embedding hole inner layer figure à AOI à pressing à drilling à copper sinking à plate electricity (thickened copper) à resin plug hole à polishing à inner layer figure à AOI à pressing à drilling through hole à copper sinking à plate electricity à outer layer figure electroplating à etching à resistance welding à surface treatment à forming à electrical measurement à FQC à shipping
No grinding required: cutting material à burying hole inner layer figure à AOI à pressing à drilling → PTH/electroplating → inner layer line → browning → plugging hole → flattening → baking → pressing → drilling (laser drilling/mechanical drilling) → PTH/electroplating → outer layer line → à welding resistance à surface treatment à forming à electrical measurement à FQC à delivery
3.1.3 Type of outer through-hole resin plug
1. Cutting à drilling → PTH/electroplating → plug hole → baking → grinding → baking → outer line → anti welding → surface treatment à forming à electrical measurement à FQC à delivery
2. Cutting à drilling à copper sinking à plate electricity à plate electricity (thickened copper) à resin plug hole à baking → grinding → baking à outer layer graphics à graphic electroplating à etching à solder resistance à surface treatment à forming à electrical measurement à FQC à shipment
3.2 Special points in the process
l. From the above processes, we can clearly see that the processes are different. Generally, we understand that "resin plug hole" is followed by the product of "drilling through hole and copper plate electricity" process, and we all think it is a POFV product; If the process following the "resin plug hole" is "inner layer graphics", we consider it as the inner layer HDI resin plug hole product; If the process following the "resin plug hole" is "outer layer figure";
l. The above different types of products are strictly defined in the process, and can not go wrong; Keding ChEMIcal has developed three different inks based on the characteristics of the above three processes. The three inks TP-2900S TP-2900 TP-2900C correspond to the above three processes.
3.3 Process improvement
A. For products with resin plug holes, in order to improve the product quality, people are constantly adjusting the process to SIMplify their production process and improve the yield of their production;
B. Especially for the products with HDI plug holes in the inner layer, in order to reduce the scrap rate of the open circuit of the inner line after polishing, the process of plugging holes after lines is adopted. First, the inner line is made. After resin plug holes, the resin is pre cured, and then the resin is cured using the high temperature in the pressing stage.
C. At the beginning, UV pre curing+thermosetting ink was used for the inner layer HDI plug hole. At present, thermosetting resin is directly used, which effectively improves the thermal performance of the inner layer HDI plug hole.
3.4 Process method of resin plug hole
3.4.1 Ink used for resin plug hole
A. At present, there are many kinds of ink used in the resin plug hole process on the market. Commonly used brands include San Ei, Kotti and other suppliers.
3.4.2 Process conditions of resin plug hole
A. There are tens of thousands of resin plug holes, and it should be ensured that no hole is not full. This one in ten thousand defect will lead to the probability of scrapping, which inevitably requires rigorous thinking and specification in the process.
B. Good plug hole equipment is an inevitable requirement. At present, the screen printing machines used for resin hole plugging can be divided into two categories, namely, vacuum hole plugging machines and non vacuum hole plugging machines.
3.4.3 Plugging process of ordinary screen printing machine
A. The selection of screen printing machine is based on the maximum cylinder pressure, screen lifting mode, stability and levelness of the tool holder, etc;
B. The silk screen scraper needs to use a scraper with a thickness of 2cm and a hardness of 70-80 degrees. Of course, it must be resistant to strong acids and alkalis;
C. Screen printing can choose either screen or aluminum sheet; What is to be controlled is to select the appropriate mesh number and the window size for the hole diameter according to the requirements of the plug hole process conditions;
D. The backing plates used for resin plug holes are various, but they are often ignored by engineers. The base plate not only plays the role of air conduction, but also plays the role of support. For the area with dense holes, after drilling the base plate, the whole area is empty. At this position, the base plate is arched or deformed, and the support force for the plate is the worst, which will result in poor plumpness of the plug hole at this position. So when making the base plate, we should find a way to overcome the problem of large area vacancy. At present, the best way is to use a 2mm thick base plate, and only drill 2/3 of the depth of the base plate.
E. In the process of printing, the most important thing is to control the pressure and speed of printing. Generally speaking, the larger the aspect ratio is, the smaller the aperture is, the slower the speed is required, and the greater the pressure is required. Controlling the slow speed is the best way to improve the plug hole bubble.
3.4.4 Plugging process of vacuum resin plugging machine
Due to the high price of the vacuum resin plugging machine and the confidentiality of its equipment use and maintenance technology, few PCB manufacturers can use this technology at present.
The hole plugging technology of VCP vacuum resin hole plugging machine is mainly that it has an ink clip and two laterally movable plug control heads. There are many small holes in the plug hole head. After the equipment is vacuumized, use the piston to push the ink in the ink clip to the small hole in the plug hole head. Two transverse plug hole heads clamp the plate first, and then fill the ink into the through hole or blind hole on the plate through many small holes in the plug hole head. The plate is vertically hung in the vacuum chamber, and the transversely moving plug hole head can move downward until the hole in the plate is filled with resin. The pressure of the plug hole head and the ink can be adjusted to meet the requirements of the fullness of the plug hole. Different sizes of plug hole heads can be used to plug holes for different board sizes. After the plug hole is completed, it can be scraped off with the scraper slurry plug hole ink and then added into the plug hole ink clip for reuse.
At present, there is another type of vacuum plug hole machine that uses the screen for printing and CCD alignment system for alignment. Its operation is similar to that of ordinary screen printing, but it has an additional process of vacuum plug hole. This kind of plug hole machine has the best plug hole effect, but because of expensive equipment investment, it has not been widely used.
The use of vacuum hole stopper is undoubtedly the best way to solve the bubble problem of resin, and the selection of hole stopper ink is basically not limited by the process. However, because there is resin on the whole board, it is very difficult to remove the resin. It needs to be used together with a good grinder.
3.4.5 Grinding after resin plug hole
A. Nonwovens or abrasive belt grinders are essential equipment for making resin plug holes. On the one hand, the equipment is required to effectively remove the resin from the board surface, and on the other hand, the roughness of the copper surface is required to be free of scratches, scratches and other problems.
conclusion
After years of development, the resin plug hole technology has been gradually accepted by many users, and continues to play an indispensable role in some high-end products. Especially, it has been widely used in blind hole, HDI, thick copper and other products, which involve communication, military, aviation, power supply, network and other industries. As the manufacturer of PCB products, we have learned the process characteristics and application methods of resin plug hole process. We also need to constantly improve the process capability of resin plug hole products, improve the quality of products, solve the relevant process problems of such products, really use and promote such technology, and achieve the production of PCB products with higher technical difficulties.
然后
联系
电话热线
13410863085Q Q
微信
- 邮箱