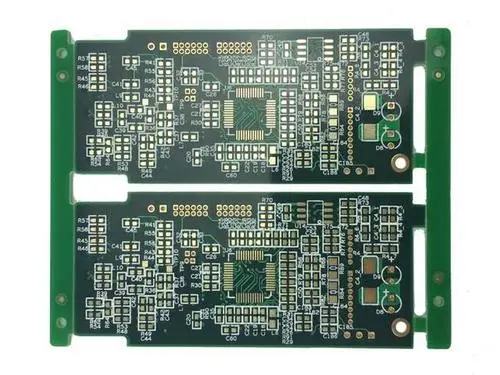
通过我们的 PCB 技术热线经常被问到的一个问题是,“IPC 清洁度标准是什么?”。 这是PCB行业新手经常问到的一个简单明了的问题,所以简单明了的答案一般都是他们想要的。 然而,在大多数情况下,这不足以满足他们的个人需求。
要回答这个问题,首先要了解简单的标准:所用的IPC标准、残留物的种类、适用范围和清洁度标准。
标准残留物类型 适用范围 洁净度标准
IPC-6012 各种离子<1.56 μ G/cm2 NaCl当量阻焊膜涂层前光板
IPC-6012 OrganIC * 各类电子产品阻焊涂层前光面无污染物排放
J-STD-001 各类电子产品阻焊层涂前光板足以保证可焊性
J-STD-001 所有电子类粒子焊后无松动、无挥发、电间隔最小
J-STD-001 松香焊后组装 * 1 类电子产品<200 μ g/cm2
2 类电子产品的焊后组装 <100 μ g/cm2
3 类电子产品的焊后组装 <40 μ g/cm2
J-STD-001 离子 * 所有电子类别的焊后组装 <1.56 μ G/cm2 NaCl 当量
IPC-A-160 焊后组件对所有电子类可见残留物的视觉可接受性
但这些答案是否提供了必要的事实? 不幸的是,打电话的人很少满意。 事实上,这些答案往往会引出更多的问题,例如:“是吗?”; “如果污染物含有更多的氯化物怎么办?”; “免清洗过程中的助焊剂残留物怎么办?”; “如果使用保形涂层来保护组件怎么办?”; 或者,“其他非离子污染物呢?”
与过去松香助焊剂主导PCB行业的“好时光”不同,新的PCB表面涂层、助焊剂、焊接和清洁系统层出不穷。 显然,没有“一刀切”的答案。 出于这个原因,标准和规范强调用于证明可靠性的测试程序,而不是简单的通过/失败数字。
仔细看一下IPC标准——尤其是IPC-6012,刚性PCB印制板的技术指标和性能——就会发现,在阻焊层、焊料或替代表面涂层后的光滑板的清洁度要求应该在 文档。 这意味着 PCB 组装制造商必须告诉电路板制造商他们希望灯板的清洁度。 它还为使用免洗工艺的 PCB 组装制造商留出空间,为进货电路板设定更严格的清洁度要求。
PCB组装厂商不仅需要规定来料板的清洁度,还需要与用户就组装产品的清洁度达成一致。 根据J-STD-001,除非用户另有规定,否则制造商应规定清洁要求(或不清洁或清洁一个或两个装配表面)和清洁度测试(或不测试,表面绝缘电阻测试,或测试离子 、松香或其他有机表面污染物)。 然后根据PCB焊接工艺和PCB产品的兼容性来选择清洗系统。 清洁度测试将取决于所使用的助焊剂和清洁化学品。 如果使用松香助焊剂,J-STD-001 提供了 1、2 和 3 类产品的数字标准。 否则,离子污染测试是最简单且成本最低的。 J-STD-001也有通用数字
如果氯化物含量是一个问题,涉及离子色谱分析的工业研究结果表明,以下指南是氯化物含量的合理断点。 当氯化物含量超过以下水平时,电解失效的风险会增加:
小于 0.39 低固体通量 μ g/cm2
对于高固体松香助焊剂,小于 0.70 μ g/cm2
水溶性助焊剂小于0.75 - 0.78 μ g/cm2
锡铅金属化光面板小于0.31μg/cm2
关于清洁的讨论往往会得出最终的答案,即真正的清洁度取决于PCB产品和期望的最终使用环境。 但是,您如何确定对于特定的最终使用环境来说什么样的清洁就足够了呢? 通过深入、严格的分析,研究每一种潜在污染物和最终使用情况,并进行长期的可靠性测试。
但是有没有更简单的方法呢? 通过介绍别人的经验,缩短增加学习的弯路。 如IPC、EMPF和海军航空电子中心对各种清洁条件进行了一系列测试和工业研究; 其中一些调查结果可在公共领域获得。 这些技术文件和手册指导个人或公司了解过程测试和有效性的这一微妙而关键的要素。 一个很好的例子是由 IPC、环境保护署 (EPA) 和国防部 (DOD) 赞助的深度清洁和清洁度测试计划,该计划于 1980 年代后期完成。 该计划研究电子制造清洁过程中使用的新材料和新工艺,以降低氯氟烃 (CFC) 的含量。
PCB电子行业的下一个大浪潮——无铅焊料和无卤素绝缘层的运动——可能会引发另一场关于洁净度和清洁度的广泛工业研究。 到那时,读者和电话顾问需要在掌握IPC规范的基础上,从各种销售资料、案例研究、报告和指南中清楚地了解个人的清洁度要求是什么。
然后
联系
电话热线
13410863085Q Q
微信
- 邮箱