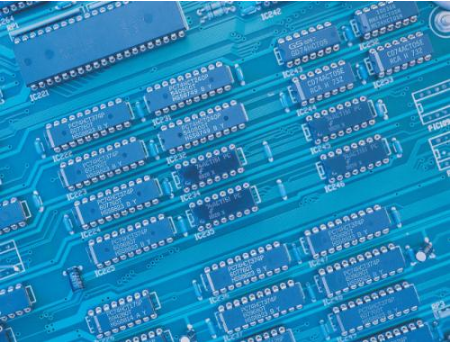
PCB design has entered the era of high-speed PCB design. PCB is no longer just a carrier to complete the interconnection function, but an extremely important component in all electronIC products. From the perspective of engineering realization of high-performance PCB design, this paper comprehensively analyzes all aspects of high-performance PCB design in IT industry. To achieve high-performance PCB design, we must first have a high-quality PCB design team.
1、 Suggestions on the formation of PCB design team
Since PCB design entered the high-speed era, the practice that hardware engineers are solely responsible for schematic and PCB design has gone forever, and full-time PCB engineers have emerged as the times require.
A mature large and medium-sized PCB design team should include the following types of work:
Packaging library engineer: full-time library building, familiar with the process capabilities and technical parameters of today's mainstream board manufacturers and patch manufacturers, combined with the actual products of the company, and based on this, complete the PCB packaging library building work under the current high-speed and high-density conditions.
PCB design engineer: designers must have extensive peripheral
CB stack design, impedance design, signal integrity, EMC, etc., comprehensively consider the requirements of modern PCB design, and complete the PCB layout and wiring.
SI engineer: Uncover the "hidden schematic diagram" hidden in the PCB transmission line, and face the problems of reflection, crosstalk and timing in the high-speed era. Through pre and post SIMulation, the signal quality is ensured, the one-time success rate of the product is improved, and the stable and reliable operation of PCB is ensured.
EMC engineer: as the source of EMC design, responsible for board level EMC design related to circuits, devices and PCB. Reduce its own external radiation and improve its ability to resist external interference.
Thermal design engineer: thermal design engineer is indispensable in a product R&D team that pursues exquisite and compact products. Through the analysis of heat source distribution, a reasonable air duct system is designed to control the temperature rise of the system to ensure the stable and reliable operation of the product. It is hard to imagine that a notebook design team can make reliable and stable notebook products without the participation of thermal design engineers. (Note: In some companies, structural engineers are also responsible for PCB thermal simulation and thermal design).
Process engineer: prepare the process parameters for PCB design of the company according to the process capabilities of PCB processing manufacturers and SMT equipment/manufacturers of the company. Participate in the design of specific boards and PCBs to ensure the producibility and processability of PCBs.
In consideration of the needs of self communication, technology improvement and personnel backup, each of the above types of work shall have at least 3 people. For companies with limited team size and large R&D demand fluctuation, it is a wise move to properly reserve some composite generalists and appropriately seek external resources according to their own needs to solve their own R&D problems.
Let's take a look at the formation process of PCB design teams of IT industry giants:
In 1980, the company's internal hardware engineer concurrently worked as PCB designer;
In 1990, CAD engineers beCAMe independent as a specialized department;
In 1995, professional PCB DESIGN HOUSE became popular in North America and Japan
In 2000, the specialized division of labor became more and more detaiLED, and the types of work such as database building, SI, EMC, thermal design, and process were gradually independent; More than 50% of PCB designs in North America and Japan are completed by professional design companies; SI, EMC and other types of work gradually form their own systems;
In 2003, a professional design company led by Yibo Technology brought the PCB design outsourcing concept into China;
In 2008, the company had clear internal division of labor and complete types of work. And reasonable use of resource outsourcing, peak staggering design and technology outsourcing has become a trend.
PCB design
2、 Hardware Essential Basis for High Performance PCB Design
Since PCB design entered the high-speed era, signal integrity knowledge based on transmission line theory has overshadowed basic hardware knowledge. It was suggested that only the front end and the back end (the front end refers to the IC design, and the back end refers to the PCB design) will be available for hardware design ten years later. It is enough to have a system engineer to integrate them. It is easy to doubt the necessity of learning the basic hardware knowledge. In fact, both IC engineers and PCB engineers must have knowledge of R, L, C and basic gate circuits.
