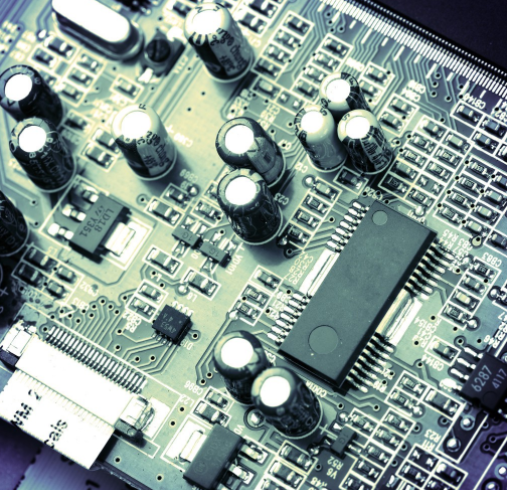
SignifICant cost losses and difficulties in SMT patches and solutions
SMT patch for major cost loss
Recently, the consumption rate of parts has increased, and customer satisfaction has also had a corresponding impact. This is why we are now worried about SMT's significant cost loss. Now that we have found the problem, we will analyze the customer service attitude of other factors except the shortage of manpower. I hope that if you have SIMilar problems on the production line, we can help you!
1. High throwing rate
1. The machine lacks maintenance and repair. Due to the dirt on the nozzle surface, the nozzle cannot identify data or has poor identification ability.
2. Insufficient air compressor pressure or insufficient storage capacity of the vacuum compressor pump of the placement machine lead to material throwing during the placement process.
3. The insufficient crimping force of the braided belt of the feeder causes the plastic bag to curl abnormally during the feeding process.
4. The placement program was edited incorrectly, and the PCB MARKing coordinates were set incorrectly, resulting in incorrect feeding position.
5. The solder paste printing position is offset due to deviation during solder paste printing, and the data cannot be soldered.
6. The flatness of the workbench and the supporting platform is not in the same horizontal plane or the commissioning equipment has errors.
The high discard rate proves that the patch has a great loss. It needs to be refilLED, refilled and refilled, and any of them will consume costs.
Especially for the core BGA or IC, because it belongs to Class A data, the loss and spare parts should be strictly controlled, or there are few spare parts. If it is due to the manufacturer's own reasons, the customer's delivery date may not keep up with the corresponding compensation.
Difficulties and Solutions in SMT chip processing
First, high reliability and strong anti vibration capability
SMT processing adopts chip components, which have high reliability, SMAll size and light weight. In addition, it has strong anti vibration ability Adopt automatic production, high reliability Generally, the ratio of defective solder joints is less than 10 million and more than 1 million, which is lower than wave soldering technology In order to ensure the low solder joint defect rate of electronic products or components, nearly 90% of electronic products now use SMT technology
Second, electronic products are small in size and high in assembly density
The volume of the patch assembly is only about 1/10 of the traditional insertion assembly, and the weight is only 10% of the traditional insertion assembly. In general, SMT can reduce the volume of electronic products by 40% - 60%, the quality by 60% - 80%, and the area and weight by a large margin. The surface mount machining grid of the assembled parts is currently 1.27mm to 0.63mm, and the single grid is 0.5mm. The installation of hole process components can make the package density higher.
Third, high frequency characteristics and reliable performance
Because the chip modules are firmly connected, the devices usually have no leads or short leads, which reduces the impact of parasitic inductance and capacitance, improves the high-frequency characteristics of the circuit, and reduces electromagnetic interference and radio frequency interference. The circuit frequency designed by SMC and SMD can reach 3GHz, while the circuit designed by chip is only 500MHz, which can shorten the transmission delay time. It can be used in circuits with clock frequency higher than 16MHz. With MCM technology, the clock frequency of computer workstation can reach 100MHz, and the additional power consumption caused by parasitic reaction can be reduced by 2-3 tiMES.
Fourth, improve production efficiency and realize automatic production
At present, if the perforated printed circuit board is to be fully automated, the area of the original printed circuit board needs to be expanded by 40% so that the insertion head can automatically insert components, otherwise the space gap is insufficient and the parts will be damaged. The automatic placement machine (SM421/SM411) uses a vacuum nozzle to suction and discharge components. The vacuum nozzle is smaller than the component, but the installation density is increased. In fact, in the production of automatic placement machine, small parts and small spacing QFP units are used to realize the automation of the whole production line.
Fifth, reduce costs and expenses
(1) The area of the printed board is reduced to 1/12 of the through hole process. If CSP is used for installation, the area will be greatly reduced;
(2) Reduce the number of holes drilled on the printed circuit board to save maintenance costs;
(3) The frequency characteristic of the circuit is improved, and the circuit debugging cost is reduced;
(4) Due to the small size and light weight of the chip module, the packaging, transportation and storage costs are reduced;
The above is the explanation given by the editor of PCB circuit board company.
If you want to know more about PCBA, you can go to our company's home page to learn about it.
In addition, our company also sells various circuit boards,
High Frequency Circuit Board and SMT chip are waiting for your presence again.
然后
联系
电话热线
13410863085Q Q
微信
- 邮箱