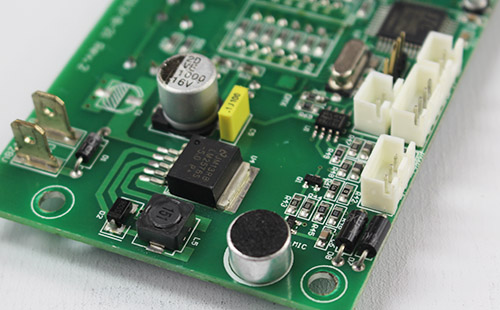
PCB manufacturer explains the feasibility analysis of PCBA welding
The development trend of electronIC information industry requires higher and higher PCBA assembly process. For the reliability and quality of PCBA welding, the existence of residues must be strictly controlLED, and if necessary, these pollutants must be completely removed.
1、 Residues affecting PCBA welding reliability
1. The residue of rosin flux, the flux containing rosin or modified resin, is mainly composed of non-polar rosin resin, a SMAll amount of halide, organic acid and organic solvent carrier.
2. Organic acid flux residues. Organic acid flux (OR) generally means that the solid part of the flux is mainly organic acid flux. The residues of this type of flux are mainly unreacted organic acids, such as oxalic acid, succinic acid, etc., and their metal salts.
3. The white residue is a common pollutant on PCBA, which is generally found after PCBA cleaning or assembly for a period of time. Many aspects of the manufacturing process of PCB see PCBA can cause white residues.
4. Adhesive and oil pollution. In the assembly process of PCBA, yellow glue and red glue are often used to fix components. However, due to the process inspection, the electrical connection parts are often stained. In addition, the residues torn off after the bonding pad protects the tape will seriously affect the electrical connection performance.
2、 PCBA welding reliability test
PCBA welding reliability test mainly includes appearance inspection, ICT test, FCT test, aging test, X-ray inspection, metallographic section analysis, strength (tensile, shear), fatigue life, high temperature and humidity, drop test, random vibration, reliability testing methods, etc. Here are some of them:
1. Visual inspection shows that lead-free and lead welded PCBA solder joints are different from each other in appearance, and will affect the correctness of AOI system. The stripe of PCBA lead-free solder joint is more obvious and rougher than the corresponding lead solder joint, which is caused by the phase transition from liquid to solid. Therefore, this kind of solder joint looks rougher and uneven. In addition, because of the high surface tension of lead-free solder in PCBA processing, it is not as easy to flow as lead solder, and the shape of fillet formed is also different.
2. X-ray inspection showed that the number of defective solder joints in the spherical solder joints of PCBA lead-free soldering increased. The welding density of PCBA lead-free welding is relatively high, which can detect cracks and faulty welding in welding. Copper, tin and silver should belong to "high-density" materials. In order to characterize the excellent welding characteristics, monitor the PCBA assembly process, and conduct the most important structural integrity analysis of PCBA solder joints, it is necessary to recalibrate the X-ray system and have high requirements for testing equipment.
3. Metallographic section analysis, metallographic analysis is one of the important means of metal material test and research. In the reliability analysis of PCBA solder joints, the metallographic structure of the solder joint profile is often taken for observation and analysis, so it is called metallographic section analysis. Metallographic section analysis is a kind of destructive inspection. The sample production cycle is long and the cost is high. It is often used for post weld failure analysis, but it has the advantages of intuition and fact.
In order to ensure the reliability and quality of PCBA welding, it is necessary to carry out necessary analysis and testing.
PCB manufacturers, PCB designers and PCBA processors will explain the feasibility analysis of PCBA welding.
然后
联系
电话热线
13410863085Q Q
微信
- 邮箱