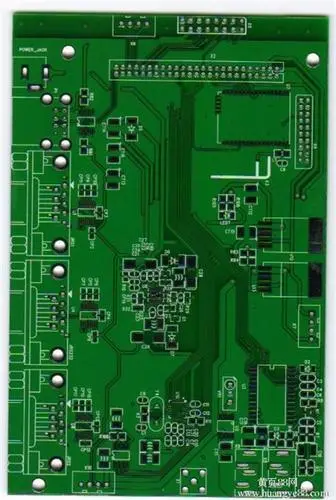
一、高端PCB钻铣床控制系统架构
1.1 系统结构说明
PCB控制系统PCB控制采用上位机+下位机+网络I/O接口模块的结构。 由于是通过千兆以太网与下位机进行数据通讯,因此对上位机没有特殊要求。 可根据工况选择工控机、普通PC甚至笔记本电脑。 下位机实现实时运动控制、I/O管理和故障监控。 专用运动控制器通过轴接口连接驱动器,输出模拟信号,采集编码器/光栅尺反馈信号,实现闭环伺服控制、限位管理、原点、驱动报警、复位、刹车报警等信号。 这部分关系到最终的速度精度等关键指标。 可选择国内固高公司的独立控制器或美国DELTA TAU著名的PMAC运动控制卡。 现场网络I/O扩展模块实现断刀检测、刀具检测和辅助输入输出功能。
1.2 软件功能模块
数控程序也相应地分为上下两部分。 上位程序实现参数设置、文件输入与转换、图形图像处理、现场监控等人机交互功能。 加工文件解释完成,形成加工指令和刀具指令数据后,打开主加工线程,将数据发送给下层程序。 下层运动控制主程序完成井道控制和I/O管理等实时性要求高的功能; 检测线程运行在CPU空闲期,对系统状态进行监测和诊断,并在操作界面上即时显示系统状态。
以上两部分的内容主要描述了系统搭建的常规软硬件技术路线,远远不够。 要想真正打造和开发出高档次的控制系统,并希望能与国外顶级控制器相抗衡,还需要在控制和客户端人机界面上下功夫。
二、控制关键技术
目前国产系统最终的整体效果不如进口系统,这在很大程度上是由以下因素造成的。 要克服这些缺点,就需要选择功能强大的运动控制卡。 DELTA TAU的PMAC卡无疑是最好的选择之一。 它提供的关键功能恰好满足构建高端PCB系统的需要。
2.1 控制方式的选择
国内传统设备厂商在低端设备上均采用位置控制方式。 这是一种利用PCB板卡通道发送脉冲,精确控制工作在位置模式下的步进电机或伺服电机的一种方式。 它的响应速度和闭环特性都很差,甚至不是真正的闭环,以至于无法发挥机械系统的潜力。 后来随着速度控制方式的逐渐普及,电机控制的动态特性有了很大的改善,也实现了真正的闭环控制。 机床的速度和精度都达到了较高的水平。 这两种电机控制方式是目前国内设备厂商的主流选择。
电机的力矩和直接PWM控制被欧美厂商广泛采用,国内应用基本空白。 这两种控制方式完全摒弃了位置模式响应低的特点,克服了速度模式在调试PID参数时由于步长长带来的不确定性。 由于转矩和直接PWM控制方式在控制模型上更加简单直接,速度环和电流环转移到控制卡侧,响应性更高,同时控制器的响应速度更快。 反馈环节也得到了一定程度的提升,所以两者的合力会产生更高的性能。 遗憾的是,到目前为止,国产运动控制器还不能支持以上两种先进的控制方式,一定程度上限制了国产系统的发展。
2.2 系统辨识技术
目前,国内PCB制造商对伺服系统与机械系统之间的联系认识不足,因此即使选择了优良的元器件来构建机械系统,仍然无法获得理想的控制效果。 即由于对系统辨识的认识非常模糊,无法最有效地协调控制器与被控对象之间的关系。 如果要开发高端控制器,应尽可能提高伺服系统的跟踪速度。 带宽越大,速度越好。 伺服系统的带宽主要受控制对象和执行器惯性的限制。 惯性越大,带宽越窄。 先进的控制器具有自动诊断系统带宽的能力,然后可以选择性地支持低通滤波器或陷波滤波器,以避开机床的固有频率(共振点)。 在一定程度上可以最大限度地挖掘机床的潜力,避免高速运动激发的机床振动对机床造成的损坏。
2.3 干扰抑制与预防
电磁干扰对机床最终加工精度的影响也是致命的。 除了在电路布局、屏蔽、接地等方面采取积极措施抑制干扰外,干扰后的有效预防也很重要。 但是目前大多数控制器都没有这个功能。 高端运动控制器,如PMAC,通过硬件监测编码器或光栅尺反馈的A、B相上升沿相位差是否正常,来判断进入控制器比较环节的信号是否完好。 如发现异常,立即报警,提示操作者立即排除干扰,避免机床跑偏。
2.4 控制器独立运行
过去,大多数运动控制卡都是插在主机的ISA或PCI插槽中。 单一固定金手指的接口形式不适合长期在恶劣的工作环境下工作,尤其是机器剧烈震动时,会出现通讯中断,影响系统的稳定性。 因此,需要控制器的独立操作。 采用网络通信的方法有效地解决了这个问题。 同时避免了控制系统与PC共地的问题,使干扰信号不会跑到电脑上影响主控程序的正常运行,增强了稳定性。
