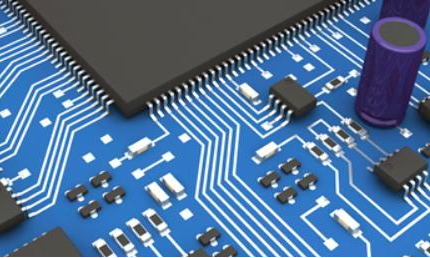
Metal core PCB is not very common in consumer products, but it is ubiquitous in industries, aerOSPace, lighting systems, power electronICs and other fields requiring high reliability. High power systems generate a lot of heat and need to be quickly removed to prevent component failure. SIMilarly, low power systems may be exposed to high heat, and heat needs to be removed quickly to prevent damage to circuit boards and components.
The metal core (including DFM) follows many of the same basIC design rules as a typical PCB on FR4. If you want to design new products in any of the above areas, you may need to use metal core plates to control the temperature. In this paper, we will briefly introduce the structure of metal core PCB and some important design points to be considered before planning to use metal core PCB design. These boards contain special manufacturing requirements, but the appropriate design company can help meet these requirements and ensure that PCB can be mass produced.
Application of Metal Core PCB design
Metal core PCBs can find their place in almost any application that generates a lot of heat when the equipment is running. These plates are not an ideal alternative to ceramics because they are a lower cost option and they provide a higher thermal conductivity that removes heat from important components. They are often a starting point when looking for circuit boards for systems with high heat dissipation. Some applications of metal core PCB include:
LED lighting unit: usually, a plate with high-power LED is manufactured on a metal core PCB. These boards provide a solid base for high power LEDs (SMD and through holes) while dissipating high heat into the metal core board.
Power conversion and management: hybrid electric vehicles, industrial equipment, base station telecommunications equipment and municipal power distribution systems all operate at high power. In these areas, metal core PCBs are common.
Solar equipment: Solar equipment needs to be particularly rugged and operate at high temperatures and high DC voltage/current. Similar PCB designs can be implemented in geothermal facilities.
Military (for example, submersible, aircraft): metal core PCB can rapidly dissipate heat, keeping electrons away from electronic equipment that may be located near high heat sources such as engines or exhaust systems.
In many other areas, high reliability and structural stiffness are also critical, making metal core plates an excellent choice. Once you start to study the stacking and layout requirements of these boards, it becomes less obvious how to actually design them. Can we make multi-layer metal core plates? Can I have both sides? How are vias handled during manufacturing? These are important issues related to DFM of metal core PCB.
DFM for metal core PCB
As with other PCBs, if you want to ensure a successful manufacturing run, you need to follow specific DFM guidelines. The process adopted by the metal core plate is different from the typical PCB lamination process involving glass braided laminate, so they tend to adopt different DFM rules. The following figure shows a typical stack of double-sided metal core PCBs.
Note that the stack can be technically adapted to be a Multilayer board in which there are multiple dielectrics on each side of the metal core. Alternatively, you can make the circuit board single sided, exposing the back of the metal core. When designing metal core PCB, the following are the manufacturing points to be noted:
Metal core grounding
The metal backing on the PCB can work like a large ground plane or a large radiator. If the board needs to use high-speed/high-frequency circuit blocks, use the back metal plate as a larger ground plane to provide some shielding. If the power plane is used on the board, it can also provide some planar capacitance.
In addition, the metal core can be used as a large radiator, especially if exposed. The latter aspect is very useful when it is necessary to install plates near high heat sources. In this case, when connecting the top side to the standard power supply, it is better not to ground the back side. This prevents ground loops. This also dissipates heat directly into the very large radiator, which helps to reduce the surface temperature.
Holes in single panel
The hole can be placed on the metal core PCB, which can be used as a mounting hole or a standard through hole on the double-sided board. If holes are used only for mounting through hole assemblies on a single panel, they should not be plated to prevent short circuits. This is accomplished by drilling holes in the mounting holes and filling the holes with non-conductive epoxy resin or gel. Then, plug the hole so that it can be installed on the upper layer.
Holes in double-sided boards
In double-sided metal core PCB, some components may be installed on both sides, and electroplated vias need to be placed between signal layers. Electroplated through-hole is formed by pre drilling → insulating filler → re drilling → electroplating process, so some difficulties will be encountered in manufacturing. This process takes additional time and costs, but it is designed to prevent through hole short circuits. In PCB layout, it is better to use a solder pad to represent the area around the through hole that needs to be filled with insulating filler material. Make sure to adjust the size of the through hole anti welding pad to comply with IPC-2221 standard.
DFM has little difference from standard PCB in other aspects of metal core PCB design, although CAD tools are not used to design these boards. The front-end of power electronic equipment needs to follow some SMAll rules, especially IPC-2221 (creepage and release rules), as well as other national defense and aerospace standards.
然后
联系
电话热线
13410863085Q Q
微信
- 邮箱