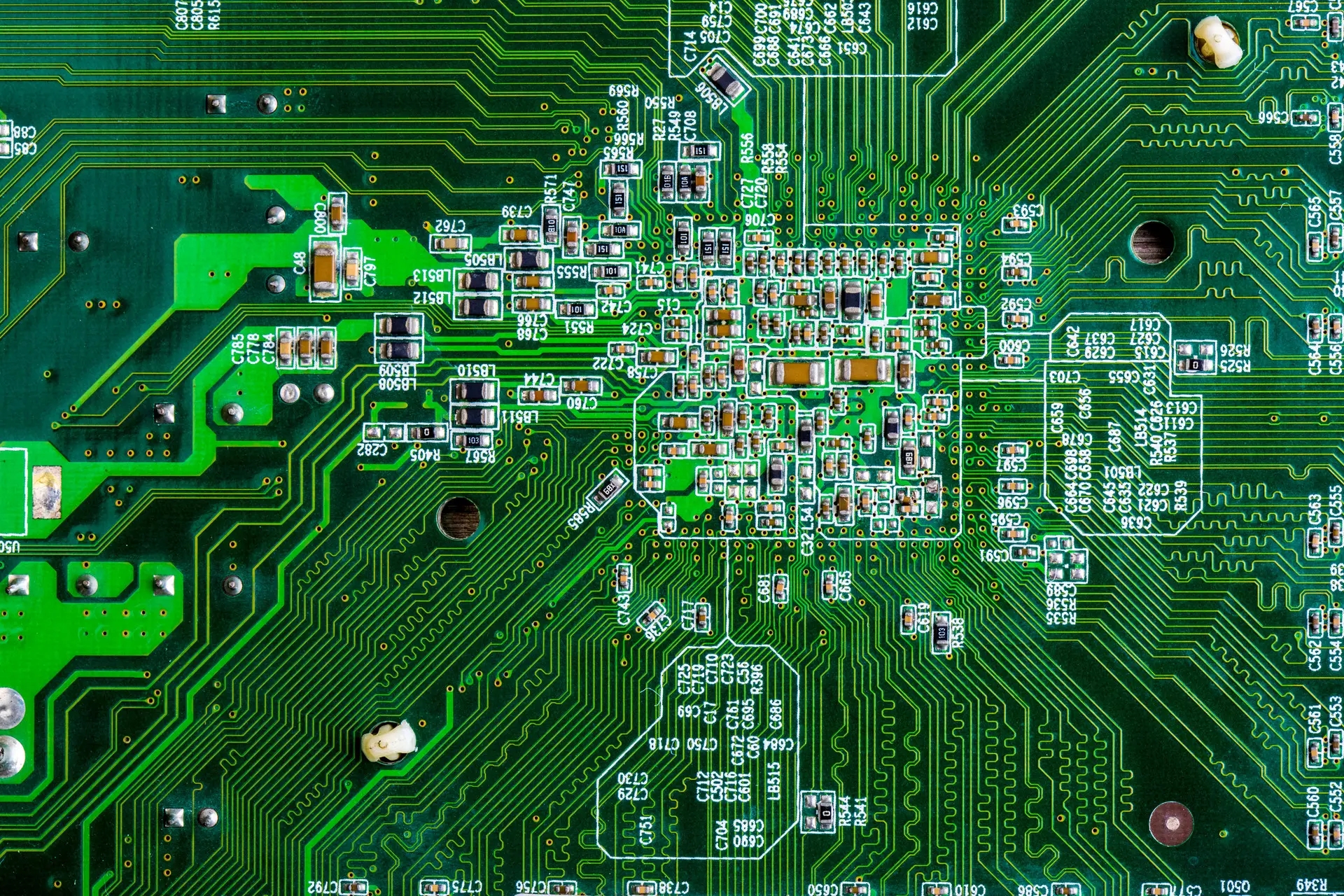
PCB工艺 PCB PCB检测方法及其介绍
本文介绍了过程监控可以防止 PCB 缺陷并提高整体质量。
检查通常可以提醒您装配过程中是否存在太多变数。 即使在您的制造过程可以实现连续零缺陷生产之后,仍需要某种形式的检查或监控以确保所需的质量水平。 表面贴装组装是一系列非常复杂的事件,其中包含大量单独的操作。 我们的诀窍是在没有 100% 检查的情况下建立平衡的检查和监控策略。 本文将讨论检查方法、技术和手动检查工具,以及回顾自动检查工具并使用检查结果(缺陷数量和类型)来改进过程和产品质量。
检查是以产品为中心的活动,而监控是以过程为中心的活动。 两者都是质量计划所必需的,但长期目标应该是减少产品检查和增加过程监控。 产品检验是被动的(缺陷已经出现),而过程监控是主动的(缺陷是可以预防的)——显然,预防比被动应对存在的缺陷更有价值。
检查实际上是一个筛选过程,因为它试图找到不可接受的产品进行修复。 很明显,大量的检验并不一定能提高或保证产品质量。 德明十四点之三说,%26ldquo; 不要指望 %26rdquo; 的大规模检查。 戴明强调,一个强大的过程应该着重于建立稳定、可重复和统计监控的过程目标,而不是大量检查。 检查是一项主观活动,即使经过相当的训练,也是一项艰巨的任务。 在许多情况下,您可以请一组检查员评估焊缝,但会得到几个不同的意见。
操作员疲劳是 100% 检查通常无法发现每个制造缺陷的原因。 此外,这是一项高成本且无附加值的操作。 它很少能达到更高的产品质量和客户满意度的预期目标。
几年前,我们开始使用 %26ldquo; 进程监控%26rdquo; 使用这个词,而不是检查员,是因为我们要改变生产场所的意识形态,从被动反应转变为主动预防。 检查员通常坐在装配线的末端检查产品。 在理想情况下,过程监控活动是产品检验和过程监控之间的平衡——例如,确认正在使用正确的过程参数、测量机器性能以及建立和分析控制图。 过程监控在这些活动中起主导作用; 它们帮助机器操作员完成这些任务。 培训是一个关键因素。 流程监控员和机器操作员必须了解流程标准(例如 IPC-A-610)、流程监控概念和相关工具(例如控制图、帕累托图等)。 电路板制造商的过程监控器还可以提高产品质量和过程监控。 作为制造团队的重要成员,监督员鼓励采用缺陷预防方法,而不是搜索和修复方法。
过度检查也是一个常见问题。 很多时候,过检只是因为对IPC-A-610工艺标准的理解有误。 比如对于元器件的插装,很多检测人员也希望板材两侧完美焊接圆脚,通孔完全填满。 然而,这不是 IPC-A-610 所要求的。 检验质量随着检验人员注意力的紧张程度和集中度而波动。 例如,恐惧(管理压力)可能会提高生产现场的集中度,质量可能会随着时间的推移而提高。 但是,如果以批量检验为主的检验方式,仍有可能生产出不良品,并可能出厂。
我们应该避免的另一个术语是修饰。 在这个行业中,许多员工认为补焊是装配过程中正常且可接受的部分。 这是非常不幸的,因为任何形式的返工和修理都应该被视为不可取的。 返工通常被认为是不可取的,但它是整个制造组织灌输的必要信息。 重要的是建立一个将缺陷和返工视为可以避免和最不希望发生的制造环境。
