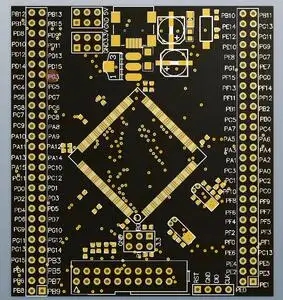
Common process problems and analysis of solder paste
Common problems in solder paste use and analysis Reflow soldering of solder paste is the main board level interconnection method used in SMT chip processing technology. This welding method combines the required weldability perfectly. These characteristICs include easy processing, extensive compatibility for various SMT designs, high welding reliability, low cost, etc; However, when reflow soldering is used as the most important SMT component level and board level interconnection method, it is also challenged by the need to further improve the solderability. In fact, whether reflow soldering technology can withstand this challenge will determine whether solder paste can continue to be used as the primary SMT welding material, especially when the ultra-fine micro pitch technology continues to make progress. Next, we will discuss several major problems that affect the improvement of reflow soldering performance. In order to stimulate the industry to develop new methods to solve this lesson, we will briefly introduce each problem as follows:
Fixing of bottom element
Double sided reflow soldering has been used for many years. Here, the first side is first wired with printed fabric, components are instalLED and soft melted, and then the other side of the circuit board is turned over for PCBA processing. In order to save more money, this process omits the soft melting of the first side, but SIMultaneously melts the top and bottom. A typical example is that the bottom of the circuit board is only equipped with SMAll components, such as chip capacitors and chip resistors, As the design of printed circuit board (PCB) becoMES more and more complex, the components installed on the bottom become larger and larger. As a result, the components fall off during soft melting becomes an important problem. Obviously, the phenomenon of component falling off is due to insufficient vertical fixing force of melted solder on the component during soft melting, which can be attributed to the increase of component weight, poor solderability of the component, insufficient wettability of the flux or insufficient amount of solder, among which the first factor is the most fundamental one. If the components still fall off after the following three factors are improved, SMT adhesive must be used. Obviously, the use of adhesives will make the self alignment effect of components worse during soft melting.
Incomplete welding
Incomplete solder bridge is formed between adjacent leads. Generally, all factors that can cause the solder paste to collapse will lead to underfill. These factors include:
1. The heating rate is too fast;
2. The thixotropy of solder paste is too poor or the viscosity of solder paste recovers too slowly after shearing;
3. Metal load or solid content is too low;
4. The particle size of powder is too wide;
5. The flux surface tension is too small. However, the collapse does not necessarily lead to underfill. During soft melting, the melted underfill solder may be disconnected under the push of surface tension, and the solder loss will make the underfill problem more serious. In this case, the excessive solder accumulated in a certain area due to solder loss will make the molten solder become too much and not easy to break.
In addition to the factors that cause the solder paste to collapse, the following factors also cause the common causes of incomplete welding:
1. Compared with the space between solder joints, too much solder paste is deposited;
2. The heating temperature is too high;
3. The solder paste is heated faster than the circuit board;
4 The wetting speed of flux is too fast;
5 The vapor pressure of welding flux is too high;
6. The solvent composition of the flux is too high;
7. The softening point of the flux resin is too low.
Continue wetting
Intermittent wetting of the solder film refers to the appearance on the smooth surface. This is because the solder surface can adhere to most solid metal surfaces, and there are some points that are not wetted under the melted solder coating. Therefore, when the surface is initially covered with melted solder, the phenomenon of continuous wetting will occur. The metastable molten solder coating will shrink under the action of the minimum surface energy driving force, and soon will aggregate into separated pellets and ridge bald objects. Further wetting can also be caused by the gas released when the part is in contact with the molten solder. Water released due to thermal decomposition of organic matter or hydration of inorganic matter will generate gas. Water vapor is the most common component of these related gases. At the welding temperature, water vapor has a strong oxidation effect and can oxidize the surface of the molten solder film or the interface under some surfaces (typical example is the metal oxide surface at the interface of the molten solder). It is common that higher welding temperature and longer residence time will lead to more serious intermittent wetting, especially in the base metal. The increase of reaction speed will lead to more violent gas release. At the same time, longer residence time will also extend the gas release time.