High performance PCB design is inseparable from the basic knowledge of power supply and FPGA common sense. Even the signal integrity analysis based on the transmission line theory is also considered from the research of micro elements based on R, L and C.
PCB design engineers must have basic circuit knowledge, such as high frequency, low frequency, digital circuit, microwave, electromagnetic field and electromagnetic wave. Being familiar with and understanding the basic functions and hardware knowledge of the designed products is the basic condition for completing a high-performance PCB design.
3、 Challenges and Engineering Implementation of High Performance PCB Design
PCB design is a better art without the best. A PCB design with excellent performance often faces the following challenges.
1. Challenges of R&D cycle
Statistics show that the design of a laptop generally takes only half a year from project approval to listing. The research and development of a mobile phone, from project establishment to listing, takes only 3 months on average. As an important part of product development, PCB design time is gradually compressed, compressed and recompressed.
In April 1985, Toshiba Mizoguchi engineers designed a T1100 pocket machine, which led the rise of the computer industry. Since then, the R&D cycle of computer motherboards has also significantly accelerated.
Figure 1: Changes in the design cycle of the computer motherboard
In EDADOC, the PCB design of notebook is basically controlled within three weeks, and the PCB design time of mobile phone is generally expected to be 10 days.
How can PCB engineers face this challenge in the face of shrinking R&D expectations in the MARKet?
First of all, we should use the first-class EDA tool software
Efficient EDA tool software brings not only the improvement of efficiency, but also the revolution of design concept. Among the numerous EDA tool software, Cadence's PSD series undoubtedly plays a flagship role in the industry. From individual combat 10 years ago, to "sub drawing" later, to "partition" now, the multi person parallel design provided by Cadence Allegro has turned the originally impossible R&D cycle into reality. In EDADOC, 92% of PCB designs use concurrent design.
For example, EDADOC once completed the front and back simulation, layout, and routing of an XDSL board with 20,000 PIN in 6 days. Among them, the parallel design is very important.
Taking a conventional notebook motherboard PCB design as an example, let's take a look at the traditional "individual combat" (a PCB engineer is responsible for it) and the main PCB design data under the working mode of three shifts adopted by some companies and the working mode of parallel design:
Secondly, intervene in the product R&D process in advance to reduce subsequent rework.
In the overall scheme design stage, PCB engineers are involved in research and development, focusing on the system architecture design and demonstration of products; In the overall design stage, carry out preliminary PCB design feasibility evaluation; In the detailed design stage, the principle scheme design is synchronized, and the device selection, structural design, and thermal design are involved. In this way, when R&D enters the PCB design process, the main work will be simplified, and the rework in the PCB design process due to excessive device volume, insufficient drive capability, infeasible topology scheme, and structural heat dissipation problems will be reduced.
Third, the design concept of "one board success"
IBM's senior consultant once pointed out the problem of a domestic R&D team: "There is no time to do things well at one time, but there is time to do things again and again". In the current market competition environment, we have experienced PCB design engineers, improve the design process, and strive for success with various tools and software. What is saved is not only the cost of making a PCB, but also the R&D cycle of the whole process. Win market opportunity window for products. Both PCB engineers and product R&D directors must have the concept of "one board success" in PCB R&D.
Finally, reuse modules and pay attention to technology
In many well-known domestic companies contacted by the author, they attach great importance to module reuse, and effectively shorten PCB design time while ensuring technology precipitation.
In a word, in terms of design concept, we should intervene in R&D in advance, adopt concurrent design, adopt the concept of "one board success" and reduce the number of R&D times, plus advanced tool software such as Cadence PSD, we do not need to work overtime, let alone two or even three shifts to solve the problem of PCB R&D cycle.
2. Cost challenges
The cost of PCB includes explicit cost and implicit cost
Dominant cost mainly includes PCB production and chip mounting cost.
For the control of explicit cost, we can reduce the explicit cost of PCB design by getting familiar with and understanding the process capability of conventional board plants and the process requirements of placement equipment, selecting a reasonable number of layers, setting a reasonable stack structure, and designing parameters.
