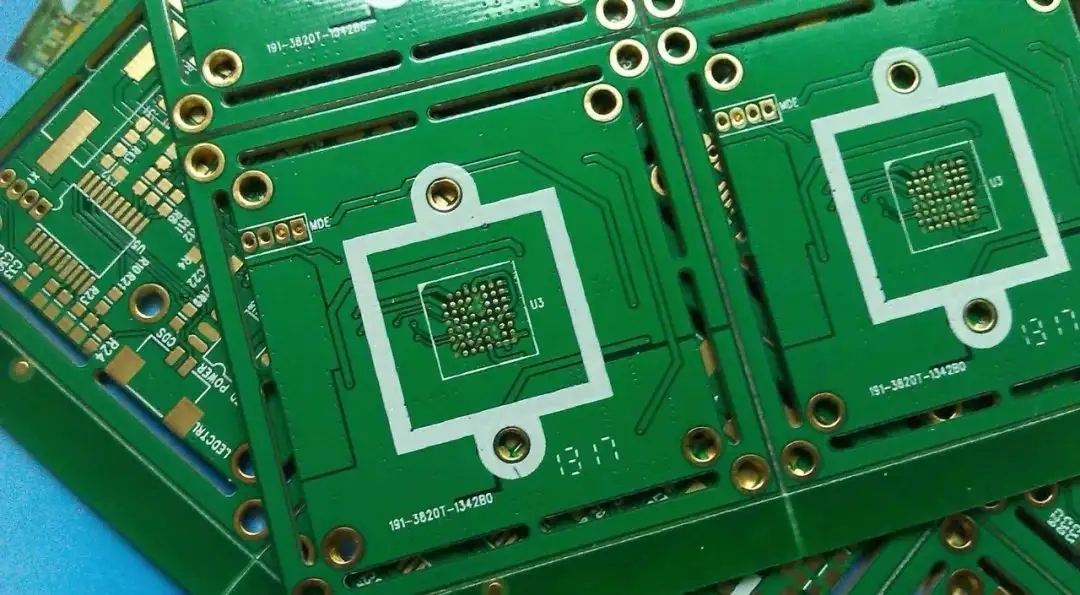
生产命脉——DFM技术要求汇总
DFM(可制造性设计)即面向制造的设计,是并行工程的核心技术。 设计和制造是产品生命周期中最重要的两个环节。 并行工程是在设计之初就考虑产品的可制造性和可组装性等因素。 因此,DFM是并行工程中最重要的支撑工具。 其关键是设计信息的过程分析、制造合理性的评价和改进设计的建议。 本文将简要介绍PCB工艺中DFM的一般技术要求。
一、一般要求
1、本标准作为PCB设计的通用要求,规范了PCB的设计与制造,实现了CAD与CAM的有效沟通。
2、我司在加工文件时优先以设计图纸和文件作为制作依据。
二、PCB材料
1、基材
PCB的基材一般为环氧玻璃布覆铜板,即FR4。 (包括单面板)
2、铜箔
99.9%以上的电解铜;
成品双层板表面铜箔厚度≥35? m(1OZ);如有特殊要求,应在图纸或文件中注明。
三、PCB结构、尺寸及公差
1、结构
a) 构成PCB的所有相关设计元素应在设计图纸中说明。 外观应统一由 MechanICal 1 层(优先级)或 Keep out 层表示。 如果在设计文件中同时使用,一般用keep out layer屏蔽不开孔,用mechanical 1成型。
b) 在设计图中,表示开长SLOT孔或镂空,可用机械1层画出相应的形状。
2、板厚公差
3、外形尺寸公差
PCB的外形尺寸应符合设计图的规定。 图纸未注明时,外形尺寸公差为±0.2mm。 (V-CUT 产品除外)
4、平面度(翘曲)公差
PCB的平面度应符合设计图的规定。 图纸无规定的,按下列规定执行
四、印制导线及焊盘
1.布局
a) 印制线和焊盘的布局、线宽、线距原则上应符合设计图纸的规定。 但我司会有如下处理:线宽和PAD环宽会根据工艺要求适当补偿。 对于单面板,我司一般会尽可能增加PAD,以增强客户焊接的可靠性。
b) 当设计线距不能满足工艺要求时(太密可能影响性能和工艺性),我司将根据制造前的设计规范进行适当调整。
c) 原则上建议客户设计单双面板时,过孔(VIA)内径设置在0.3mm以上,外径设置在0.7mm以上,线距8mil,走线 宽度为 800 万。 尽量减少生产周期和制造难度。
d) 我公司最小钻孔刀具为0.3,成品孔约0.15mm。 最小行间距为 6mil。 最细的线宽为6mil。 (但制造周期长,成本高)
2.导体宽度公差
印制线宽度公差内控标准为±15%
3.网格处理
a) 为避免波峰焊时铜面起泡,加热后因热应力导致PCB弯曲,建议将大铜面呈网格状铺设。
b) 网格间距≥10mil(不小于8mil),网格线宽≥10mil(不小于8mil)。
4.导热垫的处理
在大面积接地(电)中,常有元器件的腿与之相连。 连接脚的处理考虑了电气性能和工艺需要,做成十字形焊盘(隔热焊盘),可以大大降低焊接时因截面散热过多而产生虚焊点的可能性。
五、孔径(HOLE)
1、金属化(PHT)和非金属化(NPTH)的定义
a) 非金属开孔我司默认采用以下方法:
当客户在Protel99se高级属性中设置安装孔为非金属属性时(Advanced菜单中去掉勾选项),我司默认为非金属孔。
当客户直接使用设计文件中的keep out layer或mechanical 1 layer arc表示打孔时(不单独设置孔),我司默认为非金属孔。
当客户在孔附近标注NPTH字样时,我司默认为非金属孔。
当客户在设计通知中明确要求相应的孔径非金属化(NPTH)时,按客户要求处理。
b) 除上述情况外,元件孔、安装孔、通孔等应进行金属化处理。
2、孔径尺寸及公差
a) 设计图中的PCB元器件孔和安装孔默认为成品最终孔径。 孔径公差一般为±3mil(0.08mm);
b)通孔(即VIA孔)一般控制为:负公差不要求,正公差控制在+3mil(0.08mm)以内。
3、厚度
金属化孔镀铜层平均厚度一般不小于20? 米。 最薄处不得小于18? 米。
4、孔壁粗糙度
PTH孔壁粗糙度一般控制在≤32um
