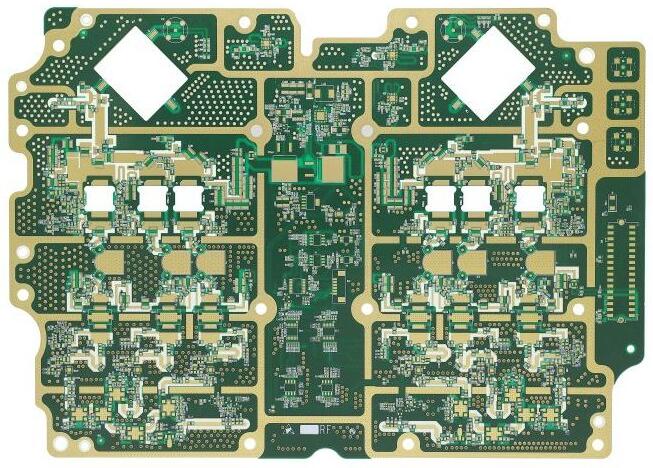
PBT engineers talk about the three proof coating of PCBA
3 Anti paint refers to the applICation of a uniform layer of ordinary 3 anti paint in the area where PCBA needs to be maintained It can effectively mask the areas and electronIC components that need PCBA maintenance, as well as its operating environment, and fully protect PCBA from damage, thus improving the reliability of PCBA and further improving the reliability of electronic equipment PCBA, high salt, dust and vibration of electronic equipment working in harsh environment such as high humidity are easily affected by system failure caused by salt spray, humidity and mold Therefore, PCBA's 3 anti coating technology is attracting more and more attention
1. 3 Anti coating technology and construction process
Before applying 3 # anti paint, we need to clean PCBA to ensure clean appearance and good adhesion of 3 # anti paint. The three anti coating processes include spraying, brushing, DIPping and other different processes. The viscosity requirements of the three kinds of paint are different with different painting processes. When selecting spraying process,
Circuit board
3. The minimum viscosity is required for paint protection to meet the requirements of "spraying" capacity, while the highest viscosity is required for impregnation 3 3 The viscosity of the paint is determined by the solid content of the paint 3 Anti paint manufacturers usually have their own thinners to dilute products with different concentrations and apply them to different coating process requirements This PCBA cleaning machine for Boyson uses full pneumatic pipes, which are not connected to the power supply at all, so there is no fire risk At the same time, it uses environmentally friendly water-based solvents, which will not harm the environment or human health It is safe and environmentally friendly Belongs to
PBT engineers talk about 3 anti coating technologies of PCBA
The second is 3. Basic coating method of anti coating
Generally, manual spraying, dipping and brushing are adopted. Although the operation is SIMple and does not require any equipment investment, the coating quality is difficult to guarantee. Poor universality of paint film thickness, 3. Large loss of anti paint, environmental pollution, painting. Sometimes it is easy to splash and pollute adjacent sockets, and selective spraying cannot be completed. It is necessary to manually paste adhesive tape to cover the equipment that needs to be protected before spraying, and some gaps between the parts and the side of the parts cannot be sprayed. The existence of these problems has affected the product quality and needs to be solved urgently. The selective active coating machine is the perfect solution to the above problems. It can finish the precise spraying of PCBA. The spraying head can avoid non stick paint parts, and the spraying thickness is uniform and ordinary.
3. Efficiency of selective active coating equipment
In order to ensure the high quality of anti coating, the selective active coating machine shall meet the following technical parameters and efficiency requirements:
1. Full active online flow operation, reducing manual turnover program;
2. With continuous connection of irregular curve points/lines/surfaces/arcs/circles and 3-axis linkage function;
3. Several different nozzles can be suspended at the same time, and the equipment can be automatically switched according to different spraying requirements to meet the requirements of different spraying areas;
4. CCD visual centering system can be selected to eliminate PCBA or fixture positioning error and improve spraying accuracy;
5. It can accurately control the spraying amount of 3 anti paint.
4、 3 Anti coating process requirements
In order to complete high quality 3 anti coating, the following process requirements must be met during the 3 anti coating process:
1. For connectors, connectors, buttons, light-EMItting diodes, gold fingers and other parts that cannot be stained with 3 anti paint, shielding tape must be affixed when brushing, dipping or manual spraying is used. Even if a full active selective coating machine is used, barrier precautions must be taken if the coating area is too close to the non paintable position (less than 5 mm).
2. Before painting, the PCBA surface must be cleaned to remove foreign matters on the PCBA surface. PCBA needs to be cleaned and dried before coating for products with strict requirements such as automobiles, aviation, aerOSPace, navigation and military industries, but the requirements are not high. For general products, dry high-pressure air can be used to remove dust and other dirt on the surface of PCBA.
3. Before selecting selective active coating machine for mass production, attention must be paid to first article inspection Make sure there are no problems such as missing coating, less coating, more coating, and bubbles Devices or areas that are prohibited from coating, such as connectors, shall not be coated with adhesive paint, and the coating thickness shall be uniform before baking
4. During the anti coating period, the humidity of the working environment shall be controlLED below 65% relative humidity As a composite material, PCB will absorb water If it absorbs moisture, 3 the paint will not have enough maintenance effect Therefore, the anti coating process shall be carried out as soon as possible after the circuit board is assembled If the PCBA is placed for a long time and then sprayed with 3 anti paint, it is better to bake the PCBA before spraying Bake at 60 ℃ for 24 hours
The above is the explanation given by the editor of pcb circuit board company.
If you want to know more about PCBA, you can go to our company's home page to learn about it.
In addition, our company also sells various circuit boards,
High Frequency Circuit Board and SMT chip are waiting for your presence again.
然后
联系
电话热线
13410863085Q Q
微信
- 邮箱