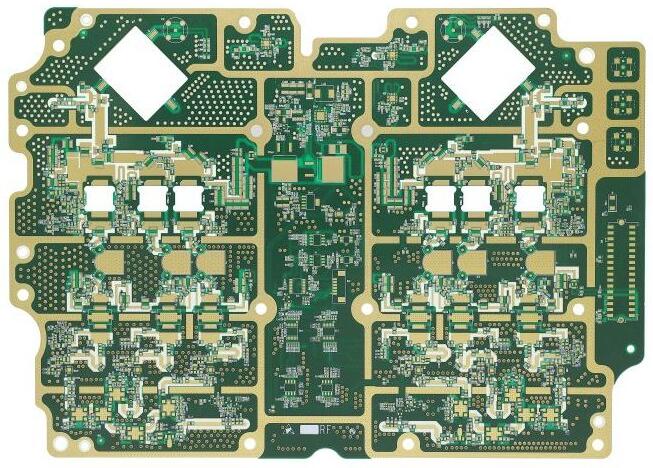
How to strengthen PCB electroplating process management?
PCB electroplating process management is an important link in electroplating production This was determined by electroplating workers after tens of millions of trial and error studies Therefore, electroplating process is highly scientifIC The determination of the process shall not only consider the deposition rate of the coating, the current efficiency of the cathode and anode, the balance of metal ion dissolution and deposition, as well as the stability of pH value, a wide range of temperature and current density, and the light selection rate and level Efficiency, comprehensive development of the brightness range and other aspects Therefore, we must pay special attention to various technical parameters specified in the process. Only in this way can we guarantee a good coating On how to strengthen the management of PCB electroplating process, the author puts forward the following points
1. Process management
1.1 Pretreatment
The pretreatment of PCB electroplating is the basis of electroplating quality. If the pre electroplating process is not good, the electroplating coating will appear halo, bubble, shelling, or even both, leading to the scrapping of defective products. The pretreatment of electroplating is mainly to remove the oil stain, oxide skin, rust, etc. on the electroplated parts. This not only ensures the good adhesion between the substrate and the coating, but also speeds up the deposition of the coating. At the same time, it ensures that the electroplating solution will not be polluted by the oil stain of the plated parts and the introduced foreign metal impurities.
Circuit board
1.2 Detection and management of bath composition
1.2.1 Laboratory analysis
It is a more scientific management method to regularly detect and timely adjust the bath content. The scale of the test can be large or SMAll. For a pure electroplating manufacturer, only some SIMple test equipment and a small amount of investment are required. Personnel can work part-time and can operate after training.
1.2.2 Proportional method
Measure with Baume specific gravity method. This method is only applicable to solutions with relatively simple bath composition. For example, chromium plating is dominated by chromic acid, and sulfuric acid accounts for only about 1%, which can be ignored. This method is also applicable to pretreatment acid (hydrochloric acid or sulfuric acid) and active acid of each channel, and Baume degree can also be used as a reference.
1.2.3 Explore laws and accumulate experience
Take fewer and more frequent channels, gradually explore the consumption law, and take out the loss to supplement, so that the composition is relatively stable and has accumulated some experience. However, this method is certainly not scientific and is mainly controlLED by experience.
1.2.4 Precautions PCB electroplating process management
(1) In order to better manage the process, in addition to carefully controlling the ingredient content, attention must also be paid to the water quality of the disposable water tank, and the wrong addition and wrong addition of chEMIcal raw materials must be prevented. The author once encountered the case that thiourea was added into the nickel plating bath as boric acid, which led to the blackening of the coating. Later, more hydrogen peroxide and activated carbon were added and gradually returned to normal after major treatment. In this regard, the author suggests that the method of "one look, two checks and three additions" should be adopted when adding chemical materials to the plating solution to avoid involuntary losses.
