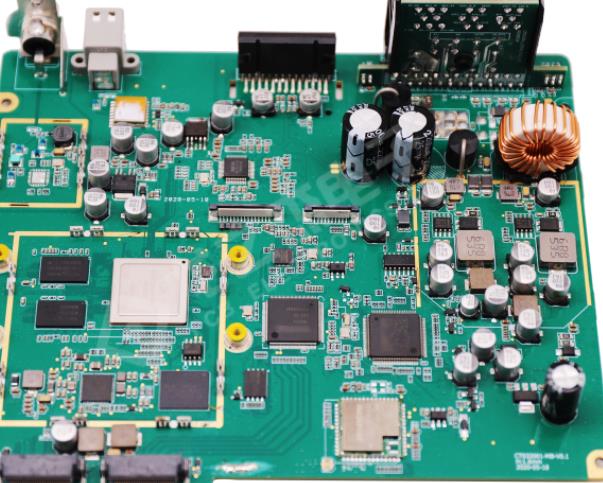
Strength and use of SMT mounter
Power chip mounter is reflected
Mounting speed refers to the installation time of each component within a certain range Chip devICes are currently instalLED on high-speed computers Speed: 0.06-0.03s: multi-functional machines are usually medium speed machines The installation speed of QFP is 1-2 seconds, and the placement speed of chip modules is 0.3 to 0.6 seconds. The current multi-function machine can also reach 0.2 seconds. If it is used for high-capacity SMT placement, the higher the placement speed, the higher the delivery rate
1. Installation speed
Installation speed refers to the installation time of each component within a certain range. The rack is fixed. Chip devices are currently installed on high-speed computers. Speed: 0.06-0.03s: multi-functional machines are usually medium speed machines. The installation speed of QFP is 1 to 2s, and the placement speed of chip components is 0.3 to 0.6s. The current multi-function machine can also reach within 0.2s. If the patch is placed on a large scale, the higher the placement speed, the higher the delivery rate.
According to the IPC9850 standard (the acceptance standard of the placement machine), the placement speed is expressed in CPH, that is, 200 mm per hour × The number of parts placed in the 200mm patch area. Large components, such as chip components and QFPs, are installed at different speeds. For example, the installation speed of chip components is greater than or equal to 12000 cph, while the installation speed of QFP is greater than or equal to 1800 cph.
Circuit board
2. Installation angle
The installation angle is usually 0 ° to 360 °, and the resolution is 0.1 ° to 0.001 °.
3. Component absorption
The component suction rate refers to the ability to pick up and place accurately. In%, the bigger the better. For example, if the component suction rate is 99.9%, it is allowed to place less than 1 component and 1000 components. In SMT wafer processing, the key to test product quality is to reduce the throw rate.
Fourth, installation area
The placement area depends on the transfer track of the placement machine and the movement range of the placement head. In general, the minimum PCB size is 50 mmx50 mm and the maximum PCB size should be greater than 250 mmx30 mm. The maximum installation area of machines from different manufacturers is different. The maximum PCB size of the same type of machine is generally divided into three specifications: large, medium and SMAll.
Purpose of the SMT machine
The mounter is also called "surface mounting system" and "mounter". Generally, in the production line, the placement machine is a device equipped with a glue distributor or screen printer, and then moves the tip to accurately place the surface mounted components on the PCB pad.
Here are some types of mounters
Class I, smt mounter
The SMT is the fourth generation of electronic assembly technology, which has the advantages of high component installation density, easy automation, improved production efficiency and reduced cost. SMT production line includes three processes: screen printing, component placement and reflow soldering. The placement of SMC/SMD is an important part of the whole surface mounting process.
Class II: LED chip mounter
LED chip mounter is a SMT chip mounter specially designed for LED industry, which is used to realize large-scale LED Circuit board assembly. It uses the principle of guide rail or linear motor to control the driving head, and must be equipped with professional spunbonded nozzle head, so as to eliminate production defects such as adhesion and throwing as much as possible during placement, and ensure its stability and service life.
Category 3, automatic placement machine
As the name implies, the automatic placement machine is a fully automatic placement machine, which does not require manual positioning.
Automatic placement machine is used to realize high-speed, high-precision and automatic placement of components. It is the key and complex equipment in the whole SMT production.
What does the mounter do? How does the mounter work?
The first step is to draw a picture. Use the picture of PCB to make an image board, print it on the circuit board, then etch it to make the basic circuit of the circuit board come out, and then punch and print the wire mesh.
The second step is to compile the location program on the mounter The positioning program is based on the MARK points drawn on the circuit board in advance, and the flux is applied after programming That is, all the places that need to be welded on the circuit board are covered with the grid board made for the circuit board The holes make on the stencil can be coated with flux (tin paste) on the PCB
然后
联系
电话热线
13410863085Q Q
微信
- 邮箱