Implicit cost includes personnel investment, technical risk, time cost during PCB design, especially the opportunity cost of listing opportunity window.
In fact, the implicit cost of PCB design is far greater than its explicit cost.
For example, the market opportunity window for general mobile phones is about half a year. If one more R&D is added due to PCB design problems, it will not only bring about 1-2 months of time loss for fashionable mobile phone products, but also the failure of the entire product.
For the control of hidden costs, the company's senior executives and R&D directors should have the concept of graSPIng the core, opening up the surrounding, strong combination and one-time success, and consider the cost at the beginning of the design. Reasonably use external resources to solve the problem of self-developed short boards and reduce the hidden cost of product development.
3. Challenges of high-Speed PCB design
With the continuous improvement of the signal speed, the signal integrity continues to perplex the R&D personnel, including bus driving ability, signal reflection, crosstalk, overshoot, oscillation, back channeling, attenuation, etc; Sometimes the timing is also included in the signal integrity scope. Signoise, a simulation module based on IBIS model in Allegro, can easily build topology for simulation.
Allegro's simulation tool has a good interface with the wiring platform. After PCB wiring is completed, you can also directly extract the wiring parameters from the PCB to the Signoise platform for post simulation to verify the wiring effect.
The routing constraints extracted from the simulation can be directly imported into Allegro's electrical rule manager, which can conveniently constrain the equal length rules required by the timing. When routing, Allegro can give an alarm in real time when the length does not conform to the specified rules.
Figure 2: Example of rule manager (click the picture to see the larger picture)
As shown in the figure, when the length is within the predetermined range, the corresponding area in the table displays green; When the length is not within the predetermined range, whether it is too short or too long, the corresponding area of the table is displayed in red.
4. PCB design challenge
Faced with the continuous improvement of the density of PCB design, PCB engineers must follow the forefront of the industry, understand new materials and new PCB processes, and use first-class EDA software that can support high-density PCB design, so as to meet the increasing density challenges faced in the process of product development. It is said that the upcoming PSD 16.2 will have a great breakthrough in HDI design, and we are looking forward to it.
5. Challenge of power and ground noise
The power and ground planes are used as the reference planes and return channels of the signal lines, and the noise of the power and ground will be directly connected to the signals taking them as the reference planes. To solve the problem of power and ground noise is not only to consider the level stability of the power supply itself, but also an important factor to solve the reliability problem of high-speed signals.
The power supply design of high-speed PCB should first clarify the power tree and analyze the rationality of the power channel.
. DFM Challenges
To solve the DFM problem, in addition to the single board process engineer formulating the process standard suitable for the company, PCB design engineers need to receive systematic and comprehensive DFM knowledge training. PCB engineers need to constantly understand the current situation of PCB production and processing capacity in the industry, and select appropriate process routes and design parameters in combination with the actual situation of the company. Comprehensively consider the choice of electrical performance and DFM. In addition, there must be full-time library building personnel on the PCB packaging library to solve the DFM problem from the source.
Allegro has a special library building module, which can easily design the packaging library and the bonding pad of the packaging library according to the device datasheet. Good packaging design is the basis of DFM design.
As high-performance PCB design, these challenges are sometimes contradictory requirements. PCB design engineers need to make use of their comprehensive experience, compromise in the face of these challenges, find an optimal combination point, and finally complete the engineering implementation of high-performance PCB design.
4、 If a worker wants to do his job well, he must first sharpen his tools
High performance PCB design is inseparable from the support of advanced EDA tool software. Cadence's PSD series has powerful functions in high-speed PCB design. Its front and back simulation modules ensure signal quality and improve the one-time success rate of products; The use of its physical and electrical rules can intelligently realize technical requirements such as difference distribution line, equal length control, etc; Support concurrent design and shorten R&D time; Support module reuse, pay attention to technology precipitation, ensure design quality and improve design efficiency.
With a high-performance EDA tool software and an experienced PCB design engineer, the realization of high-performance PCB design is practically guaranteed. As a pcb design company with more than 150 PCB engineers, EDADOC is committed to high-speed, high-density and high-performance PCB design.
然后
联系
电话热线
13410863085Q Q
微信
- 邮箱