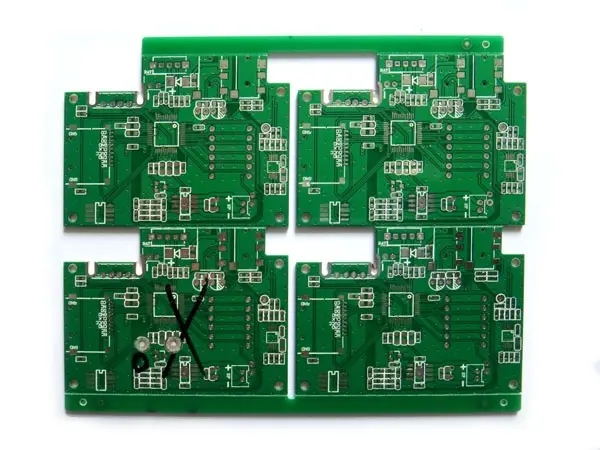
What are the techniques for reducing PCB design risks? Why is the ground wire divided?
1. What are the skills to reduce the risk of PCB design?
During PCB design, if possible risks can be predICted in advance and avoided in advance, the success rate of PCB design will be greatly improved. Many companies will have an indicator of the success rate of PCB design when evaluating projects.
The key to improve the success rate of the first board is the signal integrity design. In the current electronic system design, there are many product solutions that chip manufacturers have prepared, including what chips to use and how to build peripheral circuits. Hardware engineers almost don't need to consider the circuit principle, they just need to make PCB by themselves.
However, it is in the process of PCB design that many enterprises encounter difficulties, either the PCB design is unstable or does not work. For large enterprises, many chip manufacturers will provide technical support to guide PCB design. However, it is difficult for some SMAll and medium-sized enterprises to obtain such support. Therefore, we must find a way to complete it by ourselves, so there are many problems, which may require several versions, and debugging takes a long time. In fact, if we understand the design method of the system, these can be completely avoided. Next, let's talk about three techniques to reduce PCB design risk.
First, in the system planning stage, it is better to consider the signal integrity. The whole system is built in this way. Can signals be received correctly when they are transferred from one PCB to another? This needs to be evaluated in the early stage, but it is not difficult to evaluate this problem. A little knowLEDge of signal integrity and a little SIMple software operation can do it.
2. During PCB design, use simulation software to evaluate the specific routing and observe whether the signal quality can meet the requirements. The simulation process itself is very simple. The key is to understand the principle knowledge of signal integrity and use it for guidance.
Third, risk control must be carried out during PCB manufacturing. There are many problems that can not be solved by simulation software at present, and must be controlled manually by designers. The key to this step is to understand where there are risks and how to avoid them. What is needed is signal integrity knowledge.
If we can grasp these three points in the PCB design process, the PCB design risk will be greatly reduced, the probability of error will be much smaller after the printing, and debugging will be relatively easy.
2. What should be paid attention to in the mixed signal PCB design process?
(1) PCB is divided into independent analog part and digital part
(2) Appropriate component layout
(3) A/D converter placed across partitions
(4) Do not divide the ground: lay it uniformly under the analog part and digital part of the circuit board
(5) In all layers of the circuit board, digital signals can only be wired in the digital part of the circuit board; Analog signals can only be wired in the analog part of the circuit board
(6) Realize the division of analog and digital power supply
(7) The wiring shall not span the gap between the divided power planes
(8) The signal lines that must cross the gap between the split power supplies shall be located on the wiring layer adjacent to the large area
(9) Analyze the actual flow path and mode of return ground current
(10) Apply the correct routing rules
3. Why should the ground wire be divided in PCB design?
The purpose of land division is mainly for EMC's consideration, and it is worried that the power supply of digital part and the noise on the ground will interfere with other signals, especially analog signals through the transmission path. As for the division of signal and protective ground, the consideration of ESD static discharge in EMC is similar to the role of lightning rod grounding in our life. No matter how divided, there is only one land in the end. It's just that the way of noise EMIssion is different.
