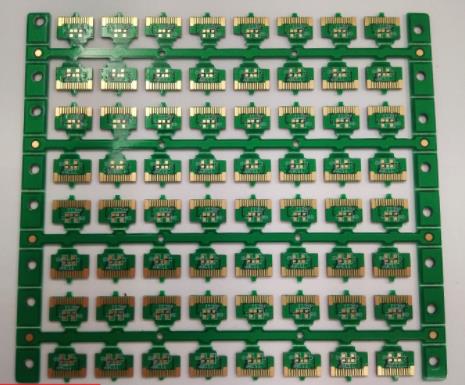
TechnICal level and development trend of circuit board protection components
PCB manufacturers, PCB designers and PCBA manufacturers will explain the technical level and development trend analysis of PCB protection components industry
1. Technical level
There are high technical barriers in the circuit protection component industry. Enterprises in developed countries such as Europe, America and Japan hold the core technologies and standards of the leading industry development direction, while outstanding enterprises in countries such as South Korea and China have some key technologies and have certain advantages in product design and manufacturing. At present, the main indicators of the technical level of the industry are as follows:
First, the ability to design and assemble production equipment. Although the annual output value of the global circuit protection component MARKet has reached US $6 billion, it is difficult to standardize the required production equipment due to the wide range of product series and specifications. There are few manufacturers of professional circuit protection component production equipment in the market, so manufacturers need to develop and design their own equipment, and then make their own equipment or find industrial machine tool manufacturers to customize or purchase relevant equipment according to industry experience for self assembly and debugging.
Second, the ability to select customized raw materials. As the safety components for circuit protection, circuit protection components have wide application fields. The performance requirements for circuit protection components vary from application field to application field, so the raw materials for circuit protection components have different requirements. To meet the different requirements of downstream customers, circuit protection component manufacturers need to have strong raw material selection and customization capabilities.
Third, flexible production capacity of products. The products provided by circuit protection component enterprises have the characteristics of multiple varieties, multiple batches, nonstandard and high-precision. Therefore, the manufacturers are required to have a perfect quality control system and flexible production capacity, so that the production is modular and flexible, and they can produce as many product varieties as possible in the same system to meet the market demand of multiple industries, multiple customers and products of different specifications.
Fourth, green production capacity. On the one hand, the EU has formulated REACH regulations, RoHS directives and other strict environmental requirements for products sold in these countries and regions; On the other hand, SONY, CANON and other end users have also developed green partner certification with stricter environmental requirements. Therefore, circuit protection component manufacturers need to select appropriate materials and green manufacturing processes, which is also an important means for manufacturers to occupy the market.
Fifth, core production link technology:
① Melt processing technology. The fusible processing technology is the key manufacturing process of tubular fuse, radial lead fuse, power fuse and other over-current protection components, including fusible molding, wire winding and tin ball spotting. The fusible size, wire winding pitch, tin ball diameter and consistency determine the fusible characteristics and stability of the product.
② Welding production process. The welding production link refers to the welding between the fusible (or PPTC chip) and the end electrode. If the welding process is not perfect, the contact resistance of the welding part will increase, which will affect the performance of the over-current protection components and affect the circuit protection function of the over-current protection components.
Welding is a key link in the production of over-current protection components, which has high technical difficulty. First of all, in order to meet the environmental requirements of REACH regulations and RoHS directives, lead-free soldering tin is required in the welding process. Compared with lead soldering tin, lead-free soldering tin has a higher melting point and poor tin loading capacity. If the welding process is not perfect, qualified circuit protection components will not be produced. Secondly, due to the SMAll volume of the fuse or self restoring fuse, the welding process temperature control must be accurate to ensure that the fuse link (or PPTC chip) is firmly welded to the end electrode. Taking the welding process of tubular fuse as an example, the welding of tubular fuse is to pre install soldering tin in the copper cap of the end electrode for heating welding. When one end of the tubular fuse has been welded and seaLED, the air in the pipe is expanded by the welding heat conducted and the pressure rises rapidly; To weld the copper cap at the second end, if the welding temperature is slightly higher, the soldering tin is easy to be pressed out of the copper cap by the high-pressure air in the pipe. If the welding temperature is slightly lowered, it is easy to occur that the fusible metal is not firmly welded, and the soldering tin has solidified. Good welding is difficult to achieve.
