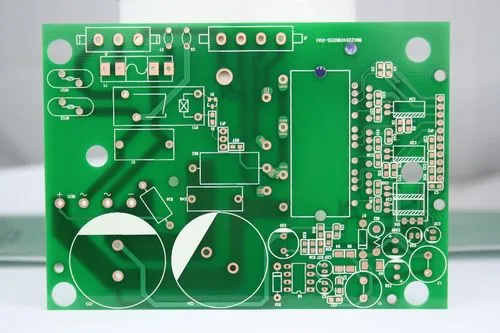
以下是高级PCB封装器件的快速贴装:
面阵封装变得越来越重要,特别是在汽车、电信和计算机应用中,因此生产力成为讨论的焦点。 引脚间距小于 0.4 毫米,即 0.5 毫米。 细间距 QFP 和 TSOP 封装的主要问题是生产率低下。 但是,由于平面阵列封装的脚间距不是很小(例如倒装芯片小于200μm),回流焊后dmp率至少比传统的fine pitch技术好10倍。 此外,与相同间距的QFP和TSOP封装相比,考虑到回流焊时的自动对准,对贴装精度的要求要低很多。
另一个优点,尤其是倒装芯片使印刷电路板的占用面积大大减少。 表面阵列封装还可以提供更好的电路性能。
因此,PCB行业也在向平面阵列封装方向发展,最小间距为0.5mmμ的BGA和芯片级封装(CSP)不断引起人们的关注。 至少有20家跨国公司在致力于这一系列封装结构的研究。 未来几年,预计裸芯片的消费量将以每年20%的速度增长,其中倒装芯片增长最快,其次是应用于COB(直接板上贴装)的裸芯片。
预计倒装芯片的消费量将从1996年的5亿颗增加到本世纪末的25亿颗,而TAB/TCP的消费量将停滞不前,甚至出现负增长。 不出所料,1995年也只有7亿左右。
PCB贴装方式
安装原则因要求不同而异。 这些要求包括元器件取放能力、贴装强度、贴装精度、贴装速度和助焊剂流动性。 在考虑安装速度时,要考虑的主要特性之一是安装精度。
挑选和安装
安装设备的安装头越少,安装精度越高。 x、y、θ定位 贴装头安装在贴装机x-y平面的支撑架上。 贴装头最重要的部分是旋转轴,但z轴的运动精度也不容忽视。 在高性能安装系统中,z轴的运动由微处理器控制,垂直移动距离和安装力由传感器控制。
安装的主要优点之一是精密安装头可以在 x 和 y 平面上自由移动,包括从格子板上取材料和在固定的高架相机上对器件进行多次测量。
最先进的贴装系统可以达到4 sigma,20 μm精度的主要缺点是贴装速度低,通常低于2000 cph,这还不包括其他辅助动作,例如倒装芯片助焊剂。
只有一个安装头的简单安装系统很快就会被淘汰,取而代之的是灵活的系统。 对于这样的系统,支撑架配备高精度贴装头和多吸嘴旋转头,可用于贴装大型BGA和QFP封装。 旋转(或射击)头可以处理不规则形状的器件、细间距倒装芯片和引脚间距小至 0.5mm μ BGA/CSP 芯片的器件。 这种装裱方法称为“采摘装裱”。
配备倒装芯片旋转头的高性能SMD安装设备已经出现在市场上。 可高速贴装直径125μm的倒装芯片和球栅。 引脚间距约为200μM的μBGA和CSP芯片。 具有收集、拾取、贴装功能的装置贴装速度约为5000cph。
传统晶圆吸枪
这种系统配备了一个水平旋转的旋转头,它同时从移动的供料器上拾取器件并将它们粘贴到移动的 PCB 上。
理论上系统的挂载速度可以达到40000cph,但是有以下限制:
芯片拾取不得超过放置器件的栅盘;
当弹簧驱动的真空吸嘴在z轴上移动时,不允许优化工作时间或可靠地从传送带上拾取芯片;
对于大多数面阵封装,贴装精度达不到要求,典型值高于4 sigma μ m的10%;
不能在微型倒装芯片上涂助焊剂。
收集和安装
