鑫景福致力于满足“快速服务,零缺陷,辅助研发”PCBA订购单需求。
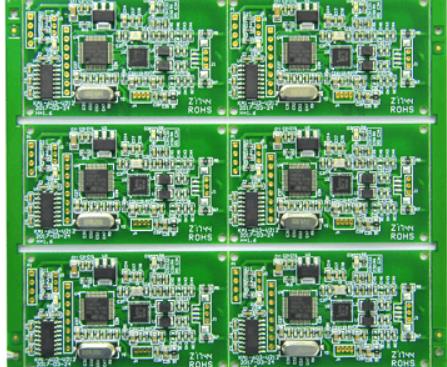
ApplICation of CIMS in SMT Chip Processing
For many electronic companies using SMT equipment, the introduction of computer integrated manufacturing system cims into SMT chip processing production has improved product quality and the effective utilization of equipment, and greatly shortened the product design cycle and time to MARKet The economic benefits brought by CIMS to enterprises are obvious It is believed that the application of cims in enterprises SMT chip processing will become more and more widespread in the near future
Application of cims in enterprises SMT chip processing and production
Many equipment in SMT chip processing production line are computer controlLED automatic processing equipment, which makes it possible for computer aided manufacturing to form a CAD/CAM integrated system.
Handle CAD design files, improve assembly accuracy, and greatly reduce failure rate.
In the 1970s, Dr Joseph Harrington first proposed the concept of cim (computer integrated manufacturing). Its connotation is to integrate various scientific and technological systems related to manufacturing in enterprises with the help of computers, so as to improve enterprises' ability to adapt to market competition However, cims, a system based on the concept of CIM, began to be valued and implemented on a large scale in the mid 1980s Cims is based on database, and transmits the data in the design environment to various automatic processing equipment through computer network, and can effectively control and supervise these automatic equipment The connection between the production department and the design department is established by using cims, which can be realized by cad integration As mentioned earlier, many of the equipment in SMT chip processing production lines are computer controlled automatic processing equipment, which provides a completely possible/cam integrated system for computer-aided manufacturing to form cad In fact, most of the data required for the programming of processing equipment in the SMT SMT production line can be obtained from the relevant data files of the CAD system For example, coordinate position, angle, physical parameters, electrical parameters, etc PCBA upper assembly These data voluMES are very large, and different processing equipment need some characteristic data For example, placement machine, distributor and online test equipment all need the coordinate position of components on PCB Therefore, the idea and technology of CIMS are used to establish a cad system/cad and cam integrated system, directly select, organize/transform and optimize the corresponding characteristic data in the cad system data file, and program the data format requirements according to the specific equipment or n format. The/c command needs to be transmitted to the control computer of the processing equipment through the computer network and interface communication software, so as to directly call or directly drive the numerical control processing equipment during the programming But also because of the direct
Due to the characteristics of the production of the SMT industry, it is more appropriate to use just in time system for on-site management The combination of just in time and total quality control can reduce waste and improve product quality
For many electronic companies using SMT equipment, the introduction of computer integrated manufacturing system cims into SMT chip processing production has improved product quality and the effective utilization of equipment, and greatly shortened the product design cycle and time to MARKet The economic benefits brought by CIMS to enterprises are obvious It is believed that the application of cims in enterprises SMT chip processing will become more and more widespread in the near future
Application of cims in enterprises SMT chip processing and production
Many equipment in SMT chip processing production line are computer controlLED automatic processing equipment, which makes it possible for computer aided manufacturing to form a CAD/CAM integrated system.
Handle CAD design files, improve assembly accuracy, and greatly reduce failure rate.
In the 1970s, Dr Joseph Harrington first proposed the concept of cim (computer integrated manufacturing). Its connotation is to integrate various scientific and technological systems related to manufacturing in enterprises with the help of computers, so as to improve enterprises' ability to adapt to market competition However, cims, a system based on the concept of CIM, began to be valued and implemented on a large scale in the mid 1980s Cims is based on database, and transmits the data in the design environment to various automatic processing equipment through computer network, and can effectively control and supervise these automatic equipment The connection between the production department and the design department is established by using cims, which can be realized by cad integration As mentioned earlier, many of the equipment in SMT chip processing production lines are computer controlled automatic processing equipment, which provides a completely possible/cam integrated system for computer-aided manufacturing to form cad In fact, most of the data required for the programming of processing equipment in the SMT SMT production line can be obtained from the relevant data files of the CAD system For example, coordinate position, angle, physical parameters, electrical parameters, etc PCBA upper assembly These data voluMES are very large, and different processing equipment need some characteristic data For example, placement machine, distributor and online test equipment all need the coordinate position of components on PCB Therefore, the idea and technology of CIMS are used to establish a cad system/cad and cam integrated system, directly select, organize/transform and optimize the corresponding characteristic data in the cad system data file, and program the data format requirements according to the specific equipment or n format. The/c command needs to be transmitted to the control computer of the processing equipment through the computer network and interface communication software, so as to directly call or directly drive the numerical control processing equipment during the programming But also because of the direct
Due to the characteristics of the production of the SMT industry, it is more appropriate to use just in time system for on-site management The combination of just in time and total quality control can reduce waste and improve product quality
点击
然后
联系
然后
联系
电话热线
13410863085Q Q
微信
- 邮箱