对于大多数公司来说,人工检查是第一道防线。 检查员使用各种放大工具更仔细地查看组件和焊缝。 IPC-A-610 建立了一些基于检测元件焊盘宽度的基本放大准则。 制定这些指南的主要原因是为了避免因过度放大而导致过度检查。 例如,如果焊盘宽度为 0.25~0.50 mm,则所需的放大倍数为 10X。 如有必要,20X 也可以作为参考。
每个检查员都有自己喜欢的检查工具; 最好有一个机械师使用的三镜头折叠袖珍放大镜。 最大可携带12X放大倍率,刚好适合近距离焊点。 也许最常见的检查工具是放大倍数为 10-40X 的显微镜。 然而,连续使用显微镜造成的疲劳通常会导致过度检查,因为放大倍数通常会超过 IPC-A-610 的指南。 当然,当您需要仔细检查可能存在的缺陷时,它很有用。
对于一般检查,首选配备变焦镜头 (4-30X) 和高清彩色监视器的视频系统。 这些系统易于使用,更重要的是,它们比显微镜更不易疲劳。 高质量的视频系统成本不到 2000 美元,好的显微镜成本不到 2000 美元。 视频系统的另一个好处是不止一个人可以看到物体,这在培训或检查员需要第二意见时很有帮助。 Edmund ScientifIC (edmundscientific.com) 拥有大量放大工具,从手持放大镜到显微镜再到视频系统。
综上所述,在 0-100% 检查之间建立平衡的监控策略是一个挑战。 从这一点开始,关键检查点,我们将讨论检查设备
自动化:在许多情况下,它比检查员更准确、更快速、更高效。 但它可能非常昂贵,具体取决于其复杂性。 自动检测设备可能会削弱人们的意识,给人一种安全的错觉。
焊膏检查
锡膏印刷是一个复杂的过程,很容易偏离预期的结果。 需要明确定义和正确实施的过程监控策略来使过程处于受控状态。 至少应手动检查覆盖面积和厚度测量,但最好使用自动覆盖、厚度和体积测量。 使用极差控制图(X-bar R 图)记录结果。
锡膏检测设备有简单的 3 倍放大镜到昂贵的自动在线机器。 主要工具使用光学或激光来测量厚度,而辅助工具使用激光来测量覆盖率、厚度和体积。 这两种工具都是离线使用的。 第三级工具也测量覆盖面积、厚度和体积,但在线安装。 这些系统的速度、准确性和可重复性因价格而异。 工具越贵,性能越好。
对于大多数装配线,特别是高度混合的生产,中等性能是首选。 它是一种离线工具,用于安装台面以测量覆盖范围、厚度和体积。 这些工具非常灵活,成本不到 50000 美元,而且通常可以提供所需数量的反馈。 显然,自动化工具要贵得多($75,000 - $200,000)。 但是,它们更快、更方便,因为它们是在线安装的。 最适用于批量大、混料少的流水线。
检查胶水
胶水分配是另一个很容易偏离预期结果的复杂过程。 与焊膏印刷一样,需要明确定义和正确实施的过程监控策略来控制过程。 建议手动检查胶点直径。 使用极差控制图(X-bar R 图)记录结果。