The above two aspects will increase the amount of gas released, and the methods to eliminate the phenomenon of continuous wetting are:
1. Reduce the welding temperature;
2. Shorten the residence time of soft melting;
3. Adopt flowing inert atmOSPhere;
4. Reduce pollution.
Low residue
For the soft melting process without cleaning, in order to obtain decorative or functional effects, low residues are often required. Examples of functional requirements include "detecting and testing the surfacing layer through the flux residues tested in the circuit and conducting electrical contact between the insertion joint and the through hole adjacent to the soft melting solder joint". More flux residues often lead to excessive residue coverage on the metal surface to be electrically contacted, This will hinder the establishment of electrical connections. With the increasing density of circuits, this problem has attracted more and more attention.
Obviously, low residue solder paste without cleaning is an ideal solution to meet this requirement. However, the necessary condition of soft melting related to this makes this problem more complicated. In order to predict the welding performance of low residue solder paste in different levels of inert soft melt atmosphere, a sEMI empirical model is proposed. This model predicts that with the decrease of oxygen content, the welding performance will rapidly improve, and then gradually become stable. The experimental results show that with the decrease of oxygen concentration, the welding strength and the wetting ability of solder paste will increase. In addition, the welding strength will also increase with the increase of solid content in the flux. The model proposed by the experimental data is comparable, and strongly proves that the model is effective and can be used to predict the welding performance of solder paste and materials. Therefore, it can be asserted that in order to successfully use low residue solder without cleaning in the welding process, inert soft melting atmosphere should be used.
clearance
Gap refers to that no solder joint is formed between the component lead and the solder joint of the circuit board. Generally speaking, this can be attributed to the following four reasons:
1. Insufficient solder deposition;
2. Poor coplanarity of leads;
3. Insufficient wetting;
4. Solder loss.
This is caused by the slump of solder paste on the pre tinned printed circuit board, the wicking effect of the lead or the through hole near the solder joint. The coplanarity problem of the lead is a particularly interesting problem of the new lightweight QFP Quadflatpacks with 12 mil (um) spacing. In order to solve this problem, a method of pre coating solder joints with solder before assembly is proposed, This method is to expand the size of local solder joints and form a controllable local welding area along the bulged solder pre coverage area, thereby compensating for the change of lead coplanarity and preventing gaps. The lead's inhaling effect can be solved by slowing down the heating speed and making the bottom surface heated more than the top surface. In addition, the solder with slower wetting speed is used, Higher activation temperature or solder paste that can delay melting (such as solder paste mixed with tin powder and lead powder) can also minimize the wicking effect. Before finishing the circuit board with tin lead coating, covering the connection path with solder mask can also prevent the wicking effect caused by nearby through-hole.
Solder balling
Solder balling is the most common and thorny problem, which refers to the solidification of solder into balls of different sizes near the main solder pool in the soft melting process; In most cases, these particles are composed of solder powder in the solder paste. Solder balling causes people to worry about the occurrence of circuit short circuit, electric leakage and insufficient solder on the welding point. With the development of fine pitch technology and welding methods without cleaning, people increasingly urgently require the use of SMT process without solder balling.
The causes of solder balling include:
1. Oil stains caused by improper circuit printing process;
2. Solder paste is excessively exposed to oxidizing environment;
3. Solder paste is excessively exposed to damp environment;
4. Improper heating method;
5. The heating speed is too fast;
6. The preheating section is too long;
7. Interaction between solder mask and solder paste;
8. Insufficient flux activity;
9. Excessive oxide or pollution of welding powder;
10. Too many dust particles;
11. Inappropriate volatiles are mixed in the flux during specific soft melting treatment;
12. Solder slump caused by improper solder paste formula;
13. Unpack the solder paste before it is fully recovered to room temperature;
14. The printing thickness is too thick, causing "collapse" to form solder balls;
15. The metal content in the solder paste is low.
Solder bead
Solder bead formation is a special phenomenon when solder paste and SMT process are used. To put it simply, solder bead refers to those very large solder balls with (or without) small solder balls stuck on them. They are formed around extremely low foot supporting components such as chip capacitors. Solder bead formation is caused by flux exhaust, which exceeds the cohesion of the solder paste in the preheating stage. The exhaust promotes the formation of isolated agglomerates of the solder paste under the low clearance element. During soft melting, the melted isolated solder paste emerges again from the element and coalesces.
