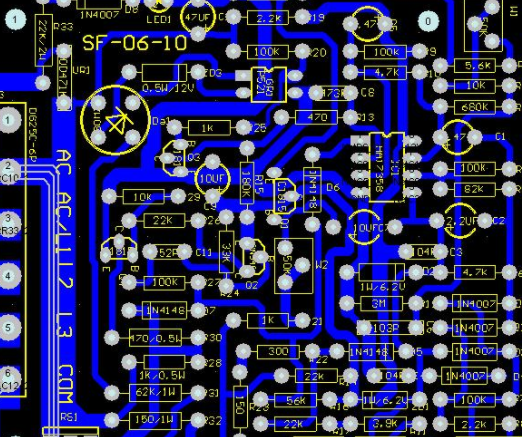
The Influence of Integrated Passive components on the Development of PCB Technology
The integrated passive component technology can integrate various electronIC functions from the printed circuit board technology, and has the advantages of miniaturization and improving system performance, which can replace the large discrete passive components This paper mainly introduces the development of integrated passive component technology, and uses IPD film technology to realize the processing of capacitors, resistors and inductors, and discusses the impact of intellectual property rights on the development of enterprises PCB technology
1 Introduction
With the development of electronic technology, the integration of active electronIC components has been greatly improved and the demand for passive components and active components has increased significantly since the transistor was prepared from the micro process to the nano process The development trend of electronic product MARKet is thin and short Therefore, the improvement of transistor process capability greatly increases the number of active components in the same volume In addition to supporting a substantial increase in the number of passive components, more space is required to place these passive components Therefore, the size of overall packaging equipment will inevitably increase, which is quite different from the development trend of the market From the cost perspective, the total cost is proportional to the number of passive components Therefore, under the prEMIse of using a large number of passive components, how to reduce the cost and space of passive components, and even improve the efficiency of passive components, is an important issue at present One of the theMES IPD (Integrated Passive Devices) technology can integrate a variety of electronic functions, such as sensors, RF transceivers, MEMS, power amplifiers, power management units and digital processors, In order to provide compact integrated passive components, IPD products have the advantages of miniaturization and improved system performance Therefore, if the size and weight of the whole product are reduced, or if the functions are added to the existing product volume, the integrated passive component technology can play a great role In the past few years, IPD technology has become an important implementation of system in package (SiP); At the same time, IPD technology can be introduced to deal with PCB boards. Through the comprehensive advantages of IPD technology, packaging technology and PCB technology can be bridged IPD integrated passive component technology has developed from the initial commercial technology to the present to replace discrete passive components, and has steadily increased/electromagnetic interference driven by ESD and other industries RF, high brightness LED, and digital hybrid circuit
PCB board
2. Introduction of thin film IPD technology
IPD technology can be divided into thick film process and thin film process according to the process technology. The thick film process technology includes low temperature co fired ceramic LTCC (Low Temperature Co fired Ceramics) technology using ceramic as abstract and PCB based on HDI high density interconnection PCB embedded passive components (Embedded Passives) technology; And thin film IPD technology, which uses commonly used transistor technology to manufacture circuits, capacitors, resistors and inductors LTCC Technology uses ceramic materials as substrates, embeds passive components (such as capacitors and resistors) into ceramic substrates, and forms complete ceramic components through sintering, which can greatly reduce the space of components However, with the increase of the number of layers, the manufacturing difficulty and cost increase Therefore, LTCC components are mainly used for circuits with specific functions; HDI embedded component technology is usually used in this PCB digital system, which is only applicable to distributed welding capacitors and medium and low precision Resistors, as the size of components shrinks, SMT devices are not easy to handle too SMAll components Although the technology of embedded printed circuit board is mature, the product characteristics are poor, and the tolerance cannot be accurately grasped, because the components are embedded in the Multilayer board, it is difficult to replace or repair and adjust after problems occur Compared with LTCC technology and PCB embedded component technology, thin film IPD technology of integrated circuit has high precision and repeatability The advantages of small size, high reliability and low cost will become the mainstream of IPD in the future This paper will mainly introduce thin film IPD technology
3. Development status of thin film integrated passive component technology
Thin film IPD technology uses thin film processes such as exposure development coating decoration - etc The process can produce various resistors, capacitors, and inductive components, as well as low inductance grounding plates and transmission lines for connecting passive components The film structure is suitable for manufacturing on the same carrier substrate data. The process must not only meet the required number of module efficiency and precision, but also be uncomplicated. and the number of masks (usually 6 to 10) is required In order to compete with SMT discrete components in terms of area and cost, each passive component usually occupies less than 1 mm2 According to the existing IPD structure, the development manufacturers are introduced as follows:
