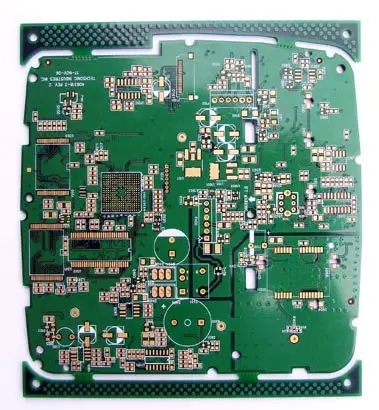
DetaiLED explanation of PCB process PCB layers
The Circuit board manufacturer and circuit board designer explain the PCB layers in detail
PCB layer:
a. Signal Layers: The signal layers include Top Layer, Bottom Layer, Mid Layer 1... 30. These layers are all layers with electrICal connections, that is, actual copper layers. The middle layer refers to the middle layer used for wiring, in which wires are laid.
b. Internal Plane: Internal Plane 1...... 16. These layers are generally connected to the ground and power supply to become the power supply layer and stratum. They also have the function of electrical connection. They are also actual copper layers, but generally they are not wired and are composed of a whole piece of copper film.
c. Silkscreen Overlay: including the top screen layer and the bottom screen layer. The silk screen characters that define the top and bottom layers are text symbols that are usually printed on the solder mask layer, such as component naMES, component symbols, component pins and copyrights, to facilitate future circuit welding and error checking.
d. Paste Mask: including the top paste layer and bottom paste layer. It refers to the exposed surface mounted pads that we can see, that is, the parts that need to be coated with solder paste before welding. Therefore, this layer is also useful for hot air leveling of pad and welding steel mesh fabrication.
E. Solder Mask: It includes Top solder and Bottom solder. Its function is opposite to that of Solder paste. It refers to the layer to be covered with green oil. This layer does not stick solder to prevent short circuit of excess solder at adjacent welding points during welding. The solder mask covers the copper film conductor,
The anti copper film oxidizes too quickly in the air, but leaves a place at the solder joint and does not cover the solder joint.
f. Mechanical Layers: Up to 16 mechanical layers can be selected. You only need to use the default option Mechanical Layer 1 to design double-sided panels.
g. Keep Out Layer: defines the boundary of the routing layer. After the forbidden wiring layer is defined, the wiring with electrical characteristics cannot exceed the boundary of the forbidden wiring layer in the subsequent wiring process.
h. Drill Layer: includes the drill guide and drill drawing, which are drilling data.
f. Multi layer: refers to all layers of PCB.
Meaning of each layer in Altium Designer
Mechanical
Keepoutlayer keepoutlayer
Topoverlay
Bottom overlay
Toppaste
Bottompaste
Top solder mask
Bottom solder
drillguide
Drilldrawing through hole drilling layer
1 Signal layer
The signal layer is mainly used to arrange the wires on the circuit board. Protel 99 SE provides 32 signal layers, including Top layer, Bottom layer and 30 MidLayers.
2 Internal plane layer
Protel 99 SE provides 16 internal power supply layers/grounding layers. This type of layer is only used for multilayer boards, mainly for laying power lines and grounding wires. We call it double-layer board, four layer board, and Six layer board, generally referring to the number of signal layers and internal power supply/grounding layers.
3 Mechanical layer
Protel 99 SE provides 16 mechanical layers, which are generally used to set the overall dimensions, data MARKs, alignment marks, assembly instructions and other mechanical information of the circuit board. The information varies according to the requirements of the design company or PCB manufacturer. Execute the menu command Design | Mechanical Layer to set more mechanical layers for the circuit board. In addition, the mechanical layer can be attached to other layers to output and display together.
4 Solder mask layer
Apply a layer of paint, such as solder mask, on all parts outside the bonding pad to prevent tin coating on these parts. The solder mask is automatically generated for matching pads during the design process. Protel 99 SE provides two solder mask layers: Top Solder and Bottom Solder.
5 Paste mask layer
Its function is SIMilar to that of the solder mask, but the difference is that the pad of the corresponding surface bonded component is welded by the machine.
Protel 99 SE provides two solder paste protective layers: Top Paste (top layer) and Bottom Paste (bottom layer).
Mainly for SMD components on PCB. If all the boards are placed with DIP (through hole) components, Gerber files do not need to be output for this layer. Before pasting SMD components onto PCB, solder paste must be coated on each SMD pad. The steel mesh for tin coating must need this Paste Mask file before film can be processed.
The most important thing to be clear about Gerber output of Paste Mask layer is that this layer is mainly for SMD components. At the same time, compare this layer with the Solder Mask introduced above to find out the different functions of the two layers, because the two film images are very similar from the film image.
6 Keep out layer
It is used to define the area where components and wiring can be effectively placed on the circuit board. Draw a closed area on this layer as the valid routing area. You cannot automatically layout and route outside this area.
7 Silkscreen layer
The silk screen layer is mainly used to place printed information, such as outline and annotation of components, various annotation characters, etc. Protel 99 SE provides two silk screen layers: Top Overlay and Bottom Overlay. Generally, all marking characters are on the top screen layer, and the bottom screen layer can be closed.
8 Multi layer
The bonding pad and through-hole on the circuit board should penetrate the whole circuit board and establish electrical connection relationship with different conductive graphic layers. Therefore, the system has set up an abstract layer - multilayer. Generally, pads and vias must be set on multiple layers. If this layer is closed, pads and vias cannot be displayed.
