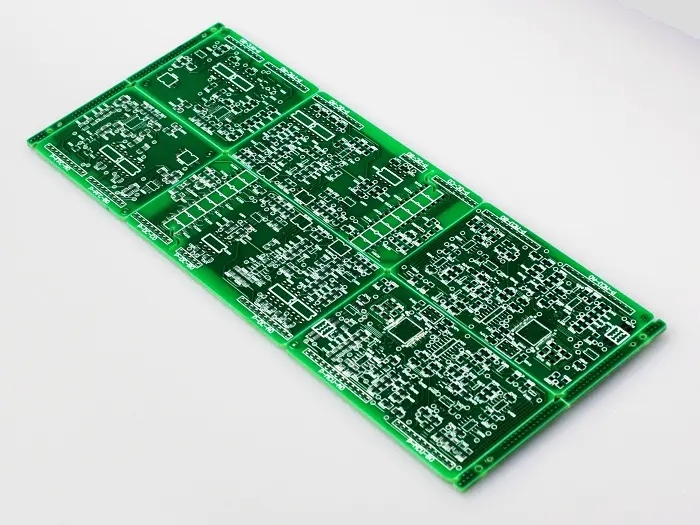
Problems easy to occur during electrIC welding of PCBA circuit board
In the whole process of PCBA circuit board electric welding, because of the hazards of welding materials, processing technology, staff and other factors, PCBA circuit board electric welding will be weak.
① Excessive residual PCBA circuit board
The excessive residue on the plate may be due to the heating before welding or the heating temperature is too low, and the temperature of the tin furnace is insufficient; The circuit board speed is too fast, and antioxidant and antioxidant oil are added to the antioxidant; Too much welding fluid is applied; The leg of the component is inversely proportional to the pore plate (with large porosity), so the flux is accumulated. During the application of solution aids, it is not easy to add paint thinner for a long time.
② Etching, green ingredients, blackened pad
The main reason is that the heating is not sufficient, there are many residues of welding fluid and too many harmful substances; Apply the flux to be cleaned, but do not clean after electric welding. PCBA circuit board manufacturers have high assembly relative density, SMAll electronic equipment and light weight. The volume and net weight of patch type components can only be about 1/10 of that of traditional plug-in components. After SMT is generally selected, the volume of electronic equipment becomes 40%~60% smaller, and the net weight is reduced by 60%~80%.
③ Virtual junction
Virtual electric welding is a very common disadvantage, which is very harmful to PCB. PCBA Circuit board manufacturers have high assembly relative density, small electronic equipment and light weight. The volume and net weight of patch type components can only be about 1/10 of that of traditional plug-in components. After SMT is generally selected, the volume of electronic equipment becomes 40%~60% smaller, and the net weight is reduced by 60%~80%. The relative density of PCBA assembly is high, the size of electronic equipment is small, and the weight is relatively light. The volume and net weight of patch type components can only be about 1/10 of that of traditional plug-in components. Generally, after SMT is selected, the volume of electronic equipment decreases by 40%~60%, and the net weight decreases by 60%~80%. The coating amount of flux is mainly small or uneven.
Some weld layers or weld legs will be seriously oxidized by air; PCBA circuit board wiring is unscientific; The foam plastic pipe is blocked, and the polyurethane foam is uneven, resulting in the uneven coating of the welding fluid; The actual operation of hand DIPping tin is not good; Unscientific chain alliance trend.
④ Cold welding
The surface of spot welding is the way of water tofu. The key is that the temperature of the electric iron is not enough, or the electric welding of the welding materials before the welding materials are dried and solidified. The compressive strength of the spot welding is not high, and the conductivity is weak. It is very easy for the components to turn on the power circuit because of the external force
⑤ Spot welding whitening
Firm and low. PCBA circuit board assembly has high relative density, small size and light weight of electronic equipment. The volume and net weight of chip mounted components can only be about 1/10 of that of traditional plug-in components. After SMT is generally selected, the volume of electronic equipment will be reduced by 40%~60%, and the net weight will be reduced by 60%~80%. Generally, it is caused by too high temperature or too long heating time of electric soldering iron. Disadvantages The compressive strength of spot welding is not enough, and it is very easy to cause the invalidity of components due to external force.
⑥ Disengaging of cushion
The key reason is that the pad is separated from the printed circuit board after withstanding high temperature, and defective spot welding is easy to cause damage to components.
⑦ Tin bead
Processing technology: the heating temperature is low (the organic solvent of the solution is not completely evaporated), the plate speed is fast, which can not reach the actual heating effect, the oblique angle of view of the drive chain is not very good, there is a bubble between the tin liquid and the pcb, which causes tin beads after the bubble cracks; Poor practical operation; Wet and cold office environment; PCBA circuit board problem: the surface is wet and cold, and there is water. The design scheme of holes in the operation of PCBA circuit board is unscientific, resulting in gas between PCBA circuit board and tin liquid; PCB design scheme is unscientific, and components are too concentrated to cause gas. There are many reasons for poor electric welding of PCBA circuit board, and each processing process must be strictly controlLED to reduce the post hazard of previous processing processes.
PCB manufacturers, PCB designers and PCBA manufacturers will explain the problems that are easy to occur in the welding process of PCBA PCB.
然后
联系
电话热线
13410863085Q Q
微信
- 邮箱