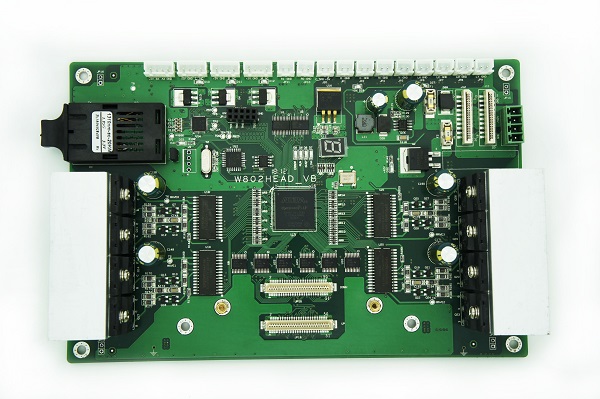
I. SMT assembly
The printing of solder paste and the systematIC quality control details of reflow temperature control are the key points in the PCBA manufacturing process. At the same time for special and complex process of high precision circuit board printing, it is necessary to use laser steel mesh according to the specific situation, in order to meet the higher quality requirements, processing requirements more demanding circuit board. Depending on PCB manufacturing requirements and customer's product characteristics, some may need to add U holes or reduce steel mesh. The steel mesh needs to be processed according to the requirements of PCBA processing technology.
Among them, THE temperature control accuracy of REFlow furnace is very important for the wetting of solder paste and the firm welding of steel mesh, which can be adjusted according to the normal SOP operation guide. To maximize the reduction of PCBA patch processing in the SMT link quality defects.
In addition, strict implementation of AOI test can greatly reduce the adverse effects caused by human factors.
2, the DIP plug-in after welding
DIP plug-in after welding circuit board in the processing stage is the most important, but also in the final process. In the process of post-welding DIP plug-in, the consideration of the over-wave welding fixture is very critical. How to use the furnace fixture to greatly improve the yield, reduce tin, tin, tin deficiency and other welding defects, and according to the different requirements of customers' products, PCBA processing plant must constantly summarize experience in practice, in the process of experience accumulation to achieve technical upgrading.
3, test and procedure firing
The manufacturability report is an evaluation work before the whole production after we receive the production contract from the customer. In the early DFM report, we should provide some suggestions to the customer before the PCB processing, such as setting some key test points on the PCB (test points). In order to carry on the PCB welding test and the subsequent PCBA processing after the key test of circuit conductivity, connectivity. When conditions allow, you can communicate with the customer to provide the back-end program, and then through the burning device to burn the PCBA program to the core control IC. In this way, it is more concise to test the circuit board through the touch action, so as to test and inspect the integrity of the whole PCBA, and find the defective products in time.
4. PCBA manufacturing test
In addition, many customers looking for PCBA processing one-stop service also have requirements for back-end testing of PCBA. The contents of such tests generally include ICT (circuit test), FCT (function test), burn test (aging test), temperature and humidity test, drop test, etc.
5. What should be paid attention to after PCBA sampling?
After we make samples in PCBA, some PCB boards are SMAll in size and need to be spliced for production efficiency. When finishing PCBA processing, PCBA splicing boards need to be spliced. Therefore, in the process of plate separation, some precautions should be paid attention to to prevent damage to the complete PCBA board.
It should be noted that the lower edge of the PCBA board must be held with both hands when folding the edge, 20mm above the V-shaped incision, to avoid bending deformation and damage to the PCBA electrical circuit, parts and tin groove.
Requirements for machine board:
1, stable support point
Without support, the resulting stress may damage the substrate and weld points. Distorting the plate or creating different stresses in the assembly process during plate separation may develop to cause hidden information or obvious defects.
2. Wear protective tools
Protection should be prepared before operation, and high frequency eye protection lighting device should be instalLED to protect the safety of operators. It's best to bring a pair of eyes to keep them safe.
3. Wipe the SPIndle and tools of the machine tool with alcohol frequently to remove PCB dust generated in the process of board division and keep the board running normally.
4. When using for a certain number of times, smooth the slider, bearing and oiling of the plate splitter, check whether the screw is loose, etc.
5, in the process of machine learning application and development, the table surface should adhere to a clean, the best not to place other things, to avoid these things fall on the tool and the formation of tool damage and damage to the goods. Although there are electric eyes for management and maintenance, we should pay attention to keep a certain safety protection interval between fingers and knives in the process of practical application history.
In general, when using PCBA partitioning, machine partitioning is more important than manual partitioning, because machine partitioning is efficient and has low damage rate. However, when the machine is divided, the process is also strictly followed to reduce human error. The above is the share of Kingford Electronics Xiaobian. I hope that more people can have some help in PCBA proofing.
然后
联系
电话热线
13410863085Q Q
微信
- 邮箱