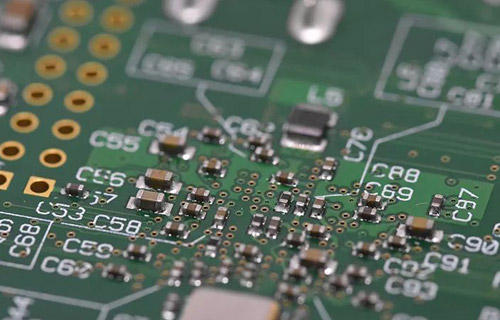
Why do I insert a PCB into the hole
With the development of electronIC products towards "light", thin and short, printed circuit boards are also developing towards high density and high difficulty. As a result, a large number of PCBs with SMT and BGA have emerged, and customers need plug holes when installing components. After a lot of practice, the traditional aluminum plug hole process has been changed, and white grids have been used to complete PCB surface resistance welding and plug holes. The production is stable and the quality is reliable
Through hole and through hole play an important role in the interconnection and conduction of circuits. The development of electronic industry has also promoted the development of PCB. At the same time, higher requirements have been put forward for PCB production technology and Surface Mount Technology. The through-hole plug hole process CAMe into being and should meet the following requirements:
requirement:
(a) If there is copper in the hole, resistance welding can be plugged but not plugged;
(b) There must be tin and lead in the hole, with a certain thickness requirement (4 microns). No solder ink enters the hole, causing the tin bead to be hidden in the hole;
(c) The through-hole must have solder ink plug hole, opaque, Wuxi ring, tin bead and leveling requirements.
circuit board
With the development of electronic products in the direction of "light, thin, short and SMAll", PCB is also developing in the direction of high-density and high difficulty. A large number of SMT and BGA PCBs have emerged. Customers need plug holes when installing components, which mainly have five functions:
(1) Prevent short circuit during wave soldering of PCB from causing tin to flow out from the through hole passing through the component surface; Especially when we put the hole on the BGA pad, we need to make the plug hole first, and then gild it for BGA welding;
(2) Avoid flux residues in conductive holes;
(3) After the surface installation and assembly of components are completed in the electronics factory, the printed circuit board shall be vacuumized to form a negative pressure on the testing machine;
(4) Prevent the solder paste from flowing into the hole, causing false soldering and affecting the installation;
(5) Prevent the solder bead from popping up after wave crest, resulting in short circuit.
Realization of conductive hole plug hole process
For surface mounting plates, especially BGA and IC installation, the plug hole of the conductive hole must be smooth, concave and convex plus or minus 1mil, and the edge of the conductive hole must be free of red tin; The conductive hole hides tin beads. In order to meet the customer's requirements, the process of the conductive hole plug hole can be described as diverse, especially long, difficult to control, and often in hot air leveling and green oil resistance welding experimental oil. Oil explosion and other problems will occur after curing. According to the actual production situation, various PCB plug hole processes are summarized, and the advantages and disadvantages of the processes are compared and elaborated:
Note: The working principle of hot air leveling is to use hot air to remove the excess solder on the surface and hole of PCB, and the remaining solder is evenly covered on the bonding pad, and open the solder wire and surface seal decoration, which is one of the surface treatment methods of PCB.
1. Hole plugging technology after hot air leveling
The process flow is: plate surface plug welding - welding ring - plug hole - curing. Non plugging process is adopted in production. After hot air leveling, according to customer requirements, use aluminum mesh or ink screen to complete the plug holes of all fortresses. The hole plug ink can be photosensitive ink or thermosetting ink. In order to ensure the consistency of wet film color, the hole plug ink is best used with the same ink plate. This process can ensure that the through hole will not drip oil after hot air leveling, but it is easy to cause the blocking ink to pollute the board surface and make it uneven. The customer is prone to virtual welding during installation (especially in BGA). Many customers do not accept this method.
2. Hot air leveling before hole plugging
2.1 Graphic transmission shall be carried out after aluminum plate plug hole, solidification and grinding
This process is processed with a CNC drilling machine. The aluminum alloy plate plug holes are drilLED and made into screen and plug holes to ensure that the plug holes are filled with plug holes. The plug hole ink can also be used as thermosetting ink. Its characteristics must be high hardness, small resin shrinkage change, and good hole wall adhesion. The technological process is: pre-treatment - plug hole - grinding disc - pattern transfer - etching - resistance welding on the plate surface.
This method can ensure the smooth conduction of the plug hole, the hot air leveling will not have oil, the side of the hole will be shot blasted to remove oil and other quality problems. However, the process requirements for one-time thickening of copper make the copper thickness of the hole wall meet the customer's standards. This whole plate has high requirements for copper plating, and also has high requirements for the efficiency of the grinder. It is necessary to ensure that the resin on the copper surface is completely removed, such as the copper surface is clean and free from pollution. Many PCB factories do not have a one-time copper thickening process, and the efficiency of the equipment does not meet the requirements, resulting in the process not being used in PCB factories.
2.2 Block weld the screen printed board surface directly behind the aluminum plate plug hole
This process flow uses a numerical control drilling machine to drill aluminum plates to plug holes and make a screen plate, which is installed on the screen printing machine plug hole. After the plug hole is completed, the machine shall stop for no more than 30 minutes. The 36T screen is used to directly resistance weld the screen printing plate surface. The process flow is: pretreatment - plug hole - screen printing - pre baking - exposure - development - curing. This process can ensure that the conductive hole cover oil is good, the plug hole is flat, and the wet film color is consistent. Hot air leveling can ensure that the conductive hole does not contain tin, and the tin bead is not hidden in the hole, but it is easy to cause poor solderability after the ink pad is solidified in the hole; After hot air leveling, the edge of the through-hole bubbles and drops oil. This process is difficult to be used for production control. It is necessary for process engineers to adopt special processes and parameters to ensure the quality of plug holes.
2.3 Aluminum plug hole, development, pre curing, surface welding of abrasive plate.
Use a numerical control drilling machine to drill the plug hole of the aluminum plate required, make it into a screen, and install it on the plug hole of the screen shifting printing machine. The plug hole must be full, with good protrusions on both sides. Then, after curing and polishing, the surface of the plate shall be treated. The process is: pretreatment - plug hole - pre drying - development - pre curing - surface welding. Because the plug hole curing in this process can ensure that the oil will not drip or penetrate the hole after HAL, but the tin bead hidden in the hole and the tin on the hole after HAL cannot be completely solved, many customers do not accept this.
2.4 The resistance welding and hole plugging on the plate surface shall be carried out at the same time.
This method uses 36T (43T The processing time is short and the equipment utilization rate is high, which can ensure that there is no hot air leveling guide hole on the tin after the oil is discharged from the hole. However, because the hole is blocked by screen printing, there is a large amount of air in the hole memory. When curing, the air expands, breaks through the resistance welding film, and there are holes, which are uneven. Hot air leveling will reduce the amount of tin in the guide hole
然后
联系
电话热线
13410863085Q Q
微信
- 邮箱