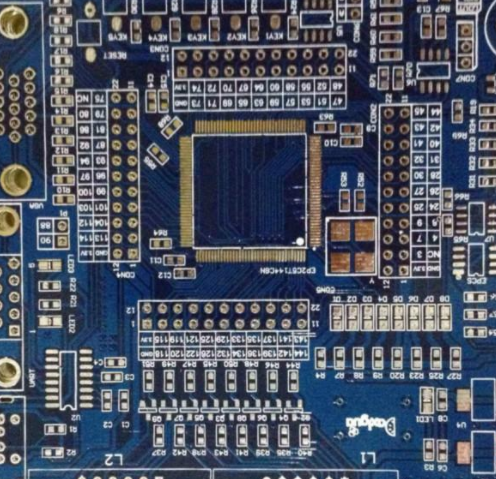
How to deal with the tin tip in PCB wave soldering
The reason for the tin tip phenomenon of long pin components during wave soldering: During soldering, most of the flux on the PCB will be washed off as the soldering tin wets and covers the PCB surface, leaving the flux between the PCB and the tin wave. When the PCB leaves the tin wave, the flux left on the PCB will prevent the oxidation of solder. If the space between solder joints is SMAll, there will not be much flux left in this process, so it is almost impossible to prevent solder oxidation. As a result, when the tin wave is separated from the PCB board, the solder will be oxidized and an oxide layer will be formed on the surface. In the final stage of separation, the surface tension of liquid solder will make some solder remain on the pins of the component; If this part of the solder surface is oxidized, the solder will be wrapped in the oxide layer to form a tin tip.
If there is a large area covered with soldering tin and almost no flux can help prevent oxidation, this phenomenon will be more obvious. Therefore, we can understand why long pins are more likely to lead to tin tips, because only the flux left on the PCB surface can help prevent oxidation. In the process of separating the PCB from the tin wave, because long pins are far away from the PCB surface, the anti oxidation effect of the flux on the pins on the PCB surface is signifICantly reduced. SIMilarly, tin tips are also easy to occur in places with large pad areas on PCB boards. Due to the heat dissipation effect, the solder joints on the shielding cover are also prone to tin tips. If the heat brought by soldering tin to the solder joint is quickly absorbed by the shielding cover, the soldering tin will almost solidify immediately after being separated from the tin wave. As a result, the solidified tin cannot flow back to the solder joint to form a tin tip.
Solution to tin tip phenomenon of long lead components during wave soldering: make the extended component pins shorter, so that the flux left on the PCB can still play an anti oxidation role. Generally speaking, increasing the amount of flux will not work because the flux is likely to be washed off when the PCBA passes the tin wave; Of course, more flux is helpful for wetting the pad; If the flux with strong adsorption on PCB is used, it may help prevent tin tip phenomenon. When PCB passes through tin wave, adding inert gas to cover or create an environment conducive to reducing oxidation can also avoid tin tip phenomenon. If the solder tip is caused by the heat dissipation effect near the solder joint, the solder joint design should be optimized.
然后
联系
电话热线
13410863085Q Q
微信
- 邮箱