在“收集和安装”吸枪系统中,两个旋转头都安装在 x-y 支撑架上。 然后,旋转头装有6个或12个吸嘴,可以接触栅板上的任何位置。 对于标准的SMD芯片,该系统在4 sigma(包括theta偏差)μm贴装精度和20,000 pch贴装速度下可以达到80%。 通过改变系统的定位动态特性和球栅搜索算法,该系统可以在4sigma中达到60%的平面阵列封装μM到80μM,贴装速度高于10000 pch。
安装精度
为了对不同的贴装设备有一个整体的了解,您需要了解影响表面阵列封装贴装精度的主要因素。 球栅P//ACC//的安装精度取决于球栅合金的种类、球栅的数量和封装的重量。
这三个因素是相互关联的。 与采用相同间距的QFP和SOP封装的IC相比,大多数平面阵列封装对贴装精度的要求较低。
注意:插入方程式
对于没有阻焊层的圆形焊盘,最大允许安装偏差等于PCB焊盘的半径。 当贴装误差超过PCB焊盘半径时,球栅与PCB焊盘仍会存在机械接触。 假设PCB焊盘直径大致等于球栅直径μ BGA和CSP封装的贴装精度要求为0.15mm; 如果球栅直径为100μm。间距为175μm。 精度要求为50 μ m。
在 TBGA 和 CBGA 的情况下,自对准是有限的。 因此,要求安装精度高。
助焊剂的应用
倒装芯片球栅的标准大型回流焊炉需要助焊剂。 现在,一般功能强大的SMD贴装设备都配备了内置的助焊剂应用装置。 两种常用的内置供电方法是涂层和浸焊。
涂层单元安装在安装头附近。 在倒装芯片安装之前,在安装位置涂抹助焊剂。 安装位置中心的涂层量取决于倒装芯片的尺寸和助焊剂对特定材料的润湿特性。 应保证助焊剂涂敷面积足够大,以免因失误造成焊盘缺失。
为了有效地填充非清洁过程,助焊剂必须是非清洁(无残留)材料。 液体助焊剂总是含有很少的固体物质,最适合非清洗工艺。
但由于液体助焊剂的流动性,在倒装芯片贴装后,贴装系统传送带的移动会引起芯片的惯性位移。 有两种方法可以解决这个问题:
在 PCB 传输之前设置几秒钟的等待时间。 在此期间,倒装芯片周围的助焊剂会迅速挥发以提高附着力,但这会降低产量。
您可以调整传送带的加速和减速以匹配助焊剂的附着力。 传送带的平稳运动不会引起切屑位移。
助焊剂涂敷法的主要缺点是周期比较长。 每个待镀器件,贴装时间增加约1.5s。
浸焊法
这种情况下,助焊剂载体是一个旋转的桶,刮成助焊剂薄膜(约50μm)这种方法适用于高粘度助焊剂。 通过简单地将助焊剂浸入网格底部,可以减少制造过程中的助焊剂消耗。
以下两个工艺顺序可用于此方法:
光栅和光栅浸入光通量对准后,进行安装。 按此顺序,倒装芯片球栅和助焊剂载体之间的机械接触将对安装精度产生负面影响。
球栅浸没通量和光学球栅对齐后,安装它们。 在这种情况下,助焊剂材料将影响光学球栅对准图像。
浸渍助焊剂法不适用于高挥发性助焊剂,但其速度比涂布法快得多。 根据挂载方式不同,每个设备的附加时间纯拾取挂载0.8s左右,采集挂载0.3s左右
当使用标准SMT贴装间距为0.5mm的球栅μBGA或CSP时,还有一些需要注意的地方:μBGA/CSP标准SMD)产品,显然最关键的工艺是助焊剂涂层印刷。 按理来说,传统的倒装芯片工艺和助焊剂的应用也是可以的。
所有平面阵列封装都显示出性能、封装密度和成本节约方面的潜力。 为了发挥其在PCB生产整体领域的作用,还需要进一步研发,改进制造工艺、材料和设备。 就SMD贴装设备而言,很多工作都集中在视觉技术、更高的产量和精度上。
然后
联系
电话热线
13410863085Q Q
微信
- 邮箱