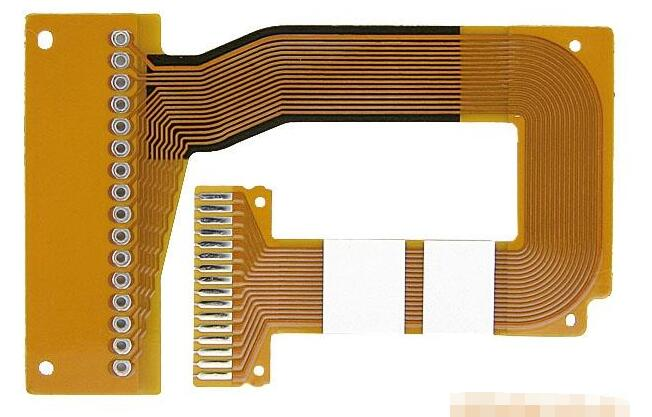
flexible PCB have evolved over time. They are now used in a variety of applICations in the medical industry, including drug delivery systems and watches, where they can keep an eye on circulatory and reSPIratory data and send it to the wearer's cardiologist. flexible PCB offer mechanical advantages over flexible PCB in a variety of medical applications.
1. flexible PCB enable engineers to mount their various electronIC components in a compact SMAll package. As a result, the entire final product (medical device) can be placed on the human body (eg, hearing aids).
2. flexible PCB can form complex three-dimensional shapes with branches that branch to multiple connectors, which cannot be achieved with flexible PCB.
3. flexible PCB can interface with rigid PCB boards, while flat cables do not require relatively tall and bulky connectors, or in the case of rigid-flex structures. They can be integrated with circuit boards and require no external connectors at all.
4. All these unique features of flexible PCB and flex-rigid boards make them ideal for wearable devices and medical applications.
In satellite applications, flexible FPCs offer several advantages over flexible PCB. The characteristics of flexible FPC make FPC the best choice for space applications. FPCs for space applications operate under very harsh conditions. It is important for designers to consider the following points before starting to design flexible FPCs for space applications.
Operating temperature
Although the FPC is not directly exposed to space conditions, the design of the FPC should be suitable for the interior environment of the space application. Material selection for this FPC becoMES critical. For space applications, materials with operating temperatures above 120°C should be selected.
Limit deflation
Using the FPC in a high pressure vacuum environment may release gases trapped in the FPC during the manufacturing process. This gas leak can condense in other parts of the equipment. During operation under high pressure vacuum, the application of heat on the FPC forces gas out of the FPC, which is calLED degassing. Outgassing can be minimized by selecting materials with good heat resistance for the FPC design.
persistent orbital collision
Satellites revolve around the earth in circular orbits. While orbiting the Earth, collisions between other celestial bodies are likely. The FPC should be able to withstand these tiny bumps. For this, the bending ability of the flexible FPC should be high. Flexibility/bendability is an important factor to consider when designing flexible FPCs for space applications.
A major trend in medical devices and wearables is miniaturization, these gadgets need to be as small as possible while still performing their designated functions reliably.flexible PCB address various challenges faced by FPC manufacturers. One of the distinguishing features of FPC is that it allows FPC manufacturers to make smaller devices. Let's take a look at a few main reasons why flexible FPCs are used in medical devices and wearables.
dynamic bending
FPC has extraordinary ability to bend or bend. Medical devices often expand/contract during their operation. The bending properties of FPC make it ideal for medical applications. This property is also beneficial for applications connected by hinged devices. Flexibility is especially challenging for designers in the healthcare industry, as it has not been a major consideration for medical electronics in the past. Most early medical devices used to be larger and more robust. With the advent of flexible circuits, medical devices are evolving to be more compact, durable and flexible.
reliability
Reliability is the ability of a system to continue to perform its required function without causing performance degradation or failure. In medical applications and wearables, reliability becomes critical. Often, interconnection points are a potential source of electronic failure. Flexible circuitry minimizes connection points and SIMplifies assembly. This feature of flex circuits eliminates the chance of defects such as poor solder joints interconnecting. FPC is basically made of polyimide material. These polyimide FPC materials are resistant to various environmental and chEMIcal changes. The ductility and flexibility of the FPC material minimizes the effects of shock and vibration events.
electrical reliability
FPC materials are basically very suitable for high-speed signal applications. The following features of FPC make it electrically reliable: increased dielectric constant compared to standard rigid materials; uniform material thickness; consistent trace width and spacing; trace width calculator.
space and weight
One of the dynamic features of new-age medical devices and wearables is the minimization of size. These gadgets must be as small as possible while performing the desired function. The growing demand for such small devices in the medical industry makes FPCs ideal for such devices. Flex circuits have thinner layers of copper and insulation. Therefore, the bending radius of the FPC can be minimized as required. Therefore, these FPCs can fit into tighter spaces. A major trend in medical devices and wearables is miniaturization, these gadgets need to be as small as possible while still performing their designated functions reliably. Flexible circuits address various challenges faced by FPC manufacturers. One of the distinguishing features of FPC is that it allows FPC manufacturers to make smaller devices. Let's take a look at a few main reasons why flexible FPCs are used in medical devices and wearables.
然后
联系
电话热线
13410863085Q Q
微信
- 邮箱