(1) Telephus
The IPD developed by Telephus uses a thick copper process, which can improve the efficiency of lines with only passive components Reduce cost and size, such as screening programs and distributors, thick copper metal layers (10 mm) and silicon insulating surfaces enable wireless communication systems and integrated RF modules have high performance. Low k data is applicable to reduce parasitic capacitance between metal layers
(2) IMEC
IMEC's thin film technology also uses electroplated copper as the connection line, BCB as the dielectric layer, and Ni/gold layer as the metal of the final connection surface, and up to 4 layers of metal are used
(3) Dai Nippon
The IPD resistors developed by Dai Nippon are mainly Ti/Cr Company, capacitors form Ta2O5 through anodic oxidation. Inductors are designed with microstrip lines and SPIral inductors
(4) Sychip
The IPD developed by SyChip uses TaSi as the resistance material. The dielectric material of the capacitor is Si3N4, the upper electrode is aluminum, and the lower electrode is TaSi. The inductor and circuit data are made of aluminum Some companies are developing IPDs using MEMS processes
4. Structure and process of thin film integrated passive component technology
The difference between the thin film process and the thick film process lies in the thickness of the resulting film. Generally, the thickness of the so-called thick film is greater than 5 mm~10 mm, while the thickness of the thin film process is about 0.01 m~1 m If the film process is used to form resistors, capacitors and inductors at the same time, different processes and materials are required to manufacture them The application of thin film technology in the manufacturing process of semiconductor integrated circuits is relatively mature Therefore, when integrating the process, only pay attention to the compatibility of data between different components, and then conduct process design In general, due to different product applications, thin film IPD integrated passive components can be fabricated on different substrates Substrates can be selected from silicon wafers, alumina ceramic substrates, and glass substrates Thin film IPD integrated passive component technology can integrate thin film resistors, capacitors and inductors. its process technology has developed, including photolithographic processing technology, thin film deposition processing technology, etching processing technology, electroplating processing technology, and chemical plating processing technology In addition to the integration of passive components, the process of active components can also be combined on the silicon chip to integrate passive components and active component circuits to achieve multi-function requirements
(1) Thin film resistor processing
Thin film resisters are usually fabricated by sputtering process. Resistance data are plated on the insulating substrate, and then photoresist and etching technology are used to process the resistance pattern to obtain the design resistance value In the application of data, it is necessary to consider the TCR of resistance data, that is, the resistance change rate at different temperatures The formation methods of thin film resistors include vacuum evaporation, sputtering, thermal decomposition and electroplating. Common resistance data include three single component metals, alloys and cermets
(2) Film capacitor processing
Because MIS (metal insulator semiconductor structure) film capacitors use semiconductors as the bottom electrode, capacitors themselves have parasitic resistance, which will reduce the resonant frequency of components and cannot be applied to frequencies above 200 MHz The MIM capacitor can reduce the parasitic resistance value, thus increasing the resonant frequency of the module. The resonant frequency depends on the natural frequency of the dielectric material Like film resistors, film capacitors need to take into account the rate of change in capacitance, as well as the dielectric constant In addition, it is necessary to pay attention to the surface roughness Ra<0. The substrate is 3mm If the roughness Ra value exceeds the specified range, the dielectric layer is easily penetrated by the slope lock of the bottom electrode, resulting in short circuit
(3) Thin-film inductor processing
The thin-film inductor process is SIMilar to the resistor process, but the main design consideration is how to reduce its parasitic capacitance and improve the quality factor (Q) of the component. Due to the ratio of inductance characteristics, considering the need to reduce its DC impedance to improve the Q value, the film thickness of the inductor wire must be between 5mm and 10mm, and this inductance wire is usually formed in the electroplating process to meet the requirements The surface roughness of the substrate will affect the characteristics of the thin film inductor, especially at high frequencies. Excessive surface roughness is likely to lead to new noise and lower high-frequency characteristics. Therefore, the selection, manufacturing and processing of the substrate will affect the efficiency of the entire thin film element
然后
联系
电话热线
13410863085Q Q
微信
- 邮箱