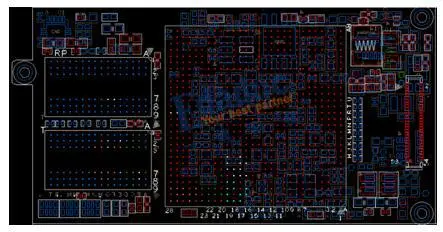
国内能够量产高水平电路板的企业主要来自外资企业或少数内资企业。 高水平电路板的生产不仅需要较高的技术和设备投入,还需要技术人员和生产人员的经验积累。 同时,高阶板客户认证程序引进严格繁琐,高阶电路板进入企业门槛高,产业化生产周期长。
PCB平均层数已成为衡量PCB企业技术水平和产品结构的重要技术指标。 本文简要介绍了在加工中遇到的主要难点,并介绍了高阶线路板关键生产工序的控制要点,以供参考。
一、主要生产难点
与常规电路板相比,高层电路板具有板厚、层数多、走线和过孔更密、单元尺寸更大、介质层更薄等特点。 控制和可靠性更加严格。
1.1 层间对准难点
由于高层板的层数较多,客户设计端对每一层PCB的走线要求也越来越严格。 通常,层与层之间的对准公差控制在±75μm。 考虑到高层板大单元尺寸设计、图文转印车间环境温湿度、不同芯板层数不一致造成的错位叠加和层间定位方式等因素,高层板层间走线控制难度加大。 上升板。
1.2 制作内线的难点
高层板采用高TG、高速、高频、厚铜、薄介质层等特殊材料,对内层电路制作和图形尺寸控制提出了高要求,如阻抗信号的完整性 传输,这增加了内层电路制作的难度。 线宽、线间距小,开短路次数增多,短路次数增多,合格率低; 细线信号层多,增加内层AOI漏检概率; 内芯板薄,易折叠,造成曝光不良,蚀刻时易卷边; 高层板多为单元尺寸较大的系统板,成品报废成本较高。
1.3 冲压制造难点
多个内层芯PCB与半凝固板重叠,压制生产时容易出现滑板、脱层、树脂空洞、气泡残留等缺陷。 在设计叠层结构时,需要充分考虑材料的耐热性、耐压性、灌胶量和介质厚度,为高层板设置合理的压合程序。 层数多,胀缩控制和尺寸系数补偿不能保持一致; 层间绝缘层薄,容易导致层间可靠性试验失败。 图1为热应力试验后裂纹板分层缺陷图。
1.4 钻井难点
采用高TG、高速、高频、厚铜特制板材,增加了钻孔粗糙度、钻孔毛刺和钻孔脏物去除难度。 层数多,总铜厚和板厚累加,钻具易折断; BGA密集、孔壁间距窄导致的CAF失效; 由于板材厚度的原因,容易出现斜钻。
二、关键生产过程控制
2.1 材料选择
随着电子元器件的高性能化、多功能化的发展,也带来了高频、高速的信号传输。 因此,要求电子线路材料具有低介电常数和介质损耗、低CTE、低吸水率和性能更好的高性能覆铜板材料,以满足高层板的加工和可靠性要求。 常用的PCB供应商主要有A系列、B系列、C系列和D系列。 比较了这四种内基板的主要特性。
对于高层厚铜线路板,选用树脂含量高的半固化片。 层间半固化片的胶流足以填满内层图形。 如果绝缘介质层太厚,成品板容易出现超厚现象。 否则,绝缘介质层过薄,容易造成介质分层、高压试验不合格等质量问题,因此绝缘介质材料的选择极为重要。
2.2叠层结构设计
叠层结构设计考虑的主要因素是材料的耐热性、耐压性、胶水填充量和介质层厚度,应遵循以下主要原则。
(1)预浸料和芯板厂家必须一致。 为保证PCB的可靠性,各层半固化片不得采用单一的1080或106半固化片(除非客户有特殊要求)。 如果客户对介质厚度没有要求,根据IPC-A-600G,层间介质厚度必须≥0.09mm。
(2)当客户要求高TG板材时,芯板和半固化片应采用相应的高TG材料。
(3)内基板为3OZ及以上,选用树脂含量高的半固化片,如1080R/C65%、1080HR/C 68%、106R/C 73%、106HR/C76%; 但106高胶半固化片的结构设计应尽量避免,防止多张106半固化片重叠。 由于玻纤纱太细,会在大基材区塌陷,影响尺寸稳定性和分层。
(4) 如果客户没有特殊要求,层间介质层的厚度公差一般控制在+/- 10%。 对于阻抗板,介质的厚度公差由IPC-4101 C/M级公差控制。 如果阻抗影响因素与基材厚度有关,则板材的公差也必须由IPC-4101 C/M级公差控制。
2.3 层间配向控制
对于内芯板尺寸补偿的准确性和生产尺寸的控制,需要通过生产中收集的数据和历史数据经验,对高层板各层图形尺寸进行准确补偿 一定的时间保证每层芯板升降的一致性。 压制前选择高精度可靠的层间定位方式,如四槽定位(Pin LAM)、热熔和铆钉组合。
设置合适的压合工艺规程和压合机的日常维护是保证压合质量、控制胶水流动和冷却效果、减少层间错位的关键。 层间对位控制需要从内层补偿值、压制定位方式、压制工艺参数、材料特性等因素综合考虑。
2.4 内层PCB电路工艺
由于传统曝光机的解析能力为50μm左右,对于高层板的生产制造,可引入激光直接成像机(LDI)提高图形解析能力,达到20μm左右 . 传统曝光机的对位精度为±25μm。 层间对位精度大于50μm。采用高精度对位曝光机,图形对位精度可提高至15μm,层间对位精度控制在30μm以内,对位偏差为 减少传统设备,提高高层楼板层间对位精度。
为了提高电路的蚀刻能力,需要在工程设计中对电路和PCB焊盘(或焊环)的宽度给予适当的补偿,并对特殊的补偿量进行更详细的设计考虑。 图形,如回线、独立线等。确认内层线宽、线距、隔离环尺寸、独立线、孔距线距的设计补偿是否合理,或更改工程设计。
有PCB阻抗和感抗设计要求,注意独立线路和PCB阻抗线路的设计补偿是否充分。 控制蚀刻过程中的参数。 确认首件合格后,方可进行批量生产。 为了减少侧蚀,需要将蚀刻液中各药液的成分控制在最佳范围内。 传统蚀刻线设备蚀刻能力不足。 可对设备进行技术改造或引进高精度蚀刻线设备,提高蚀刻的均匀性,减少毛边、蚀刻不干净等问题。
然后
联系
电话热线
13410863085Q Q
微信
- 邮箱