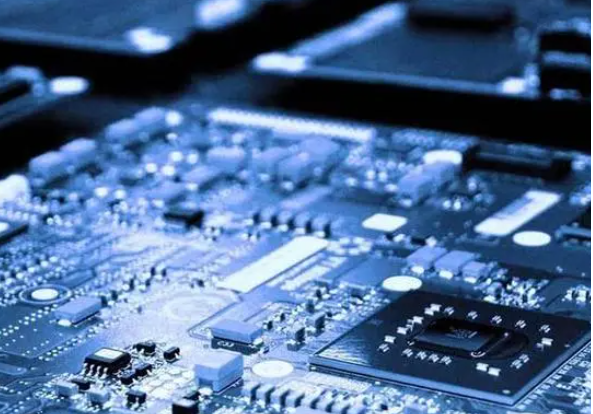
The thermal, mechanICal, and electrical behavior of each PCB depends on the material properties of the PCB substrate, conductor, and component materials. Among these different materials, people can control the behavior of the board to the greatest extent by selecting the correct PCB substrate material. The performance of PCB materials, especially the performance of resins and laminates, will determine how your circuit board reacts to mechanical, thermal and electrical stimuli.
When you need to select PCB substrate materials, which PCB material characteristics are most important for your PCB? The answer depends on the application of PCB and the environment where PCB will be deployed. When selecting prepreg and laminate materials for the next PCB, you should consider the following important material characteristics for your application reference.
Your choice of substrate is no longer limited to FR4, but you should not easily choose PCB laminate. You should first understand how different material properties affect your PCB, and then select a laminate that meets your operational requirements. Don't just listen to the MARKeting speech of the laminate manufacturer; Take the time to understand the material properties of each substrate and how they affect your PCB.
You can find some data about PCB material performance on the Internet, but you'd better consult the manufacturer, especially for special laminated materials, because no two laminates are identical, and no two laminates are identical. More exotic materials such as ceramics and metal core PCBs have a series of unique material characteristics.
The important PCB material properties that all designers should know are divided into four aspects: electrical, structural, mechanical and thermal properties.
electrical properties
All important electrical properties that need to be considered in today's PCB substrate materials are reflected in the dielectric constant.
Dielectric constant
This is the main electrical characteristic to be considered when PCB is designed for high speed/high frequency PCB lamination. Dielectric constant is a complex quantity, which is a function of frequency and causes dispersion in the following forms in PCB substrate:
Velocity dispersion: because the dielectric constant is a function of frequency, different frequencies will experience different loss levels and travel at different speeds.
Loss dispersion: the attenuation experienced by the signal is also a function of frequency. The SIMple dispersion model shows that the loss increases with the increase of frequency, but this is not strictly correct. There may be a complex relationship between the loss of some laminates and the spectrum.
These two effects contribute to the degree of distortion experienced by the signal during propagation. For analog signals operating on a very narrow bandwidth or a single frequency, dispersion does not matter. However, it is extremely important in digital signals, and is one of the main challenges in high-speed digital signal modeling and interconnection design.
Structural properties
The structure of PCB and its substrate will also affect the mechanical, thermal and electrical properties of the board. These characteristics are mainly reflected in two ways: glass weaving and copper conductor roughness.
Glass woven style
The glass braided pattern will leave gaps on the PCB substrate, which is related to the resin content on the board. The average dielectric constant of the substrate can be determined by combining the volume ratio of glass and impregnated resin. In addition, the gap in the glass braiding pattern will produce the so-calLED fiber braiding effect, in which the substrate dielectric constant varying along the interconnects will produce deflection, resonance and loss. These effects become very prominent at~50GHz or higher frequencies, which will affect radar signals, kilomega bit Ethernet and typical LVDSSerDes channel signals.
Copper roughness
Although this is actually a structural characteristic of printed copper conductors, it contributes to the electrical impedance of interconnects. The surface roughness of the conductor effectively increases its skin effect resistance at high frequencies, resulting in the induction loss caused by induced eddy currents during signal propagation. Copper etching, copper deposition method and the surface of prepreg will affect the surface roughness to some extent.
Thermal performance
When selecting substrate materials, the thermal properties of PCB laminates and substrates need to be divided into two groups.
Thermal conductivity and specific heat
The heat required to raise the temperature of the plate by one degree is quantified by the specific heat of the substrate, and the heat transmitted through the substrate per unit time is quantified by the thermal conductivity. The performance of these PCB materials together determines the final temperature when the PCB reaches thermal balance with the environment during operation. If you deploy your circuit board in an environment where you need to quickly dissipate heat to a large radiator or chassis, you should use a substrate with a higher thermal conductivity.
These two PCB material properties are also relevant. All materials have a certain coefficient of thermal expansion (CTE), which is exactly the amount of anisotropy in the PCB substrate (that is, the expansion rate is different in different directions). Once the temperature of the circuit board exceeds the glass transition temperature (Tg), the CTE value will suddenly increase. Ideally, the CTE value should be as low as possible within the required temperature range, while the Tg value should be as high as possible. Tg~130 ° C of the cheapest FR4 substrate, but most manufacturers provide the choice of Tg~170 ° C fiber core and laminate.
The thermal properties listed above are also related to the mechanical stability of the conductors on the PCB substrate. In particular, CTE miSMAtch creates known reliability problems in high aspect ratio through-hole and blind/buried through-hole, where through-hole is prone to fracture due to mechanical stress caused by volume expansion. Therefore, high Tg materials and other special laminates have been developed, and design engineers engaged in HDI PCB design may consider using these alternative materials.
然后
联系
电话热线
13410863085Q Q
微信
- 邮箱