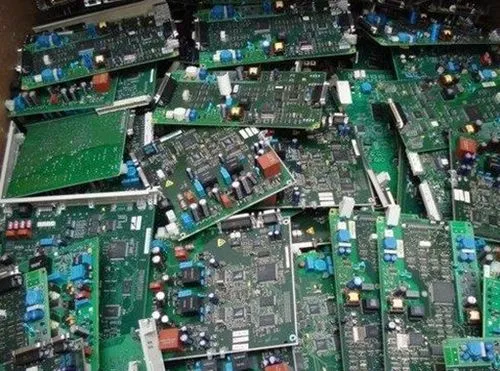
In the production process of batch PCB processing, in order to avoid the problem of scrapping and replenishment of FPC boards caused by too many short circuit faults resulting in too low qualifICation rate or reducing rough machining process problems such as punching, injection molding, laser cutting, and to evaluate how to select materials to achieve the best practical effect of customer application of soft circuit boards, pre production preparation seems especially critical.
There are three aspects that must be solved in the pre production preparation, all of which are carried out by technical engineers. The first is FPC board project evaluation, which is mainly to evaluate whether customers' FPC boards can be produced and manufactured, and whether enterprises' production capacity can consider customers' plate making process regulations and product costs; If the engineering project evaluation is based on, the next step is to immediately prepare materials, consider the balance between supply and demand of raw materials at each production and manufacturing stage, and finally, the technical engineer will solve the following engineering documents: the customer's CAD framework, gerber route materials, and so on, so as to adapt the working environment of the production line equipment and the production and manufacturing specifications and models, Then, the production and manufacturing engineering drawings and MI (engineering project step card) and other materials will be distributed to the Production Technology Department, the document control department, the purchase department and other departments to enter the basic production process flow.
In general, "stack design" refers to the design of the cumulative arrangement method of wiring layers and plane layers.
1. Foil stacking method is highly recommended for PCB stacking.
2. Minimize the application of PP sheet and CORE model, specification and type in the same stack (no more than 3 PP layers for each layer of material).
3. The thickness of PP material in the middle of the double layer does not have to exceed 21MIL (thick PP material is difficult to process, which generally increases the total number of specific layers by raising a blockboard, thus increasing the production cost)
4. The surface layer (top and bottom layers) of PCB generally adopts 0.5OZ thin copper foil, and the inner layer generally adopts 1OZ thin copper foil. Double sided circuit board
It shows that the thickness of copper foil is generally determined according to the size of electric flow and wiring. For example, 2-3OZ copper foil is generally used for power boards, and 1OZ copper foil is generally selected for data signal boards. If the wiring is too thin, 1/3QZ copper foil will be used to improve the product qualification rate; In addition, blockboard with inconsistent thickness of double-sided copper foil shall be prevented from being applied in the inner layer. (Production and manufacturing of double-layer circuit boards)
5. The overall surface layer of the wiring layer is distributed, and the left and right symmetry of the axis stacked from the PCB board is specified (including the number of layers stacked, the distance from the axis, the copper thickness of the wiring layer and other main parameters)
It shows that the PCB stacking method needs to use symmetrical design, which refers to the cable sheath thickness, sEMI dry fixed sheet type, copper foil thickness, and the types of patterns (large copper foil layer, road line layer) that are as relative to the axial symmetry of the PCB as possible. (Production and manufacturing of double-layer circuit boards)
6. Sufficient capacity must be reserved for the design of graphic boundary and material thickness to prevent SI and other design problems caused by insufficient capacity. Dingji has 15 years of experience in plate making process, and has been committed to manufacturing double-layer PCB for years
In the SMAll quantity PCB design and production, the switching power supply ground plane layer is used for wiring, or the switching power supply and ground network are used for wiring. The design of this kind of mixed type is uniformly calLED the data signal layer. Double layer differential signal characteristic impedance Circuit board manufacturer
High precision circuit board
Etching machine for PCB
Flowability of the board directly under the roller
Why are the etching methods of PCB inner surface different
Inner layer: development → etching → detachment
Surface layer: development → two copper electrotinning → separation → etching → tin stripping
Why did you do that? Isn't there a lot of process flow for surface etching?
Generally, the distance between the boundary lines of the inner layer is large, so Ring ring is enough; Generally, the surface course is dense, and the indoor space is insufficient, so at this time, we must find a way to make the route destination in the insufficient indoor space. The working capacity of alkali corrosion can reach 1~1mil of ring, but acid corrosion must be 5mil, so it is necessary to use tin to maintain the necessary route first. In areas where alkali corrosion can be avoided, it shall be avoided as much as possible, because the cost of alkali corrosion increases in acid corrosion. Etching factor is the ability of a processing plant to make products, which cannot be improved according to the process flow. The etching ability of acid and alkali etching is different.
Double layer circuit board is a necessary material for the development trend of electronic information technology towards high-speed operation, intelligence, large space and small volume. With the continuous development trend of electronic information technology, especially the widespread and deep application of scale and integrated circuit process integrated circuit chips, double-layer printed circuit is rapidly developing towards high-density, high-precision, high-rise residential digital direction, which brings up such technicalities as ultra-fine wire frame, small diameter surround, and high plate thickness diameter ratio of buried holes to consider the need of sales MARKet. Due to the necessity of high speed power supply circuits for electronic computers and aerOSPace industry production, double-sided circuit boards are required to further improve the relative density of packaging, together with the smaller size of separated components and the rapid development trend of microelectronics, the volume of electronic products will become smaller and the quality of electronic products will be relieved; Single and double-sided PCB boards are unlikely to complete the further improvement of installation relative density because of the limitation of indoor space. Therefore, it is necessary to consider the application of printed circuits with more layers than double-sided circuit boards. This created a standard for the emergence of double-layer circuit boards.
Which problem should be paid special attention to when designing the wiring of 4-layer PCB
1、 At least 3 points shall be connected to the upper part of the line, and the line shall be connected according to each point as far as possible to facilitate detection. Before the pin position, * * * construction setting out is not necessary, especially in the middle and periphery of the integrated circuit chip pin position. Lines * * * in the middle of different levels do not have to be parallel to prevent the production of actual capacitors.
2、 When designing the 4-layer circuit board, the wiring design should be parallel lines or 45 degree curves as much as possible, because it can prevent electromagnetic wave radiation. The grounding wire and power plug should be at least 10-15mil above each other, and the paved multiple wires should be connected together as much as possible to improve the total area of the grounding device. The middle of the wires should be as neat as possible. High precision double-sided circuit board
3、 Pay attention to the symmetrical blowdown of the element device, which is convenient for installation, software and welding. The layout of the blowdown parts shall be reasonable, and attention shall be paid to prevent them from being blocked. In addition, the structure shall be taken into account for the blowdown of the element device. The positive and negative parts of the chip mounted element device shall be marked in the package and finally to prevent the contradiction of indoor space.
4、 At present, the 4-layer circuit board can print 2mil PCB wiring and 2mil line torque. When wiring, more consideration should be given to the hazards of the injected current. The functional block components should be put together as much as possible. The LCD peripheral components such as the Bama strip should not be too close. The bonding pad should be coated with green oil (set to a negative value).
然后
联系
电话热线
13410863085Q Q
微信
- 邮箱