9 Drill layer
The drilling layer provides the drilling information during the manufacturing process of the circuit board (such as the pad, through hole drilling is required). Protel 99 SE provides two drilling layers, namely, Drill grid and Drill drawing.
Differentiation between solder mask and flux
Solder mask: Solder mask refers to the part of the board to be coated with green oil; Because it is a negative output, the actual effect of some solder mask is not green, but tinned, silver white!
Soldering aid layer: paste mask, which is used when the machine is mounted, is the bonding pad corresponding to all mounting elements, and is the same size as the toplayer/bottomlayer layer. It is used to open the tin leakage of the steel mesh.
Key points: both layers are used for tin coating and welding, not one for tin coating and one for green oil coating; Is there a layer that is covered with green oil? As long as there is a layer on an area, it means that the area is covered with insulating green oil? I haven't met such a layer yet! By default, the pads on the PCB we drew all have a solder layer, so the pads on the PCB we made are coated with silver solder, which is not surprising; However, the wiring part on the PCB we drew only has the top layer or bottom layer layer, and no solver layer. However, the wiring part on the PCB made is covered with a layer of green oil.
It can be understood as follows:
1. Welding resistance layer means to open a window on the whole piece of welding resistance green oil, so as to allow welding!
2. By default, areas without solder mask should be painted green!
3. The paste mask layer is used for chip packaging! SMT encapsulation uses: the toplayer layer, the topsolver layer, and the toppaste layer. The toplayer is the same size as the toppaste, and the topsolver is one circle larger than them. DIP encapsulation only uses: topsolder and multilayer layers (after some decomposition, I found that the multilayer layer is actually the top layer, bottomlayer, topsolder, and bottomsolver layers with overlapping sizes), and the top layer/bottomsolver is one circle larger than the top layer/bottomlayer.
Definition and description of each layer of PCB:
1. TOP LAYER: It is designed as the top copper foil routing. If it is a single panel, there is no such layer.
2. BOMTTOM LAYER: It is designed as the bottom copper foil routing.
3. TOP/BOTTOM SOLDER. The welding pad, through hole and the non electrical wiring of this layer shall be welded with green oil to open the window.
By default, the bonding pad will open a window (OVERRIDE: 0.1016mm) in the design, that is, the bonding pad will expose copper foil, expand 0.1016mm, and tin will be applied during wave soldering. No design change is recommended to ensure weldability;
By default, the vias will open a window (OVERRIDE: 0.1016mm) in the design, that is, the vias will expose copper foil, expand 0.1016mm, and tin will be applied during wave soldering. If it is designed to prevent the vias from being tinned and copper exposed, the PENTING option in SOLDER MASK, the additional attribute of the vias, must be checked to close the vias.
In addition, this layer can also be used for non electrical wiring separately, so the green oil of resistance welding shall be opened accordingly. If it is on the copper foil wiring, it is used to enhance the over-current capacity of wiring, and tin is added during welding; If it is on the non copper foil wiring, it is generally designed to be used for identification and special character silk screen printing, which can save the production of character silk screen layer. 4. TOP/BOTTOM PASTE (top/bottom solder paste layer): This layer is generally used to apply solder paste during SMT reflow soldering of SMT mounting components. It has nothing to do with the board manufacturing of the PCB manufacturer. It can be deleted when exporting GERBER, and it can be left as default when PCB design.
5. TOP/BOTTOM OVERLAY (top/bottom silk screen layer): designed for various silk screen identifications, such as element tag number, character, trademark, etc.
6. MECHANICAL LAYERS: It is designed as PCB mechanical shape, and LAYER1 is the shape layer by default. Other LAYER2/3/4, etc. can be used for mechanical dimension marking or special purposes. For example, LAYER2/3/4, etc. can be used when conductive carbon oil is required for some boards, but the purpose of this layer must be clearly identified on the same layer.
7. KEEPOUT LAYER: It is designed as a no wiring LAYER, and many designers also use it to make PCB MECHANICAL shapes. If there are KEEPOUT and MECHANIC LAYER1 on the PCB, it mainly depends on the shape integrity of these two layers, and MECHANICAL LAYER1 generally prevails. It is recommended that MECHANICAL LAYER1 be used as the profile layer as far as possible during design. If KEEPOUT LAYER is used as the profile, MECHANICAL LAYER1 should not be used again to avoid confusion!
8. MIDLAYERS (intermediate signal layer): It is mostly used for Multilayer boards, but rarely used in our design. It can also be used as a special purpose layer, but its use must be clearly identified on the same layer.
9. INTERNAL PLANES (internal power layer): It is used for multilayer boards, but not designed by our company.
10. MULTI LAYER: Through hole pad layer.
11. DRILL GUIDE (drilling locating layer): the center locating coordinate layer of the drilling holes of pads and vias.
12. DRILL DRAWING: the description layer of the drilling hole size of the pad and vias.
In DESIGN -- OPTION, there are:
(Signal layer), Internal Planes
(internal power supply/ground plane), mechanical
Layers
Masks
Silk screen
Others
And System,
Executed during PCB design
The line menu command [Design] Design/[Options...] can set the visibility of each working layer.
留下您的评论
您的电子邮件地址不会被泄露。
然后
联系
电话热线
13410863085Q Q
微信
- 邮箱