鑫景福致力于满足“快速服务,零缺陷,辅助研发”PCBA订购单需求。
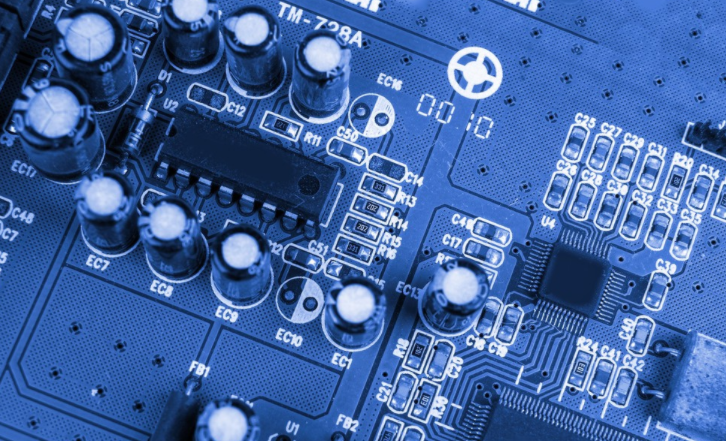
SMT data processing standards and quality inspection
– When handling plants with SMT patches, excellent material handling guidelines and methods must be available
(1) Material handling
â â 1. SMT data processing guide.
First in, first out: materials that are received first are issued first.
Appropriate quantity when ordering: master the time and quantity of each step in the warehouse.
Accounts are consistent: daily records of bills and items must be consistent.
Daily inventory: warehouse employees need to check the materials they are responsible for every day to maintain the consistency of daily accounts.
E Management: realize systematIC and paperless management.
Kanban processing: List material information in the form of tables, such as material number, quantity and storage date, and make Kanban and stand at the end of the shelf.
Storage location management: different materials are placed in different areas of the shelf, that is, the positioning of storage areas, shelves and materials.
– FIFO processing: the advanced data shall be delivered and put into use first, and the feeding month shall be MARKed with different colors.
Area management: different areas are represented by different colors as the identification of different data.
Handling of defective products: the quality control personnel shall confirm the defective products, stick, block and place unqualified labels, and return to the defective product warehouse after handling.
-MSD treatment: due to the moisture absorption of MSD components, it is necessary to control the exposure time to the air according to its sensitivity level, and fill in the "humidity sensitive component control label"
Purpose and Effect of Quality Inspection in SMT patch processing
1. Quality inspection intention awareness in SMT patch processing.
Find and eliminate the faults in the SMT installation process, complete good process control, and improve the yield of products.
â â 2. Understand the quality inspection effect in SMT chip processing.
Find defects as early as possible to prevent defective products from flowing into the next process and reduce maintenance costs; Timely find and deal with deficiencies to prevent waste products and reduce production costs.
â â 3. KnowLEDge of SMT chip processing quality detection technology.
-Visual inspection: directly investigate and check the quality of SMT products with the naked eye. In the production process of SMT practice, there are visual inspection procedures after printing paste, patch, reflow soldering, wave soldering and online inspection, that is, printing visual inspection, furnace comparison visual inspection, installation visual inspection and quality inspection.
It is characterized by low cost and viewing effect related to PCB installation density. In the case of low-density installation, the reliability, accuracy and continuity of observation vary from person to person. In the case of high-density installation, the reliability, accuracy and continuity of observation are usually reduced, and the observation time is correspondingly longer. Long
AOI inspection: Automatic optical inspection (AOI) uses active optical equipment for inspection, which is an alternative method of visual inspection. AOI inspection process is usually provided after printing paste and reflow soldering.
It is characterized by dense installation of detection system and PCB, high detection speed, high precision and high repeatability The bad results of the inspection are directly marked on the PCB with ink, or marked with graphic errors on the operation display
ICT detection: On line tester (ICT), that is, use the line tester for line fault diagnosis. ICT inspection process is usually provided after PCB assembly.
It is characterized by strong ability to diagnose faults. Welding defects such as bridging, empty welding, faulty welding and broken wire can directly show the position of the welding spot; It can also detect welding defects caused by component defects.
– When handling plants with SMT patches, excellent material handling guidelines and methods must be available
(1) Material handling
â â 1. SMT data processing guide.
First in, first out: materials that are received first are issued first.
Appropriate quantity when ordering: master the time and quantity of each step in the warehouse.
Accounts are consistent: daily records of bills and items must be consistent.
Daily inventory: warehouse employees need to check the materials they are responsible for every day to maintain the consistency of daily accounts.
E Management: realize systematIC and paperless management.
Kanban processing: List material information in the form of tables, such as material number, quantity and storage date, and make Kanban and stand at the end of the shelf.
Storage location management: different materials are placed in different areas of the shelf, that is, the positioning of storage areas, shelves and materials.
– FIFO processing: the advanced data shall be delivered and put into use first, and the feeding month shall be MARKed with different colors.
Area management: different areas are represented by different colors as the identification of different data.
Handling of defective products: the quality control personnel shall confirm the defective products, stick, block and place unqualified labels, and return to the defective product warehouse after handling.
-MSD treatment: due to the moisture absorption of MSD components, it is necessary to control the exposure time to the air according to its sensitivity level, and fill in the "humidity sensitive component control label"
Purpose and Effect of Quality Inspection in SMT patch processing
1. Quality inspection intention awareness in SMT patch processing.
Find and eliminate the faults in the SMT installation process, complete good process control, and improve the yield of products.
â â 2. Understand the quality inspection effect in SMT chip processing.
Find defects as early as possible to prevent defective products from flowing into the next process and reduce maintenance costs; Timely find and deal with deficiencies to prevent waste products and reduce production costs.
â â 3. KnowLEDge of SMT chip processing quality detection technology.
-Visual inspection: directly investigate and check the quality of SMT products with the naked eye. In the production process of SMT practice, there are visual inspection procedures after printing paste, patch, reflow soldering, wave soldering and online inspection, that is, printing visual inspection, furnace comparison visual inspection, installation visual inspection and quality inspection.
It is characterized by low cost and viewing effect related to PCB installation density. In the case of low-density installation, the reliability, accuracy and continuity of observation vary from person to person. In the case of high-density installation, the reliability, accuracy and continuity of observation are usually reduced, and the observation time is correspondingly longer. Long
AOI inspection: Automatic optical inspection (AOI) uses active optical equipment for inspection, which is an alternative method of visual inspection. AOI inspection process is usually provided after printing paste and reflow soldering.
It is characterized by dense installation of detection system and PCB, high detection speed, high precision and high repeatability The bad results of the inspection are directly marked on the PCB with ink, or marked with graphic errors on the operation display
ICT detection: On line tester (ICT), that is, use the line tester for line fault diagnosis. ICT inspection process is usually provided after PCB assembly.
It is characterized by strong ability to diagnose faults. Welding defects such as bridging, empty welding, faulty welding and broken wire can directly show the position of the welding spot; It can also detect welding defects caused by component defects.
点击
然后
联系
然后
联系
电话热线
13410863085Q Q
微信
- 邮箱