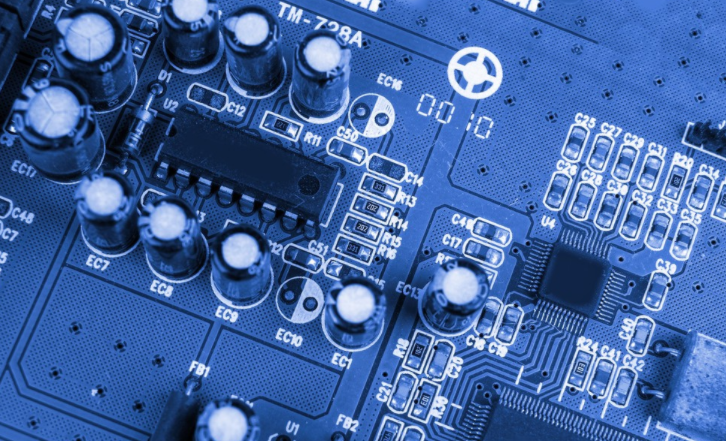
The process and cause of conductive hole blockage of PCB are introduced in detail
Through holes act as interconnections and conductors The development of the electronIC industry has also promoted the printed circuit board, putting forward higher requirements for the production process and surface mounting technology of the printed circuit board And should meet the following requirements at the same time:
(1.) There is only copper in the via hole, and the solder mask can be plugged or not plugged;
(2) There must be tin lead in the via hole, with a certain thickness requirement (4 microns), and no solder blocking ink shall enter the hole;
(3) The through holes must have solder mask ink plug holes, which are opaque, free of tin rings, tin beads, and flatness requirements
Through holes are also calLED through holes. To satisfy customers
printed circuit board
With the development of electronic products in the direction of "light", thin and short PCB boards have also developed to high density and high difficulty. Therefore, a large number of SMT and BGA PCB boards have appeared, and customers need to plug and unplug when installing components. Hole has five main functions:
(1) Prevent the tin from the via hole through the component surface and cause a short circuit when the pcb circuit board passes through the wave soldering; Specially when we put the via on the BGA pad
(2) Avoid flux residue in the via holes;
(3) After the surface mounting of the electronics factory and the assembly of the components are completed, the PCB circuit board must be vacuumed to form a negative pressure on the testing machine to complete:
(4) Prevent surface solder paste from flowing into the hole, causing false soldering and affecting placement;
(5) Prevent the tin balls from popping up during wave solving
Realization of Conductive Hole Plugging Process
For surface mount boards, especially for the installation of BGA and IC, the through-hole plug must be flat, concave convex plus or minus 1mil, and the edge of the through-hole must be free of red tin; The through hole hides the solder ball to meet the customer's requirements. The through hole plugging process can be described as diverse, which is very long and difficult to control. During the hot air leveling and green oil solderability test, the oil often falls; Oil explosion and other problems occur after solidification And some comparisons and explanations are made in the process and advantages and disadvantages:
Note: The working principle of hot air level is to use hot air to remove excess solder from the surface and holes of the printed circuit board
Printed circuit board
1. Hole plugging process after hot air leveling
The process flow is: board surface solder mask-HAL-plug hole-curing. Non clogging process is adopted in production After the hot air is leveled, the aluminum plate MESh or ink blocking mesh is used to complete the through hole blockage of all fortresses required by the customer Plug ink can be photosensitive ink or thermosetting ink Under the condition that the wet film color is consistent, the hole plug ink shall be the same as the ink on the board surface This process can ensure that the through-hole will not leak after the hot air is leveled, but it is easy to cause the ink in the plug hole to pollute the board surface and uneven Customers are prone to false soldering (especially in BGA) during mounting. So many customers do not accept this method
2. Hot air flattening the front plug hole process
2.1 Plug the hole with aluminum plate and solidify the board to transfer the graphics
This technical process uses a CNC drilling machine to drill out the aluminum sheet that needs to be plugged to make a screen Plug hole ink can also be used with thermosetting ink, and its characteristics must be high hardness, The resin has SMAll shrinkage and good adhesion with the hole wall The technological process is: pretreatment - plug hole - grinding disc - pattern transfer - etching - surface resistance welding This method can ensure that the plug hole of the through-hole is flat, and there will be no quality problems such as oil explosion and oil drops at the hole edge The requirements for copper plating on the whole plate are very high, and the efficiency of the grinder is also very high, to ensure that the resin on the copper surface is completely removed, and the copper surface is clean and free of pollution Many PCB factories do not have thick copper process, and the equipment efficiency does not meet the requirements, which leads to the lack of use of this process in PCB factories
2.2 Directly screen print the board surface solver mask
This process uses a CNC drilling machine to drill out the aluminum sheet that needs to be plugged to make a screen The 36T screen is used to directly screen the surface of the circuit board The process flow is: pretreatment of plug hole wire mesh, pre drying, exposure, development and curing This process can ensure that the through hole is well covered with oil, the plug hole is flat, and the wet film color is consistent After the hot air is leveled, it can ensure that the through-hole is not tinned and the tin bead is not hidden in the hole, but it is easy to cause ink in the hole after curing Poor solderability caused by pad; After the hot air is leveled, the edge of the through-hole bubbles and the oil is removed It is difficult to use this process to control production, and process engineers need to use special processes and parameters to ensure the quality of plug holes
2.3 The aluminum plate is inserted into the hole, developed, pre cured, polished, and then welded on the surface of the plate
Use a CNC drilling machine to drill out the aluminum plate that needs to be blocked to form a screen, and install it on the displacement screen printing machine to block the hole The sealing hole must be full and protruding on both sides The process flow is as follows: pretreat the plug hole, pre bake the development and pre curing board, and solder the mask on the surface Because this process uses plug hole solidification to ensure that the through-hole will not lose oil or explode after HAL. However, after Hal, it is difficult to completely solve the problem of tin storage in the through-hole and tin on the through-hole, which is unacceptable to many customers
2.4 At the same time, complete the plate surface resistance welding and plug hole
This method uses a 36T (43T) screen, which is installed on the screen printing machine. When using a backing plate or a nail bed, all through holes are blocked when finishing the plate surface The process flow is: pretreatment screen - prebake exposure development curing Short processing time, high equipment utilization Ensure that the through-hole will not lose oil after hot air leveling, and that the through-hole will not be tinned However, due to the use of wire mesh to block the hole, there is a lot of air in the through-hole, Air expands and penetrates the solder mask, causing voids and unevenness A few through holes will be hidden during hot air leveling At present, after a lot of experiments, our company has selected different types of inks and viscosities, adjusted screen printing pressure, etc, The holes and unevenness of through holes are basically solved, and the mass production process of printed circuit board is adopted
The above is the explanation given by the editor of pcb circuit board company.
If you want to know more about PCBA, you can go to our company's home page to learn about it.
In addition, our company also sells various circuit boards,
High Frequency Circuit Board and SMT chip are waiting for your presence again.
然后
联系
电话热线
13410863085Q Q
微信
- 邮箱