(2) In order to ensure the stability of the plating solution, please carefully bring foreign matters into the plating solution. The author suggests that for nickel plated products on copper, the nickel plating solution must be periodically electrolyzed with corrugated iron plates with a current density of about 0.05am2, or copper remover must be added to ensure the brightness of the area with low current density. In addition, if the parts fall into the nickel plating bath or acid copper plating bath, they must be taken out in time to prevent the accumulation of impurities. For dropped copper parts and zinc alloy workpieces, it is recommended to use window screens to make the flat filter screen slightly wider than the bottom of the groove, and tighten the four corners with plastic tubes (rods). The purpose of removing zinc alloy parts is to avoid or reduce the accumulation of copper and zinc impurities in the nickel plating solution, thus reducing the failure of the plating solution. (3) Incomplete hanger insulation or blistering make the chromium plating solution not clean, leading to the chromium plating solution being brought into the cyanide copper plating solution or nickel plating solution, thus polluting the plating solution and causing failure. This requires that the insulation of the hanger must be intact. For the hanger hanging at the end of the automatic line, take back the chromium, and then hang the workpiece to avoid contamination of the chromium plating solution.
1.3 Operating conditions
1.3.1 Temperature and current density
In practical operation, it is necessary to select the best temperature, which is crucial to the quality and stability of electroplating. Select the best temperature according to various workpieces and strictly control it. This is an important measure to ensure quality. The temperature is usually proportional to the cathode current density. With high temperature (within the process range), the cathode current density can be opened, the coating is fine, and the deposition speed is fast.
1.3.2 Conductive contact
Conductive contact generally refers to the contact between the hanger and the pole, the contact between the anode hook and the pole, the contact between the pole and the copper ingot, the contact between the copper rod and the copper ingot, etc. Each conductive contact point must maintain the copper color to reduce the resistance or non conductivity caused by the local poor contact, which will affect the quality of the plated parts. It is recommended that conductive contact parts should be brushed frequently to keep them clean.
1.3.3 Cathode movement and stirring
The purpose of cathode moving and stirring is to accelerate the convection and diffusion of ions, increase the current density of the cathode, improve the uniformity of the coating, and hydrogen is easy to precipitate. If the moving stroke or frequency of the cathode does not meet the requirements, it is easy to generate gas tumors or stripes when electroplating large flat workpieces. The travel of cathode movement must be controlled at about 10 cm and the frequency must be 15 minutes. In addition to the above effects, air agitation can also reduce the generation of monovalent copper in bright acidic copper solution, but air agitation must be matched with continuous filtration. Its continuous filtration shall not be less than 5-10 cycles per hour, otherwise burrs may easily occur.
2. Quality control
Electroplating enterprises must implement modern quality control. To do a good job in quality control, we must first establish a quality control system in accordance with GB T19,000-ISO9000 quality control standards. Therefore, it is necessary to establish electroplating quality standards, including quality requirements between various processes, such as sanding, degreasing and etching. At the same time, it is necessary to establish corresponding inspection systems, such as finished product inspection methods, which are one after another. Or sampling inspection, etc. Formulate standards, strengthen inspection, prevent unqualified electroplated parts from leaving the factory, prevent unqualified electroplated parts from flowing into the next process between processes, block the occurrence of batch defective products, eliminate defective products in the production process, so as to ensure quality and improve the rate of genuine products. In this regard, the author suggests strengthening the basic work of modern quality control.
3. Control the quality of raw materials
When PCB companies purchase metal and chemical raw materials, they pay more attention to quality as well as price The author thinks that price and quality must be considered If only the price is considered, the plating solution will be unstable, many failures will occur, and finally the electroplating company will suffer losses When purchasing raw materials, the importance of price factors and raw material quality must be considered Price and quality cannot be ignored Only by mastering the quality of raw materials and equipped with a set of modern quality control system can enterprises produce good economic benefits
The above is the explanation given by the editor of pcb circuit board company.
If you want to know more about PCBA, you can go to our company's home page to learn about it.
In addition, our company also sells various circuit boards,
High Frequency Circuit Board and SMT chip are waiting for your presence again.
然后
联系
电话热线
13410863085Q Q
微信
- 邮箱