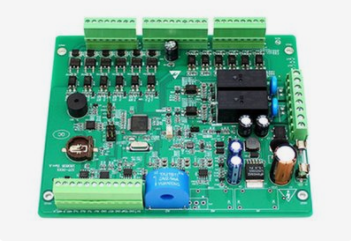
The surface mounting technology (SMT) is being rapidly adopted in the doMEStIC PCB assembly industry, and the domestic STM production lines have reached more than 10000. The important processing equipment in PCBA industry belongs to computer controlLED automatic production equipment. Before the production of a certain Printed Circuit Board (PCB), these automatic processing equipment requires programmers to spend a considerable amount of time preparing data and programming. Most electronic product manufacturers, especially high-tech enterprises with independent development and design capabilities, have the characteristics of newer and faster products, multiple varieties, and SMAll batch production, which requires short production preparation time and long effective production time for processing equipment, In order to meet the requirements of the above production characteristics and shorten the cycle of product research and development to MARKet. How to establish an organic information integration and sharing between CAD design systems and automated production equipment, that is, how to connect the "automation islands" of design automation and production automation on the information flow, and how to remove the "partition" between product design and product manufacturing, is exactly the problem to be solved by the CIMS technology.
In the PCBA industry, the entity of CIMS system is built on the factory computer network and database, which is a paperless manufacturing information system that can improve the quality, capacity and output of circuit assembly. The system can control and monitor the assembly line equipment such as screen printing machine, dispensing machine, mounting machine, plug-in machine and testing equipment. Once a problem occurs, CIMS can feed back the information to the operator or process engineer and point out the exact location of the problem. A relatively complete CIMS system should have the following four elements:
First of all, the system should realize the information integration of CAD and CAM, which is the most basic part of CIMS system. The information integration between automatIC design and automatic manufacturing subsystems can help realize the automatic conversion of CAD data to manufacturing data required by production equipment, that is, automatic programming. This function makes product conversion on the production line quite easy. Once the online products have conversion requirements, they can be automatically reflected in the machine programs, test data and documents through the CIMS system, without the need to program or modify the settings of each device separately, which means that the product conversion that can only be realized in the past few hours or even days can be realized in a few minutes now. This article will focus on how to realize CAD/CAM integration in the following chapters.
Secondly, CIMS shall provide manufacturability analysis and testability analysis tools. Through the manufacturability analysis of CAD files from the design department, the problems violating the mounting rules are fed back to the design system, which can promote the concurrent engineering of the design and manufacturing system and improve the one-time success rate of the design. The testability analysis tool can provide the designer with a complete testability analysis report, so as to reasonably and effectively arrange the testing and inspection resources, and help the design engineer to improve the testability design of the product.
Thirdly, CIMS can provide a reference for production scheduling. The system will maximize production and assembly efficiency by comprehensively analyzing and considering the parameters such as products to be assembled, machine occupancy, and delivery cycle requirements. CIMS can be used for direct short-term scheduling and long-term strategic consideration of plant capacity.
Finally, CIMS should help to balance the production line and optimize the process. A major feature of CIMS is to achieve the optimization of assembly by automatically balancing the loading and sequencing of products, the distribution and mounting of components and the speed of equipment. At the same time, the system should be able to make a reasonable choice between allocating parts to the appropriate machine or using manual assembly.
With the help and promotion of relevant national institutions, China has established many typical application projects of CIMS in the machinery manufacturing industry. Beijing Machine Tool Works and Huazhong University of Science and Technology have successively won the International CIMS Promotion and Application Award, marking that China has entered the international leading level in the research, development and promotion of CIMS. However, few factories in the electronics manufacturing industry actually implement CIMS engineering.
Recently, SMT technology is being rapidly adopted in the domestic PBCA industry. In recent years, tens of thousands of advanced SMT automatic production lines have been introduced, which are basically computer controlled automation equipment, creating favorable conditions for PCBA industry to implement the CIMS project.
In view of the specific situation of China's PCBA industry at present, and the experience and lessons learned from the implementation of CIMS in the machinery industry in recent years, the implementation of CIMS projects in the PCBA industry need not be all inclusive, but the key is the application of CIM. The application of CIM technology in PCBA industry enables enterprises to have the characteristics of multi variety and small batch production, improves the ability of enterprises to quickly respond to market changes, and thus improves the competitiveness of enterprises in global mass production.
From PCB design to the completion of assembly, CIMS provides PCBA manufacturers with powerful tools. Regardless of the variety of components, the type of substrate, the size of PCB, and the different processes used, CIMS can provide a complete solution. At the same time, CIMS is also the link of heterogeneous equipment integration, providing guarantee for rapid product conversion, quality and output improvement
然后
联系
电话热线
13410863085Q Q
微信
- 邮箱