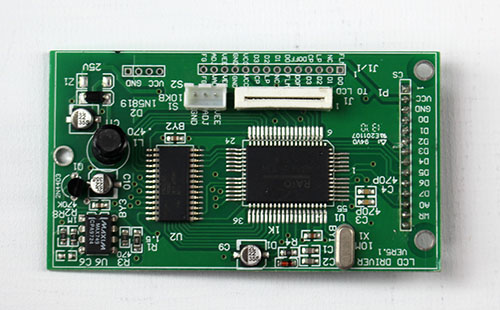
The circuit board manufacturer explained: How to prevent PCB from warping?
1、 Why is the PCB required to be very flat
In the automatIC insertion line, if the printed board is not flat, it will lead to inaccurate positioning, components cannot be inserted into the holes of the board and surface mount pads, or even damage the automatic insertion machine. The boards with components are bent after welding, and it is difficult to cut the component legs in order. The board can not be instalLED on the chassis or the socket inside the machine, so it is also very troublesome for the assembly plant to encounter the board warping. At present, printed boards have entered the era of surface mounting and chip mounting, and assembly plants must increasingly strict requirements on board warping.
2、 Standard and test method for warpage
According to American IPC-6012 (1996 edition)<<Qualification and Performance Specification for Rigid Printed Boards>>, the maximum allowable warpage and twist for surface mounted printed boards is 0.75%, and 1.5% for other kinds of boards. This improves the requirements for surface mounted printed boards compared with IPC-RB-276 (1992). At present, the allowable warpage of each electronic assembly plant, regardless of double-sided or multi-layer, is usually 0.70-0.75% with a thickness of 1.6mm. For many SMT and BGA boards, the requirement is 0.5%. Some electronic factories are encouraging to raise the standard of warpage to 0.3%. The method of testing warpage shall comply with GB4677.5-84 or IPC-TM-6502.4.22B. Put the printed board on the verified platform, insert the test pin at the place with the maximum warpage, and calculate the warpage of the printed board by dividing the diameter of the test pin by the length of the curved edge of the printed board.
3、 Anti warping plate during manufacturing
1. Engineering design: Precautions for PCB design:
A. The arrangement of interlayer prepreg shall be symmetrical. For example, for six ply boards, the thickness between 1~2 and 5~6 layers shall be consistent with the number of prepreg sheets, otherwise it is easy to warp after lamination.
B. Multilayer core board and prepreg shall be from the same supplier.
C. The area of the outer layer A and B lines should be as close as possible. If the A side is large copper and the B side only runs a few wires, this kind of printed board is easy to warp after etching. If the difference between the line areas on both sides is too large, some independent grids can be added on the thin side for balance.
2. Drying plate before blanking:
The purpose of drying the copper clad plate (150 ° C, 8 ± 2 hours) before blanking is to remove the moisture in the plate, and at the same time, fully solidify the resin in the plate, further eliminate the residual stress in the plate, which is helpful to prevent the plate from warping. At present, many double-sided and multilayer boards still adhere to the process of drying boards before or after blanking. However, there are some exceptions to this rule. At present, the drying time of PCB plants is also inconsistent, ranging from 4 to 10 hours. It is recommended to decide according to the grade of PCB produced and the customer's requirements for warpage. The two methods are both feasible, and it is recommended to bake the board after shearing. The inner plate shall also be baked.
3. Longitudinal and latitudinal directions of prepreg:
After laminating, the shrinkage of the prepreg in the warp and weft direction is different. The warp and weft directions must be distinguished when blanking and laminating. Otherwise, it is easy to cause warping of the finished board after lamination, and it is difficult to correct even if the pressure is applied to bake the board. Many reasons for the warping of Multilayer boards are due to the disorderly overlapping of the warp and weft directions of the prepreg during lamination.
How to distinguish longitude and latitude? The roll up direction of the rolled prepreg is the warp direction, while the width direction is the weft direction; For copper foil, the long side is in the weft direction and the short side is in the warp direction. If you are not sure, you can check with the manufacturer or supplier.
4. Stress relief after lamination:
Take out the multilayer board after hot pressing and cold pressing, cut or mill off the burrs, and then place it flat in the oven at 150 ℃ for drying for 4 hours to gradually release the stress in the board and completely cure the resin. This step cannot be omitted.
5. The sheet needs to be straightened during electroplating:
When the 0.4~0.6mm ultra-thin multilayer board is used for plate surface electroplating and graphic electroplating, special clamping rollers shall be made. After the thin plate is clamped on the fly bar on the automatic electroplating line, a round bar shall be used to string the clamping rollers on the whole fly bar, so as to straighten all the plates on the roller, so that the plates after electroplating will not be deformed. Without this measure, the thin plate will be bent and difficult to repair after electroplating 20 to 30 micrometers of copper layer.
6. Cooling of plates after hot air leveling:
When the PCB is leveled by hot air, it will be impacted by the high temperature of the solder bath (about 250 ℃). After being taken out, it should be put on the flat marble or steel plate for natural cooling, and then sent to the post-processing machine for cleaning. This is good for warping prevention of boards. Some factories, in order to enhance the brightness of the lead tin surface, put the boards into cold water immediately after hot air leveling, and take them out for post-treatment after a few seconds. This impact of one hot and one cold may cause warping, delamination or blistering of some types of boards. In addition, air floating bed can be installed on the equipment for cooling.
7. Treatment of warped boards:
In a well managed factory, 100% flatness inspection will be conducted for printed boards during final inspection. All unqualified boards will be picked out and put into an oven, dried at 150 ℃ and under heavy pressure for 3-6 hours, and naturally cooled under heavy pressure. Then, take out the boards by pressure relief and check the flatness. This can save some boards. Some boards need to be baked for two or three times before leveling.
PCB manufacturers, PCB designers and PCBA manufacturers explain how to prevent PCB from warping.
然后
联系
电话热线
13410863085Q Q
微信
- 邮箱