③ Screen printing and sintering technology. Screen printing and sintering technology is the key manufacturing process of SMD fuse link, which refers to the high-temperature sintering molding of silver paste after it is accurately printed on the ceramic substrate. The accuracy of the width and position of the silver paste determines the electrical properties of the fuse.
④ Punching forming technology is the key manufacturing process of power fuse, which refers to the use of laser or related machinery to punch the fusible parts according to the designed narrow diameter and reducing hole. The location, size and regularity of narrow diameter and reducing hole determine the electrical properties of power fuse.
⑤ Formula refining, that is, selecting suitable polymers such as polyethylene and conductive particles such as carbon black for mixing, refining, sheeting, electrode recombination and irradiation in a certain ratio, is the key manufacturing process of self restoring fuses, which determines the electrical performance and product quality of self restoring fuses, as well as the application fields of self restoring fuses.
2. Development trend
(1) Small size, high performance
The development trend of the downstream market determines the future development path of circuit protection components. In recent years, the downstream market, whether electronic products, Automotive electronics or various power equipment in the industrial field, has increasingly high requirements for miniaturization and integration, so the size requirements for basic electronIC components such as capacitors, inductors, resistors and circuit protection components are also increasingly demanding. The application of Surface Mount Technology is the representative of this development trend. The future product development direction is the high-performance components that are smaller and conform to the EIA standard (UL248-1/14). 0603 surface mount self restoring fuse, 0402 SMD fuse, etc. are currently the key product series in the industry.
While reducing the size of circuit board protection components, their electrical performance must be continuously improved and optimized: ① Low interference, when the circuit is operating safely, the impact of protection components on circuit operation should be as low as possible; For example, the resistance of overcurrent protection components shall be as low as possible. At present, the resistance of ultra-low resistance self restoring fuse can be reduced by 70% compared with conventional products under the condition of the same size, while the chip mounted ultra-low resistance self restoring fuse can be reduced by more than 80%. ② High precision, when the circuit is abnormal, the protection components can react quickly.
(2) Multi function and integration
By using array technology, SIMilar or different circuit protection components can be combined together on the printed circuit board, or even other electronic components can be combined to become a multi-functional electronic module, which can not only double the density of components on each printed circuit board, make component layout easier, meet the requirements of shrinking size, but also save the selection cost and installation cost of downstream manufacturers using separate discrete components, This is an important trend in the development of circuit protection component industry.
The voltage sensitive capacitor element can be used for over-voltage and lightning protection of electronic and electrical appliances, and can also act as a filter capacitor to prevent electromagnetic interference. It is a new functional over-voltage circuit protection element.
(3) New materials and processes
The research and development of advanced materials and technologies is the key to the development of new circuit protection components, so that products can meet the market requirements of small size, high performance, multi-function, modularization, etc.
Based on the optimization and improvement of traditional materials, the introduction of functional materials is a development direction for the industry to develop new products. Developing new processes is another development direction for the industry to develop new products. Surface mount technology, array technology, MLCC (Chip Multilayer Ceramic Capacitor) technology and laser punching forming technology are all newly developed new processes.
(4) Intelligence
The intelligence of circuit protection components includes two meanings: ① the feedback of local circuit protection and overall circuit protection. When a circuit protection component acts, it shall be reported to the console immediately, and the action command shall be issued to the protection components of the overall circuit to achieve the overall coordinated protection function; ② Active protection, that is, protection is no longer limited to safety, but is raised to the point of making the original circuit functions unaffected and improving product reliability. Therefore, active components and chips will be gradually introduced into the field of circuit protection. PCB manufacturers, PCB designers and PCBA manufacturers will explain the technical level and development trend analysis of PCB protection components industry.
然后
联系
电话热线
13410863085Q Q
微信
- 邮箱