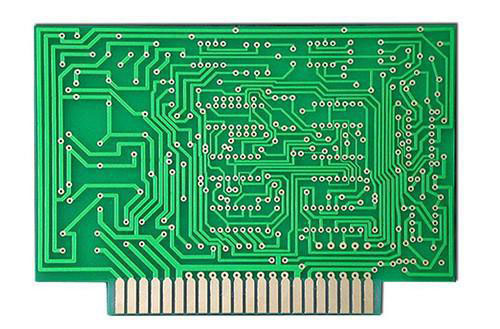
What should be paid attention to in multi-layer PCB circuit board proofing
1. Better material selection
With the development of high performance and multi-function of electronIC components, high frequency PCBs and high-speed signal transmission is also brought. Therefore, low dielectrIC constant and dielectric loss of electronic circuit materials, low CTE, low water absorption and better high-performance copper clad laminate materials are required to meet the processing and reliability requirements of multi-layer PCBs. The commonly used sheet suppliers mainly include A series, B series, C series and D series. High resin content prepreg is selected for high layer thick copper circuit board. The glue flow of interlayer prepreg is enough to fill the inner layer graphics. If the insulating medium layer is too thick, the finished board is prone to be super thick. Otherwise, if the insulating medium layer is too thin, it is easy to cause quality problems such as dielectric layering and high-voltage test failure. Therefore, the selection of insulating medium materials is extremely important.
2. Pressing
The main factors considered in the design of the laminated structure are the heat resistance, voltage resistance, glue filling amount and dielectric layer thickness of the material, which should follow the following main principles.
(1) The prepreg and core board manufacturers must be consistent. In order to ensure reliability, single 1080 or 106 prepreg shall not be used for all layers of prepreg (unless the customer has special requirements). If the customer has no requirements for media thickness, the thickness of media between layers must be ≥ 0.09mm according to IPC-A-600G.
(2) When customers require high TG plates, core plates and prepreg shall be made of corresponding high TG materials.
(3) The inner substrate is 3OZ or above, and the sEMI solidified sheet with high resin content is selected, such as 1080R/C65%, 1080HR/C 68%, 106R/C 73%, 106HR/C76%; However, the structural design of 106 high glue semi curing sheet shall be avoided as far as possible to prevent multiple 106 semi curing sheets from overlapping. Because the glass fiber yarn is too thin, it will collapse in the large base material area, which will affect the dimensional stability and delamination.
(4) If the customer has no special requirements, the thickness tolerance of the interlayer medium layer is generally controlLED by+/- 10%. For the impedance plate, the thickness tolerance of the medium is controlled by IPC-4101 C/M level tolerance. If the impedance influencing factors are related to the thickness of the base material, the tolerance of the plate must also be controlled by IPC-4101 C/M level tolerance.
3. Interlayer alignment control
For the accuracy of the size compensation of the inner core plate and the control of the production size, it is necessary to accurately compensate the graphic size of each layer of the high-rise board through the data and historical data experience collected in the production for a certain period of time to ensure the consistency of the rise and fall of each layer of the core plate. Select high-precision and reliable interlayer positioning mode before pressing, such as four groove positioning (Pin LAM), hot melt and rivet combination. Setting appropriate pressing process procedures and daily maintenance of the press is the key to ensure the pressing quality, control the glue flow and cooling effect, and reduce the interlayer dislocation. The inter layer alignment control needs to be comprehensively considered from the inner layer compensation value, pressing positioning mode, pressing process parameters, material characteristics and other factors.
5. Inner line process
Because the analytical ability of traditional exposure machine is 50 μ M or so, for the production and manufacture of high-rise boards, the laser direct imaging machine (LDI) can be selected to improve the graphic analysis ability, which reaches 20 μ M or so. The alignment accuracy of traditional exposure machine is ± 25 μ m. The inter storey alignment accuracy is greater than 50 μ m。 Using high-precision alignment exposure machine, the graphic alignment accuracy can be increased to 15 μ M, and the inter floor alignment accuracy is controlled by 30 μ Within m, the alignment deviation of traditional equipment is reduced, and the inter storey alignment accuracy of high-rise slabs is improved.