控制器的独立运行也使得实现机床的网络化控制成为可能,无人化工厂的概念不再遥不可及。 一旦网络连接并获得总控制权,网段内的任何计算机都可以控制和监视机器。 同样,一台计算机也可以控制多台机床,具有很大的灵活性。
三、客户端图形控制界面优化
目前部分PCB厂家负责人有一个误区,认为只要能实现功能,其他要求都可以打折扣。 这种思想直接导致了中国至今未能研制出高水平控制系统的局面。 这种整体落后不仅是在PCB钻铣领域,在金属加工机床领域,乃至整个工控领域都是如此。 为了改善这种状况,笔者认为以下几个方面至关重要。
3.1 软件工程思想的应用
目前,PCB行业控制产品在软件工程思想的实施和应用上受限,严重落后于管理、金融、游戏和通信行业。 一方面是因为工控领域的程序员大多是机械或工艺专业的学生,对编程语言和计算机技术的理解比较粗糙,所编写的软件大多停留在比较初级的水平; 另一方面,掌握高级编程技术的工程师往往对硬件和控制的概念模糊,无法用完美的编程语言实现工艺流程和人机交互界面。 解决这一矛盾的根本办法是在产业发展过程中贯彻软件工程思想,借鉴其他领域开发大中型软件系统的模式,组建合理的团队。 规划者是行业专家,实施者是计算机编程专家。 只有这样,才能做出高质量的产品,与国外系统竞争,并保证软件具有良好的可扩展性和可维护性。
3.2 数据库技术的应用
目前,国内数控系统软件在保存数据、机床配置和大量工况信息时,大多采用文本文件或INF文件的格式,数据量大时无法对其内容进行有效的检索和管理。 为了实现更复杂的界面配置,动态添加用户,切换语言,对刀断信息和操作信息进行分类分时管理,单纯的文本访问已经不能满足要求,那么如何使用小型数据库来组织管理 数据成为话题。 作者采用ACCESS数据库,通过DAO350的接口对数据库进行管理和控制,实现对大量数据的动态管理,彻底解决了二进制或ASCII文件数据管理带来的不便。 因此,能否有效利用这些先进的计算机技术,也是判断一个系统优劣的依据之一。
3.3 跨硬件平台架构
目前,我国机床设备生产企业众多,大致分为四川体系和沿海体系。 川系起步早,但技术自主发展,比较落后。 沿海第一系列直接空降、仿制国外技术,与国际比较同步。 但是,无论在哪里,设备制造商都会根据客户群体的不同需求,对PCB产品市场进行细分,有的面向低端市场,有的面向高端市场。 由于对机器速度和精度的要求不同,运动控制元件的选择也不同。 为了满足各厂商的不同需求,需要将控制系统设计成跨主流硬件平台的通用系统。
3.4 美观的界面和复杂智能功能的实现
很多开发者【对PCB行业的美观和布局没有给予足够的重视,但是在大型行业展会上将自研系统界面与SIEB&MEYER的CNC84系统进行对比时,发现根本不是一个档次的 . 另外,国外的系统普遍智能化程度高,比如刀具断裂信息和操作信息的记录管理,8个文件象限和8个机械象限任意组合64例的统筹考虑,刀具直径检测是和光 点位补偿功能,多种机械手对刀方式等。 由于种种原因,国内的系统开发商无法实现如此完备的功能,因此永远无法与国外系统竞争。 究其原因,还是由于规划不完善,缺乏开发大型软件的经验。 界面的美观和各种功能的智能化也是开发者实力的重要体现。
四、结论
通过近20年的不断技术突破和市场培育,我国造就了一批PCB数控制造企业,打开了中低端市场的局面,形成了一定的市场规模; 然而,在技术密集的中高端控制器市场,国产控制器的规模始终没有取得很好的突破,利润空间被挤压,研发体系无法支撑可持续的技术进步。 为了突破这种局面,笔者在金属加工领域避开了FANUC、SIEMENS等国际巨头,选择了PCB钻铣这个稍微偏远的领域,深入调研了控制器在该领域的技术和市场现状 ,并给出了打造高端控制器的技术路线。 之后,我们从核心控制技术、人机界面等方面进行有针对性的技术突破,从软硬件层面进行精心部署,有效开发了一套在各项技术指标乃至外观控制上均达到高标准、不 既做到快速、准确、稳定,又美观、方便,全面赶超国外同类PCB产品。 同时,我们希望能找出一套打破僵局的模式,供同行参考。
然后
联系
电话热线
13410863085Q Q
微信
- 邮箱