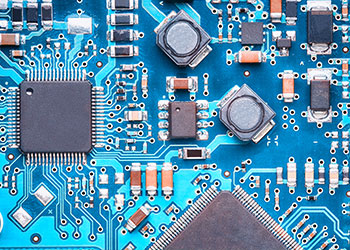
SMT processing lead-free welding and PCBA processing
The introduction of lead-free chip assembly has always been a challenge for the first assembly, because PCB processing requires rework PCBA maintenance in lead-free environment has high cost, detaiLED quality information, time and repeatability problems, but due to lead-free requirements, all these problems need attention Because lead-free process requires:
1. Train operators to perform lead-free assembly, maintenance and inspection, and evaluate time and cost.
2. Lead free solder is more expensive than traditional solder, such as lead-free wire, electrode and core solder.
3. The processing temperature of lead-free components (about 30-35 ℃) requires higher accuracy and precision.
4. The lead-free process also needs to study and plan the SMT processing plant to establish a correct PCBA rework process.
PCBA rework
circuit board
Jingbang ElectronICs believes that the first step for PCB component rework is to train and guide scientific and technical personnel, and develop the profile according to the characteristics of lead-free process The rework standard is defined to determine whether standard solder or lead-free solder is required. The process starts with the same pipe. The required steps include:
Define and execute accurate thermal profiles
2. The faulty component must be removed
3. Clean all rust or solder residues on site and prepare new parts
4. Replace components with new solder and flux and reflow
5. Thorough inspection and rework
In a lead-free environment, accurate and reliable rework is more difficult because PCBA and the components closest to the parts to be repaired must withstand multiple high temperature cycles. In order to protect the stability of the circuit board, the preheating temperature should be set not higher than the glass transition temperature of the PCB data.
The subsequent steps involved in the rework process depend on whether there is a lead-free requirement. The difference between standard and lead-free brings many challenges, which can only be solved by introducing new or changed processes, including stricter and more accurate thermal profiles and extremely high precision in the whole PCBA rework process. This will avoid many costly problems caused by different heat distributions.
Analysis of SMT lead-free welding and repair
Why to preheat before PCBA processing
The importance of temperature distribution has been widely understood in the PCB processing and welding environment of mass production. The slow heating and preheating phases help to start the flux, prevent thermal shock, and improve the quality of solder joints during smt placement. However, when it comes to rework, prototyping or PCBA first article proofing, it is easy to forget the importance of the preheating phase, which may lead to equipment damage, even if there is no damage. So why is such an important step often forgotten in the actual operation of SMT processing plant?
Reflow soldering preheating zone
What was the previous preheating for PCBA welding?
When technicians and practitioners hear the words "temperature curve" or "temperature curve", they will think of smt reflow. The four main temperature control zones can be easily seen along the huge length of the weld zone, which will eventually produce a perfect weld joint, hopefully. Carefully control and improve each stage through the experience and repeated tests of scientific and technical personnel. Each stage plays a role in improving the quality of solder joints and reducing defects. But other industrial welding machines may not have such fine temperature control. But what they have in common is the warm-up phase.
然后
联系
电话热线
13410863085Q Q
微信
- 邮箱