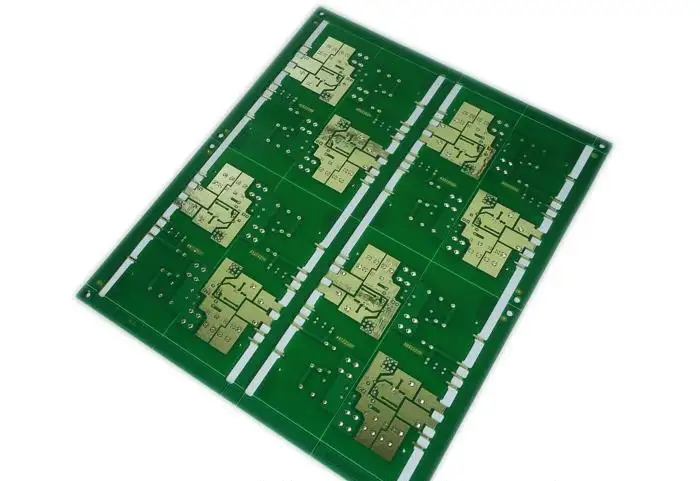
Pcb factory: introduction to the basIC knowLEDge of solder paste
Tin Powder
Tin powder, also known as metal alloy, is mainly used to reflect the welding strength. Its main components include: Sn (tin), Ag (silver), Cu (copper), Bi (bismuth).
Tin powder may have different components and ratios due to different solder paste numbers, but even if it has the same number but different brands, its components may be slightly different, some may be to avoid patents, and some may be their own secret recipe. Take SAC305, the most widely used solder paste at present, for example, tin (Sn, 96.5%), silver (Ag, 3%) and copper (Cu, 0.5%); SAC0307, on the other hand, uses solder paste with the ratio of tin (Sn, 99%), silver (Ag, 0.3%) and copper (Cu, 0.7%).
In addition to the different components of tin powder, the particle size of tin powder is also different, and the number of tin powder is given according to different tin powder sizes. However, the number of tin powder size is not uniform to be honest, but each brand probably uses the tacit understanding that the SMAller the number, the larger the particle.
The number and diameter of tin powder are roughly as follows. The following table is based on [IPC J-STD-006A]. However, each solder paste supplier actually has other tin powder number specifications, such as Type 4.5, Type 7 and Type 8 to meet the needs. The specifications beyond the specifications may be slightly different from each other
The smaller the diameter of tin powder, the better the amount of tin falling. Because the smaller the particles, the easier it is to roll off the opening of the steel plate, that is, the easier it is to print on the circuit board through the steel plate, and the more difficult it is to remain on the opening edge of the steel plate, which helps improve the printing ability of the parts with fine spacing, and also can achieve consistent solder paste printing amount; The smaller tin powder can also improve its collapse resistance, and the wetting effect is also better.
However, the smaller the tin powder is, the easier it is to oxidize. It may be necessary to use nitrogen (N2) to reduce its oxidation speed to achieve a good tin eating effect, especially when using parts with large welding pads above 5 (such as shielding frame). This is because the smaller the tin powder, the larger its contact area with the air, so it is easier to oxidize. Therefore, when selecting solder paste, it is not the smaller the tin powder particles, the better, but it depends on the product demand, and it is also necessary to specify the uniformity of solder paste particles.
Generally, No. 3 tin powder is used for SMT bonding, while No. 4 tin powder is used for fine pitch or small pad bonding. Tin powder of Type 5 and Type 6 is usually used on the bump of [Flip chip] or [CSP]. The lower the price of tin powder, the more expensive it is, because it is not easy to produce.
Although we do not want the solder paste to be oxidized, there will still be some oxidation residues after the solder paste is treated. In particular, some micro oxidation on the surface of metal particles can prevent the solder paste from merging before it is officially printed on the circuit board. Because the same pure metal will have the problem of mutual integration when placed together, it is called "birds of a feather flock together".
Oxidation basically has three elements: temperature, air and water.
The shape of tin powder can be spherical or elliptical. Spherical printing has wide application scope, small surface area, low oxidation degree and bright solder joints; Oval shape is worse.
Flux
Flux is actually the biggest driver to turn solder paste into paste, because the solvent contained in the flux can mix all substances together to form a paste.
The purpose and main function of "flux" is to remove oxides and dirt on the metal surface. In addition, it can form a film on the metal surface during high-temperature operation to isolate the air and prevent the solder paste from oxidation. Its composition mainly includes the following four components:
Resin rosin: 40-50%.
It can be divided into natural resin (Rosin) or synthetic rosin (Resin). Rosin is usually used for lead solder paste, while Resin is used for lead-free solder paste. Rosin can form a protective layer on the surface of the metal to be welded to isolate air, so it can be oxidized, sticky, and has the ability to slightly clean the metal surface.
Activator: 2-5%.
The main components are organic acid and halogen, which have the ability to strongly clean the metal surface. It is often used as a cleaner in the reflow process, which can dissolve the oxides on the metal surface and improve the welding effect. Halogen is highly toxic. In order to meet today's environmental protection needs, halogen-free solder paste has become a trend, but its deoxidation capacity is super strong and cheap, so it is still often used in some solder pastes,
Solvent: 30%.
Contains ethanol, water and other ingredients. These solvents evaporate in the preheating process of the solder paste, so they will not affect the solderability of the entire solder paste. They can help dissolve and mix different chEMIcals in the flux, make the coating of the flux more uniform, improve the effect of the flux, and make the flux easier for people to master. They can be used to control the viscosity and fluidity of the solder paste. If the preheating temperature of the reflow heats up too fast, these solvents may boil immediately and cause the problem of solder paste splashing.
Thickener: 5%.
Thixotropy or shake property is provided to control the viscosity of solder paste, enhance the anti collapse property of solder paste, and keep the original shape of solder paste after it is printed on the circuit board without causing short circuit.
In addition, one thing must remind you that if the ratio of solder paste is calculated by weight, the ratio of solder powder to flux is about 90%: 10%, because the solder powder is relatively heavy; However, if the ratio is calculated by volume, the ratio of solder powder to flux is about 50%: 50%, which will affect the calculation of solder paste amount after welding.
The Circuit board manufacturer and circuit board designer will introduce the basic knowledge of solder paste.
然后
联系
电话热线
13410863085Q Q
微信
- 邮箱