The causes of welding bead formation include:
1. The thickness of the printed circuit is too high;
2. Too much overlap between solder joints and components;
3. Too much solder paste is applied under the element;
4. The pressure of placement element is too high;
5. The temperature rises too fast during preheating;
6. The preheating temperature is too high;
7. Moisture is released from components and solder resisters;
8. The activity of the flux is too high;
9. The powder used is too fine;
10. The metal load is too low;
11. Too much solder paste slump;
12. Too many welding powder oxides;
13. Insufficient solvent vapor pressure.
Perhaps the easiest way to eliminate solder is to change the template pore shape so that there is less solder paste sandwiched between the low leg support component and the solder joint.
Welding fillet welding lifting
The lifting of welding fillet weld refers to that the lead wire and welding fillet weld are completely lifted from the welding point of quad flat integrated circuit (QFP) with fine circuit spacing after wave soldering, especially near the edges and corners of components. One possible reason is the mechanical stress on the lead wire during sampling inspection before wave soldering, or the mechanical damage during processing the circuit board. During sampling inspection before wave soldering, use a pair of tweezers to scratch the leads of QFP components to determine whether all the leads have been soldered during the baking process; The result is the generation of misaligned weld toes, which can be seen from the top to the bottom. If the heating under the board causes partial secondary soft melting on the interface between the welding area/fillet weld, then lifting the lead and fillet weld from the circuit board can reduce the internal stress. One way to prevent this problem is to conduct sampling inspection after wave soldering (rather than before wave soldering).
Tombstone
A tombstoning means that one end of a leadless component (such as a chip capacitor or resistor) leaves the substrate, and even the entire component is supported on one end of it.
Tombstoning, also known as Manhattan effect, Drawbridging effect or Stonehenge effect, is caused by uneven lubrication at both ends of the soft melt element; Therefore, the unbalanced surface tension of molten solder is applied on both ends of the component. With the development of SMT miniaturization, electronIC components become more and more sensitive to this problem.
Reasons for this situation:
1. Uneven heating;
2. Component problems: different shapes, too light weight, different solderability;
3. The thermal conductivity of the substrate material is poor, and the thickness uniformity of the substrate is poor;
4. The heat capacity of the pad varies greatly, and the solderability of the pad varies greatly;
5. The uniformity or activity of the flux in the solder paste is poor, the thickness of the solder paste on the two bonding pads differs greatly, the solder paste is too thick, the printing accuracy is poor, and the dislocation is serious;
6. The preheating temperature is too low;
7. Poor mounting accuracy and serious component offset.
Bad balling of Ball Grid Array (BGA)
BGA balling often encounters defects such as incomplete solder, misaligned solder balls, solder ball leakage and insufficient solder amount, which are usually caused by insufficient fixing force or self setting force on the ball during soft melting. Insufficient fixation force may be caused by low viscosity, high barrier thickness or high air release speed; However, the lack of self setting force is generally caused by weak flux activity or low solder content.
BGA balling can be realized by using solder paste alone or by using solder ball with solder paste and solder ball with flux; The correct and feasible method is to use the overall preform together with flux or solder paste. The most common method seems to be to use the solder ball and solder paste together, and the ball forming process of tin 62 or 63 ball welding has produced excellent results. When flux is used for tin 62 or tin 63 ball welding, the defect rate increases with the decrease of flux viscosity, solvent volatility and spacing size, as well as with the increase of flux deposition thickness, flux activity and solder joint diameter. In the ball welding system where solder paste is used for high temperature melting, no solder ball leakage is observed, and its accuracy increases with the solder paste deposition thickness and solvent volatility, The activity of flux, the size and solderability of solder joints, and the increase of metal load increase. When using Sn63 solder paste, the viscosity, spacing, and soft melting section of solder paste have little effect on the balling rate at high melting temperature. When the conventional printing release process is required, the solder paste that is easy to release is critical to the separate balling of solder paste. The ball forming process of integral preforming is also very promising. Reducing the thickness and width of solder links is also very important to improve the success rate of balling.
summary
The reflow soldering of solder paste is the main method of plate interconnection in the SMT assembly process. The main problems affecting reflow soldering include: the fixation of bottom components, incomplete soldering, intermittent wetting, low residue, gap, solder balling, solder bead, lifting of welding fillet weld, poor balling of TombstonengBGA, formation of pores, etc. The problems are not limited to this. The problems not mentioned in this article include leaching, intermetallics, non wetting, Twist, lead-free welding, etc. Only by solving these problems, reflow welding, as an important SMT assembly method, can be successfully retained in the era of ultra-fine spacing.
然后
联系
电话热线
13410863085Q Q
微信
- 邮箱