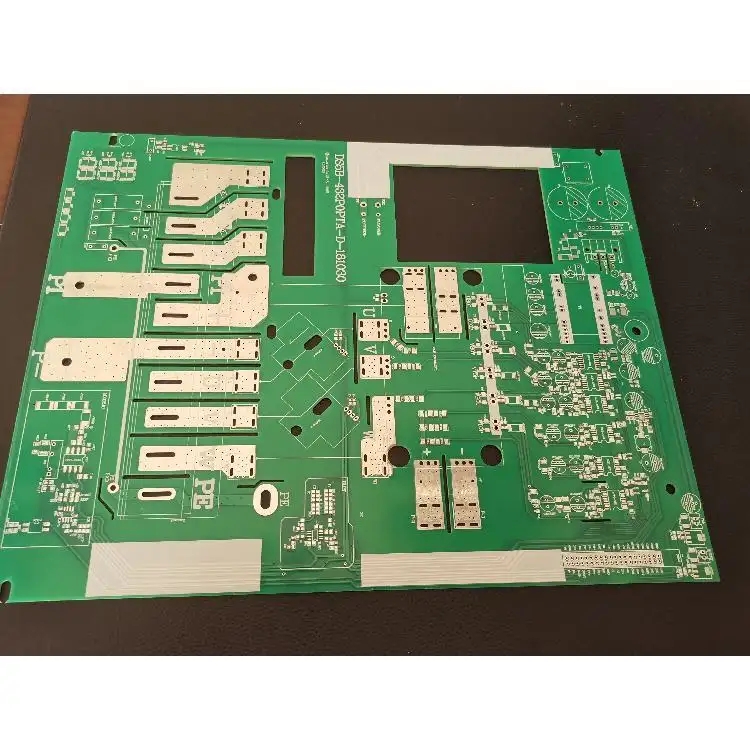
About electroplating technology of circuit board factory
Today, I would like to share with you about electroplating in the Circuit board factory.
About electroplating technology of circuit board factory
The copper thICkening of the outer circuit of the printed circuit board is mainly completed by electroplating copper. Generally, there are two electroplating methods in the circuit board factory, one is full board electroplating (full board electroplating), and the other is graphic electroplating. Pattern electroplating is to protect conductor copper parts that do not need copper plating with dry film after pattern transfer of printed circuit board, expose the conductor and connecting plate that need copper plating, and conduct selective copper plating on these parts, and then conduct Sn (or Sn/Pb) corrosion inhibitor plating. After electroplating, the printed circuit board can get the outer circuit after removing the film, etching, and removing the resist.
The whole pattern electroplating process is generally completed on the same production line, and the processes of film removal, etching, and resist removal after electroplating are carried out on another production line. Electroplating technology is mainly based on chEMIcal principles.
So what processes should PCB manufacturers carry out when conducting graphic electroplating?
Inspection: The circuit board factory (Shenzhen circuit board) mainly checks whether there is redundant dry film, whether the lines are complete, and whether there is dry film residue in the hole during inspection.
Degreasing: In the process of image transfer, after film pasting, exposure, development, inspection and other operations, there may be fingerprints, dust, oil stains, and residual film on the board. If the treatment is not good, the copper coating and the base copper will not bond firmly. At this time, the dry film and bare copper coexist on the PCB, and the oil removal should not only remove the oil stain on the copper surface, but also not damage the organic dry film. Therefore, acid oil removal is selected. The main components of the degreasing fluid are sulfuric acid and phOSPhoric acid. Our circuit board manufacturers are very careful when waking up, because it involves chemical substances.
Micro etching: remove the copper oxide layer in the line and hole, and increase the surface roughness to improve the combination of the coating and the base copper. There are two types of commonly used micro etching solutions, persulfate type and sulfuric acid hydrogen peroxide type, of which the persulfate type is mainly sodium persulfate and ammonium persulfate. Ammonium persulfate micro etching solution is easy to decompose, and the decomposed ammonia will affect the environment, which is not conducive to environmental protection, and the micro etching rate is also unstable. Sodium persulfate micro etching solution is stable, easy to control, and has a long service life. The sulfuric acid hydrogen peroxide system is unstable, easy to decompose and volatilize, and the micro etching rate fluctuates greatly, but its wastewater is easy to be treated, which is conducive to environmental protection.
Acid leaching: circuit board factory (Shenzhen circuit board) generally conducts copper electroplating or tin electroplating in acidic environment. In order to prevent moisture from entering, it needs to undergo acid leaching treatment before electroplating.
In addition, there are some SMAll details that our PCB manufacturer (Shenzhen PCB Factory) should pay attention to.
(1) Power supply
The ripple coefficient of acid decanoate sulfate tin plating power supply should be less than 5%, otherwise it is difficult to obtain an ideal tin coating.
(2) Mixing
The plating solution needs to be stirred strongly, but it cannot be stirred with air to prevent Sn2+from being oxidized. Cathode movement and
Continuous filtration is performed SIMultaneously. The solution shall be filtered at least 2-3 tiMES/hour.
(3) Anode
The purity of tin bar or tin ball shall be higher than 99.9%. Polypropylene cloth shall be used as anode bag to prevent anode mud from entering the solution.
PCB manufacturers, PCB designers and PCBA manufacturers will explain the electroplating technology of PCB manufacturers.
然后
联系
电话热线
13410863085Q Q
微信
- 邮箱