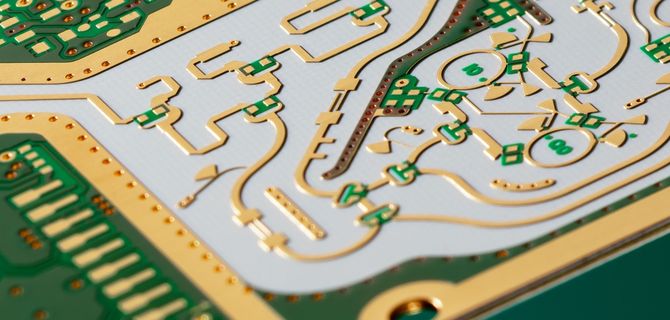
Analysis and improvement of PCB reflow cracked board
Preface: Reflow welding analysis and improvement of burst plate
With the development of electronIC products in the direction of multi function, high-density, miniaturization, more and more 3D space, the demand for heat dissipation becomes more and more important At the same time, the thermal stress and warpage caused by different thermal expansion coefficients of many materials increase the risk of assembly failure, and then the probability of early failure of electronic products will also increase A little bigger Therefore, PCB welding reliability becomes more and more important The following introduces the plate failure phenomenon in reflow welding and its improvement methods for reference
1 Plate burst phenomenon in reflow welding
1.1 Definition of burst board
Definition: In the process of reflow soldering (especially lead free applications), the separation phenomenon that occurs between the PP layer and secondary layer (L2.) coupler foil brown surface of the HDI multilayer PCB during the second
Compression, we define it as bursting plate According to the slice analysis, the plate explosion occurred in the densely buried area of 1-2 layers; No fragments or other abnormalities are found; The slicing showed that the board was badly cracked and some of the second layer circuits were pulLED open
PCB board
1.2 Factors that affect the board burst
â The formation source of volatile matter is a necessary condition for the explosion
1. Moisture absorption problem
The following shows that the existence of water in the PCB, water vapor diffusion pipe and water vapor pressure change with temperature, revealing that the existence of water vapor is the main cause of PCB explosion The
Moisture in the PCB mainly exists in the residual molecules, as well as the macro physical defects (such as voids, micro tracks) inside the PCB The water absorption rate and equilibrium water absorption of epoxy resin are mainly determined by
the free volume and the concentration of polar groups. The larger the free volume is, the faster the initial water absorption is. The polar group has affinity for water, which is the main reason why epoxy resins have high water
absorption. The greater the content of polar groups, the greater the equilibrium water absorption In a word, the initial water absorption of epoxy resin is determined by the free volume, while the equilibrium water absorption is determined
by the content of polar groups. On the one hand, temperature is added during lead-free reflow soldering of PCB, which can lead to hydrogen bonding between water and polar groups in free volume
energy to diffuse in the resin. The water diffuses outward and accumulates in the voids or microcracks, and the molar volume fraction of water in the voids increases
On the other hand, with the increase of welding temperature, the saturated vapor pressure of water will also increase The saturated vapor pressure of water vapor at 224°C is 2500kPa; the saturated vapor pressure of water vapor at 250°C is 4000kPa; and
When the welding temperature risks to 26.0 ° C, the saturated vapor pressure of water vapor even reaches 5000kPa When the binding strength between data layers is lower than the saturated vapor pressure generated by water vapor, the
Materials Therefore, moisture absorption before welding is one of the main reasons for PCB delamination and bursting
2. Effect of moisture during storage and production HDI multilayer PCB is a kind of humidity sensor, and the water in PCB has a very important influence on its efficiency For example:
(a) The moisture in the storage environment will cause significant changes in the characteristics of PP (prepreg);
(b) Without protection, PP can easily absorb water Figure 1.3 shows the hygroscopicity of PP under 30% storage, 50%, and 90% relative humidity; the relationship between the storage time and moisture
Absorption rate of PP The relationship is objective. With the passage of time under static placement, the water content of concrete PCB will gradually increase The water absorption rate of vacuum packaging is higher than the water absorption
Rate of no vacuum packaging, water absorption changes with the increase of temporary storage time
(c) Moisture mainly depends on the interface between various substances in the resin system
3. Harm of moisture absorption
(a) Increase the volatile content of PP.
(b) The presence of moisture in the PP resin weakens the cross linking between the resin molecules multilayer boards are prone to white spots, blistering, delamination in hot oil or solder bath and hot air leveling
â µ Poor adhesion between PP and copper foil is a sufficient condition for plate burst
1. Phenomenon description It can be seen from the slice analysis that the position of the plate burst is between the secondary pressing pp and the contact surface (browning surface) of the copper foil.
Copper is a nonpolar substance in metal state. In summary, many adhesives have little adhesion to copper foil If the copper foil surface is not treated, it will not have sufficient
adhesion and heat resistance. The early browning treatment method on the surface of copper foil was to form reddish-brown cuprous oxide (Cu2O) on the surface of the copper foil through chEMIcal treatment. When it is bonded to a resin-
Although the adhesion is increased at room temperature, the peeling occurs near 200 ° C This is because Cu2O is unstable to heating and will fall off from the copper foil after heating In the 1960s, researchers at
Toshiba Corporation in Japan discovered that after treatment with a special chemical solution, the black velvet-like film (CuO) formed on the surface of the copper foil has finer crystals and can firmly adhere to the surface of the copper foil. The
Stability is also very good In the mid-1990s, Europe and the United States used a new type of browning process in which the inner conductive pattern of a new Multilayer board was chemically
oxidized to replace the traditional blackening process has been widely used in the industry
2. Mechanism of browning enhancing adhesion
The new browning process, its chemical reaction mechanism is: 2Cu + H2SO4 + H2O2 + nR1 + nR2 - CuSO4 + 2H2O + Cu(R1 + R2)
In the browning tank, due to the micro corrosion effect of H2O2, the surface of the Copper substrate has formed an uneven microstructure. In addition, 6-7 times of the bonding area of the untreated smooth copper surface can be obtained At the
At the same time, a layer of organic metal film chemically bonded to the copper substrate surface is deposited on the copper substrate, and the SEM image of the copper surface of the substrate is brown And after the adhesive
Enters the compact compact part, which also adds the mechanical meshing effect
3. Factors affecting the browning effect
The quality and effect of browning depend on the refinement of the process parameters control, such as:
(a) Choose a potion with advanced formula:
The browning layer with Atotech point has a large roughness
(b) Strengthen the monitoring of bath liquid composition during the production process.
(c) Browning (or black copper oxide) film thickness: Browning (or black copper oxide) film and PP bonding strength, acid and alkali resistance, corona resistance and high temperature resistance are related to the structure and thickness of the film
The above is the explanation given by the editor of pcb circuit board company.
If you want to know more about PCBA, you can go to our company's home page to learn about it.
In addition, our company also sells various circuit boards,
High Frequency Circuit Board and SMT chip are waiting for your presence again.
然后
联系
电话热线
13410863085Q Q
微信
- 邮箱