在滴胶循环之前和之后,最好在板上滴至少两个孤立的胶点来表示每个点的直径。 这允许操作员在胶水循环期间比较胶点质量。 这些点也可用于测量胶点的直径。 胶点检测工具价格相对便宜,基本有便携式或台式测量显微镜。 不知道有没有专门针对胶点检测设计的自动化设备。 可以调整一些自动光学检测 (AOI) 机器来完成这项任务,但它们可能过于合格。
公司通常会对下线的第一块板进行详细检查,以验证机器的设置。 这种方法缓慢、被动且不准确。 一个复杂的电路板通常包含至少 1000 个元件,其中许多元件没有标记(值、零件号等)。 这给检查带来了困难。 这是验证机器设置(元件、机器参数等)的积极方法。 AOI可有效用于首板的检测。 一些硬件和软件供应商还提供飞达设置确认软件。
协调机器设置的验证是过程监控员的理想角色,他带领机器操作员在检查表的帮助下通过生产线确认过程。 除了验证进料器的设置外,过程监控器还应使用现有工具仔细检查前两个板。 回流焊后,制程监控员应对关键元器件(密集元器件、BGA、极性电容等)进行快速而详细的检查。 与此同时,生产线继续组装板材。 为减少停机时间,生产线应在回流前填充板,而过程监控器在回流后检查前两块板。 这可能很危险,但您可以通过验证机器设置来获得这样做的信心。
X射线检查。 根据经验,X 射线对于 BGA 组装不是强制性的。 但是,如果您负担得起,它肯定是手头上的好工具。 应该推荐用于 CSP 组件。 X射线对检查焊接短路非常好,但对发现焊接断路效果较差。 低成本的X光机只能往下看,焊接短路的检查就足够了。 可以倾斜被检物的X光机更适合开路检查。
自动光学检测 (AOI)。 十年前,光学检测作为解决大家质量问题的工具。 后来这项技术因为跟不上装配技术的步伐而停止了。 在过去的五年里,它作为一项令人向往的技术重新出现。 一个好的过程监控策略应该包括一些重叠的工具,例如在线测试(ICT)、光学检查、功能测试和视觉检查。 这些过程相互重叠和互补,无法单独提供足够的覆盖面。
二维 (2-D) AOI 机器可以检查是否存在缺失元件、未对准错误、不正确的零件编号和反极性。 此外,三维 (3-D) 机器可以评估焊接点的质量。 一些供应商以低于 50000 美元的价格提供台式二维 AOI 机器。 这些机器非常适合初始产品检验和小批量样品计划。 在更高性能类别中,2-D 独立或在线机器成本为 75000-125000 美元,而 3-D 机器成本为 15000-250000 美元。 AOI 技术前景广阔,但处理速度和编程时间仍然是一个限制因素。
数据收集是一回事,但使用这些数据来提高性能和减少缺陷才是最终目标。 不幸的是,许多公司收集了大量数据而没有有效地使用它们。 审查和分析数据可能很费力。 经常看到这项工作仅由工程pcb设计人员进行,不包括生产活动。 没有准确的反馈,生产就盲目进行。 每周质量会议可能是工程设计和生产部门沟通关键信息并促进必要改进的有效方法。 这些会议要求领导者组织良好,尤其是在短时间内(30 分钟或更短)。 这些会议上提供的数据必须易于使用且有意义(例如帕累托图)。 确认问题后,必须立即指派调查员。 为确保会议圆满结束,会议领导必须做好准确记录。 结束意味着根本原因和纠正措施。
然后
联系
电话热线
13410863085Q Q
微信
- 邮箱