In order to improve the etching capacity of the line, it is necessary to give appropriate compensation to the width of the line and the pad (or ring) in the engineering design, as well as more detailed design consideration to the compensation amount of special graphics, such as return lines, independent lines, etc. Confirm whether the design compensation for inner layer line width, line distance, isolation ring size, independent line, hole to line distance is reasonable, or change the engineering design. It is required to pay attention to whether the design compensation of independent line and impedance line is sufficient if there are impedance and inductive reactance design requirements. The parameters shall be controlled during etching. Batch production can only be carried out after the first article is confirmed to be qualified. In order to reduce the side etching, it is necessary to control the composition of each liquid medicine in the etching solution within the optimal range. The traditional etching line equipment has insufficient etching capacity. The equipment can be technically modified or high-precision etching line equipment can be imported to improve the uniformity of etching and reduce the problems such as rough edges and unclean etching.
6. Pressing process
At present, the interlayer positioning methods before pressing mainly include: four slot positioning (Pin LAM), hot melt, rivet, hot melt and rivet combination. Different product structures adopt different positioning methods. For the high-rise board, the four slot positioning method (Pin LAM) or fusion+riveting method is used for manufacturing. The OPE punching machine punches the positioning holes, and the punching accuracy is controlled within ± 25 μ m。 During fusion, X-RAY shall be used to check the lamination deviation of the first plate, and only when the lamination deviation is qualified can batch production be made. During batch production, it is necessary to check whether each plate is melted into the unit to prevent subsequent lamination. The pressing equipment adopts high-performance matching press to meet the inter layer alignment accuracy and reliability of high-rise plates.
According to the laminated structure and materials used for multi-layer PCBs, study the appropriate pressing program, set the optimal heating rate and curve, and appropriately reduce the heating rate of laminated boards, extend the high temperature curing time, so that the resin can flow and solidify fully, and avoid sliding plate, interlayer dislocation and other problems during the pressing process. Plates with different TG values cannot be the same as grate plates; Plates with ordinary parameters cannot be mixed with plates with special parameters; To ensure the rationality of the given expansion and contraction coefficient, different plates and prepreg have different properties, so the corresponding plate prepreg parameters shall be used for pressing, and the process parameters shall be verified for special materials that have never been used.
7. Drilling process
Due to the super thickness of the plates and copper layers caused by the superposition of layers, the drill bit is seriously worn and is easy to break, and the number of holes, falling speed and rotating speed are appropriately reduced. Accurately measure the expansion and contraction of the board to provide accurate coefficients; The number of layers ≥ 14, hole diameter ≤ 0.2mm or hole to line distance ≤ 0.175mm, and the drilling machine with hole location accuracy ≤ 0.025mm is used for production; diameter φ Step by step drilling is adopted for the hole diameter above 4.0mm, and the thickness diameter ratio is 12:1. Step by step drilling is adopted for the production of positive and negative drilling; Control the drilling flaring and hole diameter. Try to use a new drilling tool or a ground 1 drilling tool to drill holes in the high-rise slab, and the hole diameter shall be controlled within 25um. In order to improve the drilling burr problem of thick copper plates in high-rise buildings, after batch verification, high-density backing plates are used, the number of laminated plates is one, and the drill bit grinding tiMES are controlled within three times, which can effectively improve the drilling burr, as shown in Figure 2 and Figure 3.
Backdrilling technology is an effective method to improve signal integrity for high frequency PCBs, high-speed and mass data transmission PCB boards. The back drilling mainly controls the length of the residual stub, the consistency of the hole positions of the two boreholes, and the copper wire in the hole. Not all drilling machine equipment has the back drilling function, so it is necessary to upgrade the technology of drilling machine equipment (with back drilling function), or purchase the drilling machine with back drilling function. The back drilling technology applied in the industry related literature and mature mass production mainly includes: traditional depth control back drilling method, back drilling in signal feedback layer in the inner layer, and back drilling in depth calculated according to the plate thickness ratio, which will not be repeated here.
然后
联系
电话热线
13410863085Q Q
微信
- 邮箱