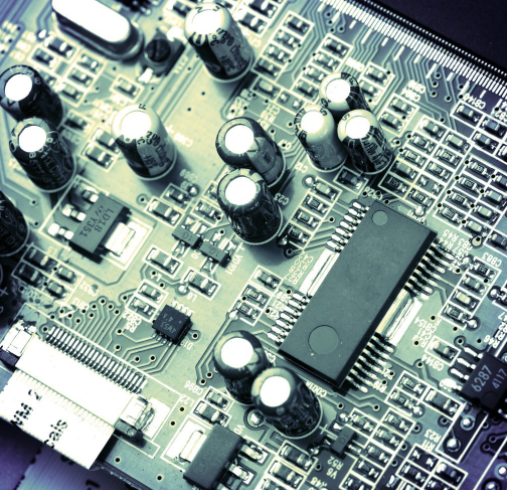
Precautions for PCBA circuit board assembly and production
1. One stop solution for PCB and prototype assembly,
2. DFM inspection
DFM checks all design specifICations of PCB. Will look for any missing, redundant, or possibly problematic features.
3. Incoming material quality control (IQC)
Verify all incoming materials and deal with quality problems before SMT assembly. Our IQC position will check whether the incoming materials meet our strict requirements.
• Model and quantity according to BOM list
• Shape (deformation, broken needle, oxidation, etc.), especially for IC or other complex components
• Use the test stand, multimeter and other tools to sample the incoming materials.
• In case of the above defects or discrepancies, we will return all materials received to the supplier or customer.
4. Machine programming - Gerber/CAD to Centroid/Placement/XY file
After receiving PCB panels and components, the next step is to set up the various machines used in the manufacturing process. Machines such as mounters and AOI (Automatic Optical Inspection) need to create a program, which is best generated from CAD data, but usually cannot be used. Gerber data is almost always available because it is the data needed to manufacture bare PCBs.
5. Solder paste printing
The first machine set up in the SMT production process is the solder paste printer, which is designed to apply solder paste to the appropriate pads on the PCB using templates and scrapers.
6. Component placement
Once the printed PCB is confirmed that the correct amount of solder paste has been applied, it will enter the next part of the manufacturing process, namely component placement. Each component is taken out of the package using a vacuum nozzle or a clamp nozzle, checked by the visual system, and placed at a programmed position at high speed.
7. Pre Reflow Automatic Optical Inspection (AOI)
After the component mounting process, it is important to verify that there are no errors and that all components have been correctly placed before reflow soldering. The best way to do this is to use an AOI machine for checks such as component presence, type/value, and polarity.
8. Reflow soldering
After placing the components on the board, each piece will be sent through our reflow welder. This means that the solder paste needs to be cured to adhere the components to the circuit board. PCB assembly achieves this through a process calLED "reflow".
9. Automatic optical inspection (AOI) after reflow
The last part of the surface mount assembly process is to use the AOI machine again to check the quality of solder joints for errors.
Checking for these errors and dislocations may involve one of several different checking methods. The most common of these inspection methods include:
Manual inspection
Automatic Optical Inspection (AOI)
Automatic X-ray inspection (AXI)
AOI inspection
10. Conformal coating
Some completed printed circuit board assemblies have conformal coatings. This usually depends on the customer's product requirements.
11. Final inspection and functional test
After the welding and conformal coating steps in the PCB assembly process are completed, the final inspection will be performed by our quality assurance team to test the function of the PCB. This check is called a "functional test".
The above is the explanation given by the editor of pcb circuit board company. If you want to know more about PCBA, you can go to our company's home page to learn about it. In addition, our company also sells various circuit boards,
High Frequency Circuit Board and SMT chip are waiting for your presence again.
然后
联系
电话热线
13410863085Q Q
微信
- 邮箱