4. How to solve the contradiction between manual wiring and automatic wiring of high-speed signals?
Most automatic routing devices with strong routing software now have set constraints to control the winding mode and the number of vias. The setting items of winding engine capacity and constraints of various EDA companies are sometiMES far from each other. For example, whether there are enough constraints to control the way of serpentine winding, and whether the distance between differential pairs can be controlled. This will affect whether the routing method of automatic routing can conform to the designer's idea. In addition, the difficulty of manually adjusting the wiring is also absolutely related to the ability of the winding engine. For example, the pushing ability of routing, the pushing ability of vias, and even the pushing ability of routing to copper coating, etc. Therefore, the solution is to choose a router with strong winding engine.
5. How to consider impedance matching when designing high-speed PCB design schematic diagram?
When designing high-speed PCB circuits, impedance matching is one of the elements of design. The impedance value has an absolute relationship with the routing method. For example, when walking on the surface layer (microstrip) or the inner layer (stripe/double stripe), the distance from the reference layer (power layer or stratum), the routing width, PCB material, etc. will affect the characteristic impedance value of the routing. That is to say, the impedance value can be determined only after wiring. The general simulation software can't take into account some discontinuous impedance wiring due to the * * of the line model or the mathematical algorithm used. At this time, only some terminators (such as series resistance) can be reserved on the schematic diagram to mitigate the effect of discontinuous impedance. The real fundamental solution to the problem is to avoid impedance discontinuity when wiring.
6. When designing high-speed PCB, what aspects should designers consider the rules of EMC and EMI?
Generally, radiation and conducted shall be considered simultaneously in EMI/EMC design The former belongs to the part with higher frequency (>30MHz) and the latter belongs to the part with lower frequency (<30MHz) Therefore, we cannot only pay attention to the high frequency and ignore the low frequency. A good EMI/EMC design must consider the location of components, PCB stack arrangement, important online routing, and component selection at the beginning of the layout. If there is no better arrangement in advance, it will take twice the effort and increase the cost if it is solved afterwards.
7. What are the methods to eliminate transmission line interference in PCB design?
(a) Avoid impedance discontinuity of transmission line. The point of discontinuous impedance is the point of sudden change of transmission line, such as straight corner, through hole, etc., which should be avoided as far as possible. The methods are as follows: avoid the straight corner of the line, and try to walk at a 45 ° angle or arc as much as possible, or at a large angle; Use as few vias as possible, because each vias are impedance discontinuities, and the outer signal shall not pass through the inner layer, and vice versa.
(b) Do not use pile lines. Because any pile line is a noise source. If the pile line is short, it can be terminated at the end of the transmission line; If the pile line is long, it will take the main transmission line as the source, which will cause great reflection and complicate the problem. It is recommended not to use it.
8. Why do you want to lay copper?
There are several reasons for copper laying. 1,EMC. For large areas of ground or power supply, copper will play a shielding role, and some special areas, such as PGND, play a protective role. 2. PCB process requirements. Generally, to ensure the electroplating effect or the lamination will not deform, copper is laid on PCB layers with less wiring. 3. Signal integrity requirements: provide a complete return path for high-frequency digital signals, and reduce the wiring of DC network. Of course, there are also reasons such as heat dissipation, copper coating required for installation of special devices, etc.
9. How does Mentor's PCB design software support BGA, PGA, COB and other packaging?
Mentor's autoactive RE is developed from the veritest acquired, and is the first gridless, arbitrary angle router in the industry. As we all know, for ball grid array, COB device, gridless, arbitrary angle router is the key to solve the routing rate. In the latest autoactive RE, functions such as pushing vias, copper foil, and REROUTE have been added to make its application more convenient. In addition, it supports high-speed cabling, including signal cabling with delay requirements and differential pair cabling.
10. Do you also need to consider the esd of the chip itself when selecting chips?
Whether it is a double-layer board or a multi-layer board, the floor area should be increased as much as possible. The ESD characteristics of the chip itself should be considered when selecting the chip. These are generally mentioned in the chip description, and even the performance of the same chip from different manufacturers will be different. When designing, pay more attention and consider more comprehensively. The performance of the circuit board will also be guaranteed. However, ESD problems may still occur, so the protection of institutions is also very important for ESD protection.
然后
联系
电话热线
13410863085Q Q
微信
- 邮箱