5、PIN孔问题
a) 我们数控铣床的最小定位销是0.9mm,三个PIN孔应该是三角形的。
b) 当客户无特殊要求且设计文件孔径小于0.9mm时,我司会在空白无线路径处或板内大铜面适当位置加PIN孔。
6. SLOT孔(SLOT孔)的设计
a) 建议SLOT孔用机械1层(Keep out layer)绘制; 也可用连接孔表示,但连接孔应大小相同,孔心在同一水平线上。
b) 我公司最小切槽刀为0.65mm。
c) 为避免高低压漏电而开SLOT孔屏蔽时,建议直径大于1.2mm,以方便加工。
六、阻焊层
1、镀层位置及缺陷
a) PCB除焊盘、MARK点和测试点以外的表面均需涂阻焊层。
b) 如果客户使用FILL或TRACK来表示圆盘,则必须在Solder mask层上绘制相应尺寸的图形来表示镀锡层。 (本公司强烈建议设计前不要使用非PAD演示板)
c) 如果需要在大铜皮上散热或在线带上喷锡,还必须绘制相应尺寸的带有阻焊层的图形,以指示镀锡层。
2、附着力
阻焊层附着力应符合美国IPC-A-600F 2级要求。
3、厚度
耐焊层厚度应符合规定
七、文字及蚀刻标记
1、基本要求
a) PCB字符一般设计为字符高30mil,字符宽度5mil,字符间距大于4mil,避免影响字符的可读性。
b) 蚀刻(金属)字符不应与导体桥接,应确保足够的电气间隙。 一般字高30mil,字宽7mil以上。
c) 如果客户对字符没有具体要求,我司一般会根据我方工艺要求调整字符的匹配比例。
d) 当客户无明确规定时,我司将按我司工艺要求在版材丝印层适当位置印上我司商标、料号、周期。
2、PAD SMT对文字的处理
PAD不得标示丝印层,以免虚焊。 当客户有PAD SMT设计时,我司会做适当的移动,以不影响其logo与器件对应为原则。
八、层的概念及MARK点处理层的设计
1、对于双面板,我司默认以顶层为正视图,顶层覆屏层的字符为正面。
2.、对于单面板,顶层用于绘制信号层,即该层的线为正视图。
3、单面板使用顶层绘制信号层,也就是说这一层的线是透视面。
MARK点设计
4、当客户有SMT做面板文件,需要用Mark点定位时,MARK一定要放好,圆直径1.0mm。
5、当客户无特殊要求时,我司采用Solder 1.5mm的圆弧来表示无阻焊剂,以增强识别性。 将一个放在 FMask 层上
6、当客户没有在面板文件的表面贴片工艺边缘放置MARK时,我司一般在工艺边缘的对角线中心加一个MARK点; 当客户对面板文件有无工艺边缘的表面贴片时,一般需要与客户沟通是否需要加MARK。
九、关于V-CUT
1、V切面板与面板之间没有缝隙,但要注意导体与V切中心线的距离。 一般情况下,V-CUT线两侧的导体间距应大于0.5mm,即单板导体间距距板边应大于0.25mm。
2、V-CUT线一般用保留层(Mech 1)层表示,所以板子中需要V-cut的部分只需要用保留层(Mech 1)层画出来, 最好在板连接处标注V-CUT字样。
3、如下图所示,V切后的剩余深度一般为板厚的1/3,可根据客户对剩余厚度的要求适当调整。
4、V-cut产品尺寸会因玻璃纤维断裂后被拉伸现象而略有超差,部分产品会大于0.5mm。
5、V-CUT刀只能走直线,不能走曲线和折线; 拉线板的厚度一般在0.8mm以上。
十、表面处理工艺
当客户无特殊要求时,我司默认采用热风整平(HAL)方式进行表面处理。 (即喷锡:63锡/37铅)
以上DFM通用技术要求(单双面板)供广大客户设计PCB文件时参考,希望能就以上几方面达成共识,更好的实现CAD与CAM的互通,更好的实现 可制造性设计(DFM)的共同目标,更好地缩短产品制造周期,降低生产成本。
以上DFM通用技术要求(单双面板)仅是世纪芯在设计PCB文件时为客户提供的参考,希望通过以上方面的协商和调解,更好的实现CAD与CAM的互通,更好的实现 可制造性设计(DFM)的共同目标,缩短产品制造周期,降低生产成本。
然后
联系
电话热线
13410863085Q